Група 05-19
Тема: "Метали і
сплави".
Вуглеце́ва сталь — сталь, що містить вуглець (до 2%) поряд з іншими домішками. На відміну від чистих залізовуглецевих сплавів в ній, крім заліза і вуглецю, є постійні домішки (марганець, кремній, сірка, фосфор, кисень, азот, водень) і домішки випадкові (хром, мідь, нікель тощо).
Термічна обробка полягає у зміні структури металів і сплавів при нагріванні, видержуванні та охолодженні, згідно спеціального режиму, і тим самим, у зміні властивостей останніх. В основі термічної обробки сталей лежить перекристалізація аустеніту при охолодженні. Перекристалізація може відбутися дифузійним або бездифузійним способами. У залежності від переохолодження аустеніт може перетворюватися у різні структури з різними властивостями.
Повний дифузійний розпад аустеніту відбувається при незначному переохолодженні. У даному випадку утворюється пластинчастий перліт (механічна суміш фериту і цементиту вторинного). Якщо переохолодження збільшити до 373-393 0К, пластинки фериту і цементиту встигають вирости тільки до товщини (0,25-0,30 мнм), таку структуру називають сорбітом. Твердість сорбіту вища за твердість перліту.
Коли переохолодження досягає 453-473 0К, ріст пластинок припиняється на товщині 0,1-0,15 мнм, така структура називається трооститом. Твердість трооститу вища від твердості сорбіту.
При значному переохолодженні аустеніту (до 513 0К) дифузійний розпад його стає неможливим, перекристалізація має бездифузійний характер. У такому випадку утворюється перенасичений твердий розчин вуглецю в залізі, який називається мартенситом. Твердість мартенситу вища від твердості трооститу.
Структура перліту є рівноважною, а структури сорбіту, трооститу і мартенситу є не рівноважними.
1. Види термічної обробки
Розрізняють такі види термічної обробки: відпал, нормалізація, загартування і відпуск.
Відпал. Відпалом називають нагрівання до високих температур, видержування і повільне охолодження разом з піччю.
Розрізняють такі види відпалу: рекристалізаційний, дифузійний, на зернистий перліт, ізотермічний, повний і неповний. Відпал підвищує пластичність, зменшує внутрішні напруження, понижує твердість сталей.
Нормалізація. Нормалізацією називають нагрівання до високої температури, видержування і повільне охолодження на повітрі. Нормалізація доводить сталь до дрібнозернистої та однорідної структури. Твердість і міцність сталі після нормалізації вищі, ніж після відпалу.
Загартування сталі. Загартуванням називають нагрівання до високої температури, видержування і швидке охолодження (у воді, мінеральній оливі та інших охолоджувачах). Є такі види загартування: в одному охолоджувачі; перервне; ступінчасте; ізотермічне; поверхневе та ін. Загартування сталей забезпечує підвищення твердості, виникнення внутрішніх напружень і зменшення пластичності. Твердість збільшується у зв'язку з виникненням таких структур: сорбіт, троостит, мартенсит. Практично загартуванню піддається середньо- і високовуглецеві сталі.
Відпуск сталі. Відпуском називають нагрівання до температур нижче 973 0К, видержування і повільне охолодження на повітрі.
Розрізняють три види відпуску: низький (нагрівання до температури 473 0К; середній (573-773 0К); високий (773-973 0К). Після відпуску в деякій мірі зменшується твердість і внутрішні напруження, збільшується пластичність і в'язкість сталей. До цього приводить зміна структур після відпуску. Структура мартенситу сталі переходить відповідно в структуру трооститу і сорбіту. Чим вища температура відпуску, тим менша твердість відпущеної сталі і тим більша її пластичність та в'язкість.
Відпуск, в основному, проводять після загартування для зняття внутрішніх напружень. Низький відпуск застосовують при виготовленні різального інструменту, вимірювального інструменту, цементованих деталей та ін..; середній - при виробництві ковальських штампів, пружин, ресор; високий - для багатьох деталей, що зазнають дії високих напружень (осі автомобілів, шатуни і т.п.).
2. Основи теорії хіміко-термічної обробки
Хіміко-термічною обробкою називають насичення поверхні виробу різними елементами.
Мета хіміко-термічної обробки - надати поверхневому шару стальних деталей підвищеної твердості, зносостійкості, жаростійкості, корозійної стійкості та ін. Для цього нагріті деталі поміщають у середовище, з якого в процесі дифузії у поверхневий шар переходять деякі елементи (вуглець, азот, алюміній, хром, кремній, бор та ін.).
Такі елементи найкраще поглинаються тоді, коли вони виділяються в атомарному стані при розпаді якої-небудь сполуки. Подібний розпад найлегше відбувається у газах, тому їх і намагаються застосовувати для хіміко-термічної обробки сталі. Активізований атом елемента, що виділяється при розпаді, проникає у решітку кристалів сталі і утворює твердий розчин або хімічну сполуку. Найпоширенішими видами хіміко-термічної обробки сталі є: цементація, азотування, ціанування, дифузійна металізація.
Цементацією називається насичення поверхні стального виробу вуглецем. Після загартування такого виробу він стає твердим на поверхні і в'язким у серцевині. Цементації піддають в основному деталі, які працюють на стирання і удар одночасно. Цементація придатна для маловуглецевих сталей. Є два види цементації: цементація твердим карбюризатором і газова цементація.
Азотування - це насичення поверхневого шару виробу азотом, щоб надати йому високої твердості, підвищити зносостійкість та опір агресивним середовищем. Азотують леговану сталь, що містить алюміній, титан, ванадій, вольфрам, молібден або хром. Такі елементи, при взаємодії з азотом, утворюють тверді, стійкі в агресивних середовищах нітриди (TіN і т.п.).
Ціанування - насичення поверхневого шару виробів одночасно вуглецем і азотом. Воно буває рідинне і газове, низькотемпературне (773-9730К), високотемпературне (1073-1123 0К). Ціанування в основному застосовують для обробки інструментів із швидкорізальної сталі, підвищується твердість і корозійна стійкість.
Дифузійна металізація - насичення поверхневого шару виробу різними металами. Найбільш поширені: алютування (насичення алюмінієм); хромування (насичення хромом); нікелювання (насичення нікелем); силіціювання (насичення кремнієм). Дифузійна металізація проводиться для підвищення твердості, корозійної стійкості, жаростійкості.
3. Спосіб хіміко-термічної обробки деталей із металів та сплавів
Спосіб хіміко-термічної обробки деталей із металів та сплавів, який включає їх обробку в парогазовому середовищі з наступним охолодженням до кімнатної температури на повітрі, який відрізняється тим, що обробку проводять перегрітою парою водного розчину 5-8 % алюмохромофосфатної солі при температурі 600±20°С протягом 30-60 хвилин, а охолодження проводять до температури 200°С разом з контейнером, а потім на повітрі. Винахід відноситься до металургії, а саме до зміцнення деталей із металів та сплавів дифузійним насиченням металічної поверхні в твердому стані елементами, які підвищують експлуатаційні властивості матеріалу, та може бути використаний в машинобудуванні, для отримання зносостійких покриттів.
4. Відпал
Відпал - термічна обробка полягає в нагріванні металу до певних температур, витримка і подальшого дуже повільного охолодження разом з піччю. Застосовують для поліпшення обробки металів різанням, зниження твердості, отримання зернистої структури, а також для зняття напружень, усуває частково (або повністю) всякого роду неоднорідності, які були внесені в метал при попередніх операціях (механічна обробка, обробка тиском, лиття, зварювання), покращує структуру сталі.
Відпал першого роду . Це відпал при якому не відбувається фазових перетворень, а якщо вони мають місце, то не роблять впливу на кінцеві результати, передбачені його цільовим призначенням. Розрізняють такі різновиди відпалу першого роду: Гомогенізаціонний і рекрісталлізаціонний.
Гомогенізаціоний - це відпал з тривалою витримкою при температурі вище 950 С (Зазвичай 1100-1200 С) з метою вирівнювання хімічного складу.
Рекрісталлізаціоний - це відпал наклепаної сталі при температурі, що перевищує температуру початку рекристалізації, з метою усунення наклепаного отримання певної величини зерна.
Відпал другого роду. Це відпал, при якому фазові перетворення визначають його цільове призначення. Розрізняють такі види: повний, неповний, дифузійний, ізотермічний, світлий, нормалізований (Нормалізація), сфероідізірующій (на зернистий перліт).
Повний відпал виробляють шляхом нагрівання сталі на 30-50 ° С вище критичної точки, витримкою при цій температурі і повільним охолодженням до 400-500 ° С зі швидкістю 200 ° С на годину вуглецевих сталей, 100 ° С на годину для низьколегованих сталей і 50 ° С на годину для високолегованих сталей. Структура стали після відпалу рівноважна, стійка.
Неповний відпал проводиться шляхом нагрівання сталі до однією з температур, що знаходиться в інтервалі перетворень, витримкою і повільним охолодженням. Неповний відпал застосовують для зниження внутрішніх напружень, зниження твердості і поліпшення оброблюваності різанням.
Дифузійний відпал . Метал нагрівають до температур 1100-1200 Вє С, так як при цьому більш повно протікають дифузійні процеси, необхідні для вирівнювання хімічного складу.
Ізотермічний відпал полягає в наступному: сталь нагрівають, а потім швидко охолоджують (частіше перенесенням в іншу піч) до температури, що знаходиться нижче критичної на 50-100 С. В основному застосовується для легованих сталей. Економічно вигідний, так як тривалість звичайного відпалу (13 - 15) год, а ізотермічного відпалу (4 - 6) год полягає в нагріванні сталі вище критичної температури на 20 - 30 ° С, витримці при цій температурі і повільному охолодженні.
Світлий відпал здійснюється за режимами повного або неповного відпалу із застосуванням захисних атмосфер в печах з частковим вакуумом. Застосовується з метою захисту поверхні металу від окислення і обезуглероживания.
Нормалізація - полягає в нагріванні металу до температури на (30-50) ° С вище критичної точки і наступного охолодження на повітрі. Призначення нормалізації різна залежно від складу сталі. Замість відпалу низьковуглецевих сталі піддають нормалізації. Для середньовуглецевих сталей нормалізацію застосовують замість гарту і високого відпустки. Високовуглецеві стали піддають нормалізації з метою усунення цементітной сітки. Нормалізацію з подальшим високим відпусткою застосовують замість відпалу для виправлення структури легованих сталей. Нормалізація в порівнянні з відпалом - Більш економічна операція, так як не вимагає охолодження разом з піччю.
Загартування - це нагрів до оптимальної температури, витримка і подальше швидке охолодження з метою отримання нерівноважної структури.
У результаті загартування підвищується міцність і твердість і понижується пластичність сталі. Основні параметри при загартування - температура нагріву і швидкість охолодження. Критичною швидкістю гарту називається швидкість охолодження, забезпечує отримання структури - мартенсит або мартенсит і залишковий аустеніт.
У Залежно від форми деталі, марки сталі та необхідного комплексу властивостей застосовують різні способи гарту.
Загартування в одному охолоджувачі. Деталь нагрівають до температури загартування і охолоджують в одному охолоджувачі (вода, масло).
Загартування в двох середовищах (переривчаста гарт) - це гарт при якій деталь охолоджують послідовно в двох середовищах: перше середовище - охолоджуюча рідина (вода), друге - повітря або масло.
Ступеневе гартування. Нагріту до температури гарту деталь охолоджують в розплавлених солях, після витримки в плині часу необхідного для вирівнювання температури по всьому перетину, деталь охолоджують на повітрі, що сприяє зниженню гартівних напруг.
Ізотермічне гартування так само, як і ступінчасте, проводиться у двох охолоджуючих середовищах. Температура гарячої середовища (соляні, селітрові або лужні ванни) різна: вона залежить від хімічного складу сталі, але завжди на (20-100) ° С вище точки мартенситного перетворення для даної сталі. Остаточне охолодження до кімнатної температури проводиться на повітрі.
Ізотермічне гартування широко застосовується для деталей з високолегованих сталей. Після ізотермічного загартування сталь набуває високі міцнісні властивості, тобто поєднання високої в'язкості з міцністю.
Гартування з самоотпуском має широке застосування в інструментальному виробництві. Процес полягає в тому, що деталі витримуються в охолоджуючої середовищі не до повного охолодження, а в певний момент витягуються з неї з метою збереження в серцевині деталі деякої кількості тепла, за рахунок якого здійснюється подальший відпустку.
5. Відпуск сталі
Відпуск сталі є завершальною операцією термічної обробки, формує структуру, а отже, і властивості сталі. Відпустка полягає в нагріванні сталі до різних температур (залежно від виду відпустки, але завжди нижче критичної точки), витримці при цій температурі і охолодженні з різними швидкостями. Призначення відпустки - зняти внутрішні напруження, що виникають у процесі загартування, і отримати необхідну структуру.
Залежно від температури нагріву загартованої деталі розрізняють три види відпустки: високий, середній і низький.
Висока відпустка проводиться при температурах нагрівання вище (350-600)° С, але нижче критичної точки; таку відпустку застосовується для конструкційних сталей.
Середня відпустка проводиться при температурах нагрівання (350 - 500)° С; таку відпустку широко застосовується для пружинного і ресорної сталей.
Низька відпустка проводиться при температурах (150-250)° С. Твердість деталі після гарту майже не змінюється; низький відпустку застосовується для вуглецевих і легованих інструментальних сталей, для яких необхідні висока твердість і зносостійкість.
Контроль відпустки здійснюється за кольорами мінливості, які з'являтимуться на поверхні деталі.
6. Старіння
Старіння - це процес зміни властивостей сплавів без помітної зміни мікроструктури. Відомі два види старіння: термічне і деформаційне.
Термічне старіння протікає в результаті зміни розчинності вуглецю в залізі в залежності від температури.
Якщо зміна твердості, пластичності і міцності протікає при кімнатній температурі, то таке старіння називається природним.
Якщо ж процес протікає при підвищеній температурі, то старіння називається штучним.
Деформаційне (Механічне) старіння протікає після холодної пластичної деформації.
7.Обробка холодом
Новий вид термічної обробки, для підвищення твердості стали шляхом перекладу залишкового аустеніту загартованої сталі в Мартенсом. Це виконується при охолодженні сталі до температури нижньої мартенситної точки.
Методи поверхневого зміцнення
Поверхневим загартуванням називають процес термічної обробки, представляє собою нагрів поверхневого шару сталі до температури вище критичною і наступне охолодження з метою отримання в поверхневому шарі структури мартенситу.
Розрізняють такі види: індукційне гартування; гартування в електроліті, гартування при нагріванні струмом високої частоти (ТВЧ), гартування з газополуменевим нагріванням.
Індукційне гартування засноване на фізичному явищі, сутність якого полягає в тому, що електричний струм високої частоти, проходячи по провіднику, створює навколо нього електромагнітне поле. На поверхні деталі, вміщеній в цьому полі, індукуються вихрові струми, викликаючи нагрівання металу до високих температур. Це забезпечує можливість протікання фазових перетворень.
Залежно від способу нагрівання індукційне гартування підрозділяється на три види:
одночасний нагрів і гартування всієї поверхні (використовується для дрібних деталей);
послідовний нагрів і гартування окремих ділянок (використовується для колінчастих валів і подібних їм деталей);
безперервно-послідовний нагрів і гартування переміщенням (використовується для довгих деталей).
Газополум'яне гартування. Процес газополум'яного гартування полягає у швидкому нагріванні поверхні деталі ацетилено-кисневим, газокисневі або киснево-гасових полум'ям до температури гартування з подальшим охолодженням водою або емульсією.
Загартування в електроліті. Процес загартування в електроліті полягає в наступному: у ванну з електролітом (5-10% розчин кальцинованої солі) опускають гартувати деталь і пропускають струм напругою 220-250 В. У результаті чого відбувається нагрівання деталі до високих температур.
8.Термічна обробка чавуну
Термічну обробку чавунів проводять з метою зняття внутрішніх напружень, що виникають при лиття і викликають з плином часу зміни розмірів і форми виливки, зниження твердості і поліпшення оброблюваності різанням, підвищення механічних властивостей. Чавун піддають відпалу, нормалізації, загартуванню та відпуску, а також деякими видами хіміко-термічної обробки (азотуванню, алітуванню, хромуванню).
Відпал для зняття внутрішніх напружень . Цьому відпалу піддають чавуни при наступних температурах: сірий чавун з пластинчастим графітом (500 - 570) °С; високоміцний чавун з кулястим графітом (550 - 650) ° С; низьколегований чавун (570 - 600) ° С; високолегований чавун (620 - 650) ° С. При цьому відпалі фазових перетворенні не відбувається, а знімаються внутрішньо напруги, підвищується в'язкість, виключається викривлення і утворення тріщин в процесі експлуатації.
Зм'якшуючий відпал (відпал графітізіруючий низькотемпературний ). Проводять для поліпшення оброблюваності різанням і підвищення пластичності. Його здійснюють тривалої витримкою при (680 - 700) ° С або повільним охолодженням виливків при (760 - 700) °С. Для деталей складної конфігурації охолодження повільне, а для деталей простої форми - прискорене.
Відпал графітізіруючий , в результаті якого з білого чавуну отримують ковкий чавун.
Нормалізацію застосовують для збільшення пов'язаного вуглецю, підвищення твердості, міцності і зносостійкості сірого, ковкого і високоміцного чавунів. При нормалізації чавун (виливки) нагрівають вище температур інтервалу перетворення (850 - 950) °С і після витримки охолоджують на повітрі.
Гартуванню піддають сірий, ковкий і високоміцний чавун для підвищення твердості, міцності і зносостійкості. За способом виконання гарт чавуну може бути об'ємною безперервної, ізотермічної та поверхневої.
При об'ємної безперервної загартуванню чавун нагрівають до температури (850 - 950) ° С. Потім витримують для прогріву і повного розчинення вуглецю. Охолодження здійснюють у воді або маслі. Після гарту проводять відпустку при температурі (200 - 600) ° С. В результаті підвищується твердість, міцність і зносостійкість чавуну.
При ізотермічному загартуванню чавун нагрівають так само, як і при об'ємної безперервно ї загартуванню, витримують від 10 до 90 хвилин і охолоджують у розплавленої солі при (200 - 400) °С, і після витримки охолоджують на повітрі.
Поверхневий гарт з нагріванням поверхневого шару киснево-ацетиленовим полум'ям, струмами високої частоти або в електроліті. Температура нагріву (900 - 1000) ° С. Охолодження у воді, маслі або олійною емульсії.
Старіння застосовують для стабілізації розмірів литих чавунних деталей, запобігання викривлення і зняття внутрішніх напруг. Зазвичай старінні проводять після грубої механічної обробки. Розрізняють два види старіння: природне і штучне.
Природне старіння здійснюється на відкритому повітрі або в приміщенні. Вироби після лиття витримуються протягом 6 - 15 місяців.
Штучне старіння здійснюється при підвищених температурах; тривалість - декілька годин. При штучному старінні виливки чавуну завантажують у піч, нагріту до (100 - 200) °С, нагрівають до температури (550 - 570) ° С зі швидкістю (30 - 60) °С в годину, витримую 3 - 5 годин і охолоджують разом з піччю зі швидкістю (20 - 40) ° С в годину до температури (150 - 200) ° С, а потім охолоджують на повітрі.
Хіміко-термічна обробка чавуну
Для підвищення поверхневої твердості і зносостійкості сірі чавуни піддають азотуванню. Найчастіше азотіруют сірі перлітні чавуни, леговані хромом, молібденом, алюмінієм. Температура азотування (550 - 580) ° С, час витримки 30 - 70 годин. Крім азотування, підвищення поверхневої твердості і зносостійкості легованого сірого перлітного чавуну можна досягти газовим і рідинним ціануванням при температурі 570° С. Для підвищення жаростійкості чавунні виливки можна піддавати алітуванню, а для отримання високої корозійної стійкості в кислотах - сіліцірованіе.
Термічна обробка сплавів кольорових металів
Алюмінієві сплави
Алюмінієві сплави піддаються трьом видам термічної обробки: відпалу, загартування і старінню. Основними видами відпалу є: дифузійний, рекрісталлізаціонний і термічно зміцнених сплавів.
Гомогенізацію застосовують для вирівнювання хімічної мікронеоднорідності зерен твердого розчину. Для виконання гомогенізації алюмінієві сплави нагрівають до (450 - 520) ° С і витримують при цих температурах від 4 до 40 годин; після витримки - охолодження разом з піччю або на повітря. У результаті цього структура стає більш однорідною і підвищується пластичність.
Рекрісталлізаціоний відпал для алюмінію і сплавів на його основі застосовують набагато ширше, ніж для сталі. Це пояснюється тим, що такі метали, як алюміній і мідь, а так само багато сплавів на їх основі, не упрочнюються загартуванням і підвищення механічних властивостей може бути досягнуто тільки холодною обробкою тиском, а проміжної операцією при такій обробці є рекрісталлізаціоний відпал. Температура рекристаллизационого відпалу алюмінієвих сплавів (300 - 500) С витримка 0,5 - 2 години.
Відпал термічно зміцнених сплавів застосовують для повного зняття зміцнення, він проводиться при температурах (350 - 450) °С з витримкою 1 - 2 години і подальшим досить повільним охолодженням.
Після гартування міцність сплаву дещо підвищується, а пластичність не змінюється. Після гарту алюмінієві сплави піддають старінню , при якому відбувається розпад пересиченого твердого розчину.
Деформуємі алюмінієві сплави
У загартованому стані дуралюміни пластичні і легко деформуються. Після гартування і природного або штучного старіння міцність дуралюмина різко підвищується.
Ливарні алюмінієві сплави
Для ливарних алюмінієвих сплавів використовують різні види термічної обробки залежно від хімічного складу. Для зміцнення ливарні алюмінієві сплави піддають гартуванню з отриманням пересичені твердого розчину і штучному старінню, а також тільки загартуванню без старіння з отриманням в загартованому стані стійкої твердого розчину.
Магнієві сплави
Магнієві сплави, так само як і алюмінієві, піддають відпалу, загартування і старіння. Для вирівнювання хімічної мікронеоднорідност і зерен твердого розчину шляхом дифузії зливки магнієвих сплавів піддають гомогенізації при температурах (350 - 400) °С з витримкою 18 - 24 години. Напівфабрикати деформівних магнієвих сплавів піддають рекрісталлізаціонний відпал при температурі 350° С, а також при низьких температурах (150 - 250) ° С відпалу для зняття залишкових напруг.
Магнієві сплави піддають загартуванню , або загартуванню і штучного старінню . При температурі 20°С у загартованих магнієвих сплавах ніяких змін не відбувається, тобто вони не схильні до природного старіння.
Мідь і мідні сплави
Термічна обробка міді. Деформування міді супроводжується підвищенням її міцності і пониженням пластичності. Для підвищення пластичності мідь піддають рекрісталлізаціоному відпалу при (500 - 600) ° С, в результаті якого пластичність різко підвищується, а міцність знижується.
Термічна обробка латуней . Вони піддаються тільки рекрісталлізаціоному відпалу при (600 - 700) ° С (для зняття наклепу). Охолоджують латунь при відпалі на повітрі або для прискорення охолодження і кращого відділення загартовують у воді. Для латунних деталей, що мають після деформації залишкові напруги, в умовах вологої атмосфери характерне явище мимовільного розтріскування. Щоб цього уникнути латунні деталі піддають низькотемпературного відпалу при (200 - 300) °С, в результаті чого залишкові напруги знімаються, а наклеп залишається. Низькотемпературного відпалу особливо необхідно піддавати алюмінієві латуні, які схильні до мимовільного розтріскування.
Термічна обробка бронз . Для вирівнювання хімічного складу бронзи піддають гомогенізації при (700 - 750) °С з наступним швидким охолодженням. Для зняття внутрішніх напружень виливки віджигають при 550° С. Для відновлення пластичності між операціями холодної обробки тиском піддають рекрісталлізаціоний відпал при (600 - 700) ° С.
Алюмінієві бронзи з вмістом алюмінію від 8 до 11%, які відчувають при нагріві і охолодженні фазову перекристалізації, можуть піддаватися загартуванню. У результаті загартування підвищується міцність і твердість, але знижується пластичність. Після гарту слід відпустку при (400 - 650) °С залежно про необхідних властивостей. Також піддають гомогенізації, а деформуються напівфабрикати - рекрісталлізаціоний відпал при (650 - 800) °С.
Титанові сплави
Титанові сплави піддають рекрісталлізаціоний відпал і відпал з фазовою перекристаллізацією, а також зміцненню термічною обробкою - загартуванням і старінням. Для підвищення зносостійкості і задіростойкості титанові сплави піддають азотуванню, цементації або окислення.
Рекрісталлізаціоний відпал застосовують для титану і сплавів для зняття наклепу після холодної обробки тиском. Температура рекристаллизационого відпалу (520 - 850) ° С залежно від хімічного складу сплаву і виду напівфабрикату.
Відпал з фазової перекристалізації застосовують з метою зниження твердості, підвищення пластичності, подрібнення зерна, усунення структурної неоднорідності. Застосовують простий, ізотермічний і подвійний відпал; температура нагрівання при відпалі (750 - 950) ° С залежно від сплаву.
При ізотермічному відпалі після витримки при температурі відпалу деталі охолоджують до (500 - 650) ° С (Залежно від сплаву) в тій же печі йди переносять в іншу піч і витримують певний час, і охолоджують на повітрі. При ізотермічному відпалі скорочується тривалість відпалу, а пластичність виходить більш високою.
При подвійному відпалі деталі нагрівають до температури відпалу, витримують і охолоджують на повітрі. Потім повторно нагріваю до (500 - 650) °С, витримують і охолоджують на повітрі. Подвійний відпал порівняно з ізотермічним підвищує межу міцності при незначному зниженні пластичності і скорочує тривалість обробки.
З усіх видів хіміко-термічної обробки титанових сплавів найбільше поширення отримало азотування, виконуються в середовищі азоту або в суміші азоту та аргону при температурах (850 - 950) °С протягом 10 - 50 годин. Деталі з титанових сплавів після азотування володіють хорошими антифрикційними властивостями.
У машинах використовують не тільки підшипники кочення, але і ковзання. Оскільки вкладиші підшипників ковзання безпосередньо стикаються з валами, вони повинні бути досить пластичними і досить твердими, мати малий коефіцієнт тертя, бути мікропористими і мати невисоку температуру плавлення. Сплави, що відповідають переліченим вимогам, називають антифрикційними.
Антифрикційні сплави мають пластичну основу, в якій рівномірно розташовані більш тверді частинки.
Антифрикційні матеріали поділяють на такі групи:
- білі антифрикційні сплави на основі олова, свинцю і алюмінію;
- сплави на основі міді;
- чавуни сірі, модифіковані та ковкі;
- металокерамічні пористі матеріали;
- пластмаси.
1.6.1. Бабіти.
1.6.2. Алюмінієві антифрикційні сплави.
1.6.3. Антифрикційні матеріали на основі міді.
У промисловості використовують олов’янисті та свинцеві бабіти.
В олов’янистому бабіті пластичною основою є твердий розчин - сурми і міді в олові, а твердими частинами - сполуки - SnSb і Cu3Sn. Бабіти маркуються, наприклад, Б83 (буква Б свідчить, що це бабіт, число 83 вміст олова в %).
У свинцевих бабітах з сурмою, наприклад, Б16, тверді частинки утворюють кристали сполук SnSb іCи3Sn, розташовані в м'якій основі - розчині сурми і олова у свинці.
Бабіти використовують для виготовлення вкладишів тракторних і автомобільних двигунів.
Сплави алюмінію порівняно з бабітами мають меншу щільність, більшу міцність і дешевші. Недоліком є значна різниця в коефіцієнті розширення алюмінієвих сплавів і сталі. Найбільш поширений алюмінієво-мідний сплав алькусин (7,5-9,5 % Сu, 1,5-2,5 % Sі, решта – алюміній), в якому м'яка основа - твердий розчин кремнію і міді в алюмінії, а тверді частини - сполуки СuАl2. Цей сплав використовують як замінник бабіту марки Б16.
Олов'яні бронзи з 8 % Sn і більше застосовують як підшипникові. За структурою вони є основною масою твердого розчину олова в міді (м'яка фаза) і тверді частинки сполуки Сu3Sn.
Олов'яниста бронза марки БрОФ 10-1, що містить 0,8 - 1,2 % фосфору, до 10 % Sn - прекрасний антифрикційний матеріал.
Як антифрикційний матеріал використовують також олов'янисто-свинцеві бронзи (БрОС 8-12 і т.п.).
В автотракторній промисловості поширені пористі самозмащувальні підшипники з порошкових сплавів.
Вимоги до антифрикційних матеріалів
Антифрикційні матеріали призначені для виготовлення підшипників (опір) ковзання, що широко застосовуються в сучасних машинах і приладах завдяки стійкості до вібрацій, безшумності роботи, невеликим габаритам. Основними властивостями антифрикційних матеріалів варто вважати антифрикційність і опір втомленості.
Антифрикційність – це здатність матеріалу забезпечувати низький коефіцієнт ковзання, незначні втрати на тертя і малу швидкість зношування сполучених деталей. Крім того, кожен матеріал у конкретних умовах роботи має бути, наприклад, стійким проти окиснювання за підвищених температур, мати високий опір корозії під час роботи в агресивних середовищах і т. ін. Ці матеріали мають працювати в широкому діапазоні швидкостей ковзання (від 0,001 до 100 м/с і більше), навантажень (від 1 м до 25 МПа і більше), температур до 100°С і більше. Наведені відомості не дають змоги створити універсальний антифрикційний матеріал, здатний працювати у вузлах тертя різного призначення. Тож постає потреба в розробленні різноманітних матеріалів тертя для конкретних заданих умов роботи. На тепер налічується безліч вузлів тертя, у яких застосовуються антифрикційні матеріали – циліндричні й кулькові підшипники, підп’ятники, вкладиші, напрямні, що ковзають, струмознімачі, торцеві й бічні ущільнення, шарнірні пристрої, поршневі кільця та ін. Антифрикційні матеріали працюють у найрізноманітніших умовах, а саме: за граничного тертя, у вакуумі, тертя без змащення, еластогідродинамічного тертя, за підвищених температур, високих швидкостей, великих навантажень, у різних агресивних середовищах (воді, кислотах, лугах, розплавлених металах, розпечених газах), інертних газах та ін.
Основні вимоги до антифрикційних матеріалів такі:
• висока зносостійкість;
• низькі значення коефіцієнта тертя;
• оптимальна поверхнева й об’ємна міцність;
• припрацьовуваність;
• достатня в’язкість для унеможливлення крихкого руйнування;
• висока втомна міцність;
• здатність протистояти схоплюванню;
• достатня теплопровідність й оптимальні значення коефіцієнта теплового розширення;
• наявність у матеріалі запасу твердого або рідкого мастила;
• технологічність виготовлення;
• економічність. Крім цих вимог до матеріалів конкретного призначення, що працюють у специфічних умовах, потрібні спеціальні властивості. Наприклад, об’ємна міцність у матеріалах для важконавантажувальних вузлів тертя має бути досить високою, а матеріали для роботи в разі підвищених температур повинні мати стійкість проти окиснення.
2. В яких середовищах протікає хімічна корозія?
3. Чи можлива хімічна корозія в нафтопродуктах? Відповідь обґрунтуйте.
4. Опишіть процеси за якими відбувається хімічна корозія.
5. Як оцінюється об’ємний показник швидкості корозії?
6. Як визначають масовий показник швидкості корозії?
7. Як розраховують глибинний показник швидкості корозії?
8. Як розраховують механічний показник корозії?
9. Як визначити омічний показник корозії?
10. Які висновки можна зробити за показниками хімічної корозії?
Перевага використання грунтовки по іржі«Новбытхим»
Целюлозні автоемалі
Акрилова автоемаль
Який вибрати лак для фарбування автомобіля?
Перламутровий лак
Порошкова фарби для фарбування автомобіля
Порошкова фарба
Який автоэмалью фарбувати по іржі?
Фарби по іржі
Фарби на водній основі
1 Особливості сучасних антикорозійних складів
3 Тонкощі захисту від іржі елементів авто
4 Невеликий огляд популярних фарб по металу
Класифікація лакофарб по металу
Вибір Антикорозійних фарб
Як зафарбувати іржу на машині самостійно: фарба і методи
Де виникає проблема
Фарба по іржі Спецназ: універсальна грунтовка-емаль, відгуки
Вибір фарби
Думка споживачів
Склад фарби і її модифікації
У власників досить підтриманих автомобілів рано чи пізно виникає бажання навести, хоча б частково, кузов свого авто в порядок. Якщо брати до уваги шпаклівку і інші кузовні роботи, що вимагають втручання професіонала з автосервісу, то потрібно бути готовим викласти чималу суму. Оплата за виконану роботу буде високою, адже ремонт автомобільних кузовів завжди був дорогим.
Для ізоляції електричних машин і апаратів широко застосовують різні волокнисті матеріали рослинного походження (папір, картон, бавовняні і шовкові волокна, тканини і стрічки), а також деякі синтетичні текстильні матеріали, одержувані хімічною переробкою окремих речовин: штучний шовк, синтетичні волокна (капрон, нейлон), матеріали з полістиролу, поліхлорвінілу, поліамідні і триацетатні плівки. Органічні волокнисті ізоляційні матеріали відрізняються невисокою нагревостойкостью. і в природному вигляді без спеціальної обробки відносяться до класу Y. Їх недолік - висока гігроскопічність. Між їх волокнами і нитками залишаються повітряні проміжки (пори), легко поглинають вологу.
Папір і картон - листові матеріали коротко-волокнистої будови, що складаються з целюлози. Папір виготовляють з подрібненого бавовняного ганчір'я і волокон деревини, які піддають спеціальній хімічній обробці. Всі сорти паперу мають гарні ізоляційні властивості, однак в електромашинобудуванні застосовують тільки такі спеціальні сорти: кабельну (товщиною 0,08-0,17 мм), телефонний (0,05 мм), конденсаторну (7-30 мк), обклеювальну (0, 33 мм), просочувальну (0,12 мм), намотувальні (0,05-0,07 мм) і мікастрічкових (20 мк).
Зазначені сорти паперу використовують для ізоляції обмотувальних проводів і кабелів різного типу, виготовлення конденсаторів, обклеювання листів електротехнічної сталі, а також для виготовлення Мікаленти (див. Нижче) і різних шаруватих пластичних матеріалів (листового і фасонного гетинакса, бакелітових трубок та ін.).
Картон виготовляють з того ж сировини, що і папір, але він має значно більшу товщину. У електромашинобудуванні застосовують такі сорти картону: електрокартон, фібру і літероід.
Пластичні маси -це матеріали, здатні в прес-формах під дією зовнішнього тиску приймати необхідний вид. Велика частина ізоляційних пластмас (наприклад, з органічними сполучними) вимагають також підвищеної температури. До переваг їх, в першу чергу, відноситься висока економічність.
Пластмаси, використовувані в електротехніці, - це найчастіше ізоляційні матеріали, що складаються з двох основних складових: пов'язує і наповнювача. До перших відносяться смоли, бітуми, цемент і ін. До других - порошкоподібні матеріали (деревна або кам'яне борошно), волокнисті (бавовняну, азбестове або скляне волокно і ін.), А також листові вироби (папір, текстиль і т. П.) .
Наповнювач в основному покращує механічні характеристики ізоляції, але знижує електричні, до того ж підвищує гігроскопічність. Ось чому для пластмас, від яких потрібні високі електроізоляційні властивості, нерідко від наповнювачів відмовляються, хоча вони значно їх здешевлюють. В пластмаси вводяться ще пластифікатори (для підвищення гнучкості) і барвники (для отримання потрібного зовнішнього вигляду).
Електричні і механічні характеристики, а також нагреостойкость пластмас залежать від сполучного і від наповнювача. EПР в середньому становить 3,0-40 МВ / м (при 20 ° С), нагревостойкость коливається від А до Н.
Промисловістю пластмасові вироби випускаються у вигляді заготовок і готових фасонних деталей часто складної конфігурації.
Область застосування пластмас дуже велика: від корпусів побутових електроприладів до ізоляційних деталей складної конфігурації для електричних машин і апаратів.
Слюда є основою великої групи електроізоляційних виробів. Головне достоїнство слюди - висока термостійкість поряд з досить високими електроізоляційними характеристиками. Слюда є природним мінералом складного складу. В електротехніці використовують два види слюди: мусковіт КАl2 (АlSi3О10) (ОН) 2 і флогопит КMg3 (АlSi3О10 (ОН) 2. Високі електроізоляційні характеристики слюди зобов'язані її незвичайного будовою, а саме - шаруватості. Слюдяні пластинки можна розщеплювати на плоскі пластинки аж до субмікронних розмірів. Руйнують напруги при відриві одного шару від іншого шару складають приблизно 0.1 МПа, тоді як при розтягуванні вздовж шару - 200-300 МПа. З інших властивостей слюди відзначимо невисокий tgd, менш ніж 10-2; високий питомий опір, більш 1012 Ом · м; досить високу електричну міцність, більш 100 кВ / мм; термостійкість, температура плавлення понад 1200 ° С.
Слюда використовується в якості електричної ізоляції, як у вигляді щипана тонких пластинок, в. т. ч. склеєних між собою (міканіти), так і у вигляді слюдяних паперів, в. т. ч. просочених різними сполучними (слюдиніту або слюдопласт). Слюдяная папір виробляється за технологією, близькою до технології звичайного паперу. Слюду роздрібнюють, готують пульпу, на машинах з виробництва паперу розгортають аркуші паперу.
Електроізоляційна кераміка являє собою матеріал, що отримується з формувальної маси заданого хімічного складу з мінералів і оксидів металів. Будь-яка кераміка, в тому числі і електроізоляційна, - матеріал багатофазних, що складається з кристалічної, аморфної і газової фаз. Її властивості залежать від хімічного і фазового складів, макро- і мікроструктури і від технологічних прийомів виготовлення./1/ В електричної та радіоелектронної промисловості керамічна технологія широко застосовується для виготовлення діелектричних, напівпровідникових, п'єзоелектричних, магнітних, металокерамічних і інших виробів. В даний час, особливо з проникненням в побут електронної техніки, з електроізоляційної кераміки виготовляються десятки тисяч найменувань виробів масою від десятих часток грама до сотень кілограмів і розмірами від декількох міліметрів до декількох метрів. У ряді випадків вироби з кераміки, головним чином з електрофарфору, покриваються глазур'ю, що зменшує можливість забруднення, покращує електричні і механічні властивості, а також зовнішній вигляд виробу./14/ Електрофарфор є основним керамічним матеріалом, використовуваним у виробництві широкого асортименту низьковольтних і високовольтних ізоляторів та інших ізоляційних елементів з робочою напругою до 1150 кВ змінного і до 1500 кВ постійного струму.
У відкритих прес-формах залишок прес-матеріалу витискується, а в закритих — товщина виробу 2 залежить від кількості матеріалу, завантаженого в порожнину прес-форми.
Прес-порошок з бункера 1 (рис., б) надходить у циліндр 2> який охолоджується водою 6, що не дає полімеру змоги прилипнути до стінок шнека З та циліндра. Шнек переміщує прес-порошок у вихідну зону 5 циліндра, яка має електрообігрів. Нагрітий полімер продавлюється крізь вихідні отвори і потрапляє до мундштука 4 з отвором потрібного профілю і розміру.
Чавун, його особливості, механічні, технологічні властивості, галузь застосування
Чавун — це сплав заліза з вуглецем (з вмістом від 2,14 до 6,67 % С).
У машинобудуванні застосовують чавуни, які містять від 2,14 до 4,5 % вуглецю.
Чавун порівняно з вуглецевою сталлю характеризується кращими ливарними і гіршими пластичними властивостями.
Механічні властивості чавуну залежать від двох чинників: кількості, розміру, форми і розподілу графітових вкраплень; структури металевої основи.
Перший чинник має вирішальне значення, оскільки графітові вкраплення, розміщуючись у чавуні і утворюючи ніби надрізи в металевій основі, ослаблюють Його міцність (особливо при великих вкрапленнях). При дрібних графітових вкрапленнях чавун має високі механічні властивості.
Характер і ступінь графітизації зумовлюється швидкістю тверднення і охолодження чавуну. Чим повільніше відбувається процес тверднення й охолодження, тим краще розкладається карбід заліза, тим більше виділяється графіту.
Другим чинником впливу на міцність чавуну є структура його металевої основи.
Нормальна структура сірого чавуну (без добавляння легувальних елементів і без термообробки) є феритною чи перлітною, а проміжна між ними — феритно-перлітною металевою основою.
Найбільш бажана металева основа чавуну — перліт із вмістом 0,8 % зв'язуючого вуглецю Fe3C. Чавуни з феритною і феритно-перлітною основою мають знижену міцність, порівнюючи з перлітним чавуном, але вони характеризуються підвищеною в'язкістю, оскільки в них менше або зовсім немає зв'язуючого вуглецю.
Щоб підвищити механічні властивості чавуну, перед розливанням у форми в рідкий чавун додають модифікатор у вигляді розмеленого силікокальцію чи феросиліцію в кількості 0,1...0,4 % від маси чавуну. Модифікатори розкиснюють чавун, утворюють силікатні вкраплення, які є центрами графітизації і гальмують ріст зерен графіту. Це дає змогу одержувати високоміцний чавун з кулястим графітом.
Вплив домішок на структуру і властивості чавуну
Види чавунів, їх маркування і застосування
Ковкий чавун — умовна назва, оскільки його не кують. Цей чавун одержують з білого чавуну термічною обробкою (спеціальним відпалюванням — томлінням).
Жаростійкі чавуни.
Вуглець визначає структуру і властивості чавуну. В чавуні він може бути в структурі цементиту або графіту. Графіт у чавуні має пластинчасту, кулясту і пластівцеву форму.
Виділення вуглецю у вигляді графіту надає чавуну кращих ливарних властивостей.
Манган збільшує крихкість чавуну, поліпшує рідкотекучість. Він сприяє відбілюванню чавуну, тобто утворенню хімічної сполуки Fe3C (цементиту). У чавунах міститься 0,5... 1,0 % мангану.
Силіцій сприяє графітизації чавуну, тобто утворенню сірого чавуну. Він утворює із залізом хімічні сполуки (FeSi, Fe3Si2, які називають силіцидами. Силіциди переходять у твердий розчин із залізом, знижують розчинність вуглецю в залізі, сприяють розпаду цементиту з виділенням графіту.
Графітизувальні дії силіцію практично обмежуються 3,5 % його вмісту в чавуні. Змінюючи вміст силіцію в чавуні, можна регулювати в ньому співвідношення між зв'язуючим вуглецем і графітом. Чим більше силіцію, тим більше виділення графіту, а отже, тим менша міцність такого чавуну, нижча твердість — краще обробляється.
Силіцій сприяє деякому зниженню температури плавлення, покращує рідкотекучість.
Сірка є шкідливою домішкою. Вона сприяє відбілюванню чавуну; значно знижує його рідкотекучість та зумовлює крихкість і схильність до утворювання тріщин. Тому вміст сірки обмежується 0,08...0,12 %. Наявність сірки в чавуні затримує розпад цементиту, збільшує усадку, зумовлюючи таким чином утворення структури білого чавуну. При цьому в чавуні з'являються тверді плями, що погіршує його обробку різанням і механічні властивості.
Фосфор у невеликій кількості є корисною домішкою. Він майже не впливає на структуру чавуну, оскільки не прискорює і не сповільнює графітоутворення. Від наявності фосфору в твердому розчині твердість чавуну підвищується, а в'язкість значно знижується, що спричинює погіршення механічних властивостей чавуну. Фосфор поліпшує ливарні властивості: знижує температуру плавлення, збільшує рідкотекучість і сприяє якісному заповненню форми. Тому для лиття тонкостінних виробів беруть чавун із підвищеним вмістом фосфору (1,0... 1,25 %), а для звичайного лиття — 0,1...0,9 % Р.
Залежно від хімічного складу і структури чавуни бувають: білі, сірі, ковкі, високоміцні і спеціальні.
Білий чавун має обмежене застосування через високу твердість і крихкість. У білому чавуні майже весь вуглець перебуває у хімічно зв'язаному стані — у вигляді цементиту Fe3C. Білий чавун дуже твердий, він майже не піддається обробці різанням і в машинобудуванні сільськогосподарської техніки не застосовується, його використовують для виробництва сталі, ковкого чавуну, тому називають Переробним.
Сірий чавун широко застосовують у машинобудуванні завдяки його високим ливарним, антифрикційним властивостям, задовільній обробці різанням, зносостійкості. Проте для нього характерні невисоке значення границі міцності при розтягуванні, дуже низька пластичність.
Границя його міцності при розтягуванні σΒ= 120...380 МПа, твердість 145...270 НВ, відносне видовження δ = 0,2...0,8 %.
Механічні властивості чавунів характеризуються їх структурою й умовами (у визначенні не тільки хімічного складу). Стандарти регламентують не хімічний склад чавунів, а їхні властивості, які й позначають у марках чавунів. Наприклад, марка СЧ 20 позначає сірий чавун з границею міцності при розтягуванні σв = 200 МПа. В машинобудуванні застосовують марки сірих чавунів СЧ 10...СЧ 45 (остання цифри «0» або «5»).

Сірі чавуни містять постійні домішки в такій кількості: 3,0...3,5 % вуглецю, 1,5...3,0 % силіцію, майже 0,8 % мангану, до 0,12 % сірки і 0,3...0,9% фосфору.
У сірих чавунах вуглець частково або повністю перебуває у вільному стані у формі пластинчастого графіту. За цього в зломі має сірий колір. Інколи в структурі чавуну крім графіту утримується ледебурит. Такий сіро-білий чавун називають Половинчастим. Основні його властивості: висока твердість, крихкість і низька міцність.
Отже, змінюючи вміст і співвідношення постійних домішок, можна в певних межах змінювати структуру чавуну і його властивості.
Залежно від розпаду цементиту одержують основи сірих чавунів, які складаються: з фериту, їх називають Феритними Чавунами; з фериту і перліту — Феритно-перлітними; З перліту — Перлітними. Найміцнішими вважають перлітні чавуни.

Рис. 2.25. Мікроструктура сірих чавунів: α — феритний; 6 — феритно-перлітнни; В — перлітний
Сірий чавун широко застосовують в автотракторному і сільськогосподарському машинобудуванні для виробництва деталей методом лиття. З нього виготовляють станини металорізальних верстатів, блоки і гільзи автомобільних і тракторних двигунів.
Щоб вибрати марку чавуну для конкретної деталі, потрібно обумовити, в яких умовах працює ця деталь і порівняти технологічні та механічні властивості вибраної марки для забезпечення технічних умов роботи деталі в механізмі.
У довідниках, каталогах та іншій літературі наводять перелік чавунів (інших марок сплавів) для конкретних деталей. Наприклад, феритний сірий чавун марки СЧ 10 призначений для виготовлення слабко - і середньонавантажених деталей: кришок, фланців, маховиків, дисків зчеплення та ін. Феритно-перлітний чавун марки СЧ 20 застосовують для деталей, які працюють при підвищених статичних, динамічних навантаженнях: блоки, поршні та головки циліндрів. Перлітні сірі (модифіковані) чавуни СЧ ЗО, СЧ 40 мають високі механічні властивості. їх використовують для виготовлення гільз циліндрів, розподільних валів та ін.
Ковкий чавун має графітні вкраплення пластівчастої форми (рис.). Він міцніший і пластичніший від звичайного сірого чавуну, має вищу в'язкість.

Щоб отримати ковкий чавун використовують білі чавуни (приблизно) такого складу: 2,5...3,2% вуглецю, 0,6...0,9 силіцію, 0,3...0,4 мангану, 0,1...0,2 фосфору і не більш як 0,06...ОДО % Сірки.
До структури білого чавуну входять перліт, ледебурит і цементит. Під час томління цементит, що є в чавуні, розпадається на ферит і графіт або на перліт і графіт: у першому випадку чавун буде феритним, а в другому — перлітним. Залежно від ступеня графітизації ковкий чавун може бути і феритно-перлітним. Різного ступеня графітизації досягають зміною умов відпалювання. Відмінність структур чавунів зумовлює і відмінність їхніх властивостей. Наприклад, феритний ковкий чавун порівняно з перлітним має меншу твердість і більшу пластичність.
Для одержання ковкого чавуну білий чавун нагрівають до 950... 1000 °С і після тривалого витримування охолоджують з малою швидкістю до кімнатної температури.
Щоб отримати ковкий феритний чавун, застосовують двостадійне відпалювання: першу стадію графітизації проводять за температури близько 1000 °С, тривалістю 30...40 год, другу стадію — при 740 °С, тривалістю 20...ЗО год.
Ковкий чавун має такий склад: 2,2...3,0% вуглецю; 0,7...L5 % силіцію; 0,2...0,6 % мангану; до 0,2 % фосфору і до 0,1 % сірки. Його виплавляють в електропечах. Злом чавуну, структурою якого є ферит і графіт, буде темним.

Рис. Мікроструктура ковких чавунів: а — феритний; б — феритно-перлітний; в — перлітний
Ковкий чавун маркують літерами КЧ і цифрами, дві перші з яких позначають границю міцності при розтягуванні, а останні — відносне видовження. Наприклад, марка КЧ 30-6 означає: КЧ — ковкий чавун; 30 — границя міцності при розтягуванні (σв = 300 МП а) і 6 — відносне видовження (δ = 6 %).
Ковкий чавун широко використовують в сільськогосподарському машинобудуванні для виготовлення деталей, які в процесі роботи витримують ударні навантаження (зубчасті колеса, шестерні, ланки ланцюгів, зірочки, пальці різального апарата зернозбирального комбайна та ін.), деталей сівалок, зерноочисних машин, механізації тваринництва (корпуси водопровідних вентилів, кранів та ін.)
Високоміцний чавун. Міцність чавуну залежить від кількості і форми вкраплення графіту. Додавання в рідкий сірий чавун 0,5 %
Магнію від маси чавуну сприяє утворенню дрібнозернистої структури. При цьому утворюються часточки графіту кулястої форми (рис. ), яка унеможливлює наявність гострих надрізів усередині металевої основи. Тому міцність, пластичність і в'язкість чавуну значно підвищуються.
Високоміцний чавун (як і сірий) поділяють на марки залежно від механічних властивостей, причому основним показником є границя міцності при розтягуванні. Механічні властивості залежать від структури металевої основи, яка може бути перлітною, феритно-перлітною і феритною. Ліпшою є структура, яка складається з перліту і графіту кулястої форми, обмежених невеликими (білими) кільцями фериту.
Маркується високоміцний чавун літерами ВЧ (високоміцний чавун) і цифрами, дві перші з яких показують границю міцності при розтягуванні, а останні — відносне видовження. Наприклад, марка ВЧ 800-2 означає, що чавун цієї марки має σ„ = 800 МПа, δ«2%.
Високоміцні чавуни є замінником литої і штампованої сталі. Тому з такого чавуну виготовляють відповідальні ші деталі машин і двигунів — гільзи циліндрів, колінчасті вали, деталі супортів металорізальних верстатів, лапки бурякозбирального комбайна та ін.

Рис. Мікроструктура високоміцних чавунів: α — феритний; б — феритно-перлітний; в — перлітний
Чавун з вермикулярним графітом призначений для одержання виливків. Він має структуру графіту вермикулярної (червоподібної) форми з вкрапленням до 40 % Кулястого та 10 % пластинчастого графіту.
Для виготовлення виливків призначені такі марки чавуну: ЧВГ 300-4, ЧВГ 300-5, ЧВГ 400-4, ЧВГ 500-1.
Умовне позначення марки чавуну з вермикулярним графітом, наприклад ЧВГ 300-4, означає: Ч — чавун; ВГ — вермикулярний
Графіт; 300 — границя міцності при розтягуванні, виражена в мегапаскалях (300 МПа); 4 — відносне видовження, виражене у відсотках (4 %).
Леговані чавуни зі спеціальними властивостями. До цих чавунів належать: антифрикційні, які забезпечують низький коефіцієнт тертя; жаростійкі, що мають підвищену стійкість до окиснення і корозії.
Щоб одержати чавуни зі спеціальними властивостями, їх легують нікелем, хромом, молібденом, титаном, алюмінієм і міддю. Відповідно змінюються структура і властивості чавунів.
Антифрикційні чавуни характеризуються пер літною структурою металевої основи, наявністю великої кількості вкраплень графіту. При цьому перлітна основа утворює достатню міцність деталі, фосфідна евтектика забезпечує підвищення зносостійкості, а вбирання і утримування мастила відбувається у місцях розміщення графіту.
Більшість антифрикційних чавунів містять у невеликій кількості хром, титан, мідь та інші елементи.
Антифрикційні чавуни маркують так: АЧС-1, АЧС-2, АЧС-4, АЧС-5, АЧС-6, АЧК-1, АЧК-2, АЧВ-1, АЧВ-2, що означає: АЧС — антифрикційний чавун сірий; АЧК — антифрикційний чавун ковкий; АЧВ — антифрикційний чавун високоміцний; число в кінці марки означає порядковий номер. Порядковий номер вказує на хімічний склад антифрикційного чавуну: АЧС-1 (3,2...3,6 % С; 1,3...2 % Si; 0,6...1,2% Μn; 0,2...0,5% Cr; 0,8... 1,6 % Си; 0,15...0,4 % Ρ; 0,12% S); АЧС-2 (3,0..3,8% С; 1,4..2,2 Si; 0,3... 1,0 Μn; 0,2...0,5% Cr; 0,2...0,5% Νί; 0,03...0,1% Ті; 0,2.0,5% Си; 0,151...0,40% Ρ; 0 12 % S); АЧК-2 (2 6 30% С; 08 13% Si; 0 2 06% Μn; до 0,25 % Ρ; 0,12% S); АЧВ-1 (2,8...3,5% С; 1,8...2,7% Si; 0,6...1,2% Μn; 0,7 % Си; 0,03...0,08 % Mg; 0,20 % Ρ; 0,03 % S).
Із антифрикційних чавунів виготовляють деталі тертя (втулки, вкладиші, підшипники ковзання, ролики, ущільнення та ін.).
Леговані чавуни з відповідним вмістом алюмінію, силіцію, хрому, нікелю мають підвищену жаростійкість. Крім того, вони забезпечують стабільність структури при нагріванні.
Жаростійкі чавуни маркують так: ЖЧХ-2,5 — жаростійкий хромовий чавун з вмістом 2,5 % Сг; ЖЧЮХ — жаростійкий алюмінієво-хромовий чавун з вмістом 1 % А1 і 1 % Сг; ЖЧЮ6С5 — жаростійкий алюмінієво-силіцієвий чавун з вмістом 6 % А1 і 5 % С.
Такі чавуни застосовують для виготовлення деталей прес-форм, елементів плунжерних пар машин для лиття під тиском, штампів гарячого деформування та ін.
Застосування чавуна для виготовлення деталей автомобілів.
Чавуни доцільно класифікувати за призначенням на: білі, сірі, ковкі, високоміцні і антифрикційні.
Білі чавуни - це чавуни, в яких вуглець перебуває у зв'язаному стані, у вигляді цементиту (Fe3C). Їх можна класифікувати за структурою: до евтектичні (вміст вуглецю від 2,14 до 4,3 %); евтектичні (вміст вуглецю 4,3 %); заевтектичні (вміст вуглецю від 4,3 до 6,67 %).Тому в машинобудуванні білі чавуни мають обмежене застосування. Їх використовують тільки як зносотривкий матеріал для відливання деталей шламових насосів, гідроциклонів, доменних печей, кульових млинів для розмелювання руд. З виливків білого чавуну отримують ковкі чавуни.
Білі чавуни в основному використовують для переробки у сталь. В окремих випадках для виготовлення виробів, які не піддаються високим навантаженням.
Сірі чавуни - це чавуни, в яких вуглець перебуває як у зв'язаному стані (Fe3C) так і в вільному у вигляді графіту. Сірі чавуни маркуються буквами СЧ з цифрою, яка вказує мінімальну границю міцності на розрив або розтяг.
Згідно ДСТУ є такі марки сірого чавуну: СЧ12, СЧ15, СЧ18, СЧ21, СЧ24, СЧ25, СЧ32, СЧ35, СЧ40, СЧ45. Сірі чавуни використовуються для виготовлення різних відливок для сільськогосподарських машин і побутової техніки. У структуру сірих чавунів обов'язково входить фаза графіт у вигляді пластинок. Це дозволяє в деякій мірі підвищити пластичність у порівнянні з білими чавунами.
Ковкий чавун - умовна назва м'якого і в'язкого чавуну, який одержують з білого чавуну шляхом відливанням з подальшою термічною обробкою. Його не кують, але він набагато пластичніший за сірий чавун. Ковкий чавун, як і сірий, складається із основи – сталі та містить частину вуглецю у вигляді графіту, проте графітові включення у ковкому чавуні інші по формі (у вигляді плям, а не пластин). Властивості ковкого чавуну залежать від металевої основи і розміру включень графіту, чим менші включення графіту, тим міцніший ковкий чавун.
Ковкий чавун позначають буквами КЧ і двома числами, з яких перше вказує мінімальну границю міцності на розтяг, друге - мінімальне відносне видовження (%). Відомі такі марки ковкого чавуну: на феритній основі (3-10 % перліту ) КЧ30-6, КЧ33-8, КЧ35-10, КЧ37-12, на перлітній основі (0-20 % фериту)КЧ45-7, КЧ50-5, КЧ55-4, КЧ60-3, КЧ65-3.
Ковкий чавун широко використовують у сільськогосподарському машинобудуванні, в автомобільній і тракторній промисловості, верстатобудуванні та в інших галузях промисловості. КЧ застосовують в автомобільній,
сільськогосподарській, текстильній та ін. галузях машинобудування. З нього
виготовляють деталі, які працюють при середніх і високих статичних і динамічних
навантаженнях (підшипники, кронштейни, картери редукторів, поршні, маточини).
Високоміцні чавуни. Підвищення міцності і пластичності чавунів досягають модифікуванням під час виплавляння, яке забезпечує одержання глобулярного (сфероїдального) графіту замість пластинчастого. Таку форму графіту одержують при введені присадок у рідкий чавун магнію або лігатури (20 % Mg + 80 % Nі).
Встановлені такі марки високоміцного чавуну у відливках: ВЧ35, ВЧ40, ВЧ50, ВЧ60, ВЧ70, ВЧ80, ВЧ100, ВЧ120. Число вказує мінімальну границю міцності на розрив або розтяг.
Міцність чавуну збільшується із збільшенням кількості перліту і дисперсності глобулів графіту.
Високоміцний чавун використовують замість сталі для відливання валів, зубчастих коліс, муфт, задніх мостів автомобілів, картерів та ін.
Деталі, виготовлені з високоміцного чавуна.
Розподільний і колінчасті вали карбюраторних двигунів, малофорсованих дизелів, кришки і стакани підшипників, корпуси коробок передач, валів відбору потужності, ι Лапки бурякозбиральних комбайнів та ін.
| ||
Корпуси редукторів, барабани, кронштейни, гальмові колодки, корпуси підшипників комбайнів та ін.
| ||
Блок-картера, головки циліндрів, кришки корінних підшипників, картери маховиків, корпусу розподільників коробок передач, задніх мостів, муфт зчеплення, деталі турбін, насосів, водо поли в них агрегатів та ін.
| ||
Маточини коліс автомобілів, кронштейни, корпуси диференціалів автомобілів, редукторів комбайнів і важелі, корпуси підшипників, ковпаки культиваторів та ін.
Деталі, виготовлені з антифрикційного
чавуну, можуть працювати у вузлах тертя без задирок, заїдань та значного
зношування, наприклад у підшипниках для валів (загартованих або
нормалізованих — АЧС-1, АЧС-4, АСЧ-5, АЧВ-1, АЧК-1 чи не
термооброблених — АЧС-6, АЧВ-2, АЧК-2), напрямних втулок для повзунів,
черв'ячних та інших зубчастих колесах.
|
Сталі. Вуглецеві сталі, їх склад, механічні й технологічні властивості, маркування, галузь застосування
Сталь - найважливіший матеріал машинобудування та інших галузей промисловості. Від чавуну вона
відрізняється меншим вмістом вуглецю та домішок сірки і фосфору (0,06-0,07 %). До складу вуглецевих
сталей у невеликих кількостях входять також марганець (до 0,8 %) і кремній (до 0,4 %). Леговані сталі для
поліпшення властивостей вміщують додатково введені елементи (Ni, Cr, Ті, V та ін.). Вихідними матеріалами
для виготовлення сталі є переробний чавун і сталевий брухт (скрап). Для одержання сталі з чавуну потрібно
видалити частину вуглецю і шкідливих домішок, перевести їх у шлак або гази. Основними способами
виробництва сталі є такі: киснево-конверторний, мартенівський і електричний.
Виробництво сталі в кисневих конверторах
Виробництво сталі в кисневих конверторах зводиться до продування рідкого чавуну киснем, що
подається до конверторів зверху через фурму. Раніше для продування
використовували повітря (бесемерівські й томасовські конвертори). Кисневоконверторний спосіб виробництва сталі прогресивніший і продуктивніший.
Конвертор, виготовлений зі сталевого листа, зсередини футерують
(обкладають) основною хромомагнезитовою цеглою. Сучасний конвертер
(об'ємом 100-350 т рідкого чавуну) встановлюють на станинах і оснащують
механізмом повороту. У нижній частині він має глухе дно, а у верхній -
відкриту горловину, через яку завантажують шихту. Робоче положення
конвертора - вертикальне, а під час завантаження і випуску сталі -
горизонтальне. Перед початком роботи конвертор завантажують брухтом (до 30
%) і заливають рідким чавуном (1250-І400°С), далі повертають конвертор у
вихідне вертикальне положення, вводять кисневу фурму і додають
шлакоутворюючі матеріали (флюси). Кисень подають під тиском 1-1,5 МПа
через водоохолоджувану фурму (2), розташовану на відстані 0,7-3 м від рівня
рідкого металу. Витрати кисню на виготовлення 1 т сталі становлять 50-60 м3
.
На початку процесу окислюються кремній, марганець і фосфор. Вони переходять у шлак, який зливають.
Далі додають вапно для видалення у шлак сірки. Процес відбувається з інтенсивним виділенням тепла і не
потребує палива. Температура підіймається до 2500°С. Вуглець вигорає. Наприкінці плавки сталь розкислюють: вводять елементи з високою здатністю до взаємодії з киснем (Si,
Mn, AI). Ці елементи взаємодіють з оксидом заліза FeO, утворюючи нерозчинні МnО, SiO2, Al2O3, які
переходять у шлак. Процес плавки у 300-тонному конверторі триває 50-60 хв. Готову сталь зливають не
через горловину, а через спеціальний отвір, що запобігає перемішуванню металу і шлаку.
Киснево-конверторний спосіб виробництва сталі не потребує значних витрат, він у 5-6 разів
продуктивніший за мартенівський і електричний. Проте два останні способи також мають свої переваги.
Виробництво сталі в мартенівських печах.
Виробництво сталі в мартенівських печах здійснюють з використанням переробного чавуну
(твердого або рідкого) і брухту, іноді замість брухту використовують залізну руду. Як паливо
використовують доменний, коксувальний або природний газ, а також мазут або нафту; флюс - вапняк
СаСО3 (6-12 % від маси металу).
Мартен - регенеративна полуменева піч, в якій висока температура одержується за рахунок згоряння
газу над плавильним простором ((1750-1800°С). Газ і повітря, що надходять до печі, попередньо нагрівають у
регенераторах до 1200-1250°С. Підігрівання продуктів горіння забезпечують у робочому просторі печі при
згорянні палива температурою близько 2000°С. У разі використання рідкого палива нагрівають лише
повітря, а нафту або мазут подають через форсунки, розташовані в каналах головок печі.
Основну частину печі (робочий простір-А) обмежує склепіння (10), задня і передня стінки, головки
(9) з бокових сторін і под (6). Передня стінка має завалочні вікна (11) для завантаження шихти, відбору проб
і спостереження за процесом плавки. Нижня частина задньої стінки має отвори для випуску сталі та шлаку. У
головках печі (2) розташовані канали (7, 8), через які надходять газ і повітря, а також уводяться продукти
горіння. У регенераторах (4, 5) з вертикальними каналами і вогнетривкою насадкою нагрівають газ і повітря.
Через нижні канали (2, 3) до них надходять газ і повітря, вводяться продукти горіння. Періодичним
перемиканням клапанів (1) змінюють напрямок руху потоків газу і повітря, продуктів горіння. Залежно від
характеру кладки (футеровки) поду і стінок печі поділяють на кислі й основні. Використання кислих печей
обмежене.
Процес мартенівської плавки в печі з основною футеровкою поділяють на три періоди: плавлення,
кипіння, розкислення. Під час плавлення до печі подають найбільшу кількість тепла, відбувається окислення
кремнію, марганцю, сірки, фосфору. Оксиди реагують з флюсами і переходять у шлак. Далі починається
кипіння сталі з активним окисленням вуглецю в металі. У процесі кипіння здійснюють хімічний контроль.
Коли вміст вуглецю досягає бажаного, а кількість сірки і фосфору стає мінімальною, кипіння припиняють і
починають розкислення сталі феромарганцем, феросиліцієм, алюмінієм. Кінцеве розкислення сталі
алюмінієм і феросиліцієм здійснюють під час випуску сталі у розливальному ковші. Процес мартенівської
плавки залежно від об'єму печі триває 6-14 год.
За ступенем розкислення сталь поділяють на киплячу (має газові вкраплення), напівспокійну і
спокійну (гази відсутні). Киплячу сталь використовують для невідповідальних деталей; напівспокійну - для
виготовлення дроту, конструкцій; спокійну -для виготовлення ресор, колінчастих валів тощо.
Продуктивність вітчизняних мартенівських печей становить майже 10 т на м2
пода печі. Підвищення
показників роботи печі досягають застосуванням кисневого дуття, двованних печей, автоматизації процесу.
Виробництво сталі в електропечах
Виробництво сталі в електропечах - найважливіший спосіб одержання сталей високої якості для
відповідальних виробів і інструменту. Електроплавка дає можливість здійснювати швидке нагрівання і
підтримувати потрібну температуру в межах до 2000°С, застосовувати окисну, відновлювальну або
нейтральну атмосфери, вакуум. Це дає можливість одержувати сталі та сплави з мінімальною кількістю
шкідливих домішок і оптимальним вмістом потрібних компонентів, забезпечити високу якість металу.
Електроплавку здійснюють у дугових та індукційних печах.
Електродугова піч складається з сталевого циліндра зі
сферичним або похилим днищем, футерованого вогнетривкою цеглою.
Робочий простір печі зверху має склепіння (4) з отворами для
графітизованих електродів (3) діаметром 350-550мм.
На електроди подають електричний струм напругою 200-600 В
і силою 1-10 кА. Джерелом тепла є електрична дуга, що утворюється
між електродами і шихтою. У стінці корпусу розташоване вікно (5)
для завантаження шихти і спостереження за ходом плавки, а також
отвір для випуску металу (2) зі змінним жолобом (1). Механізмом (6)
піч можна нахиляти для завантаження або зливання сталі та шлаку.
Електродугові печі мають об'єм 0,5-400 т. Сталь виготовляють
здебільшого у печах з основною футеровкою плавкою з окисленням
або без окислення домішок.
Плавка з окисленням нагадує мартенівський процес і застосовується для одержання вуглецевих
сталей. Шихтою служить сталевий брухт, переробний чавун, кокс-для навуглецювання і 2-3 % вапна. Після
завантаження печі до електродів підводять струм, виникає дуга з температурою 3500°С. Плавка має два
періоди: окислення і відновлення. На початку плавки залізо, марганець, кремній і вуглець окислюються
киснем, що надходить з повітря, з оксидів шихти та жаровини. Оксиди взаємодіють з вапном, утворюючи
шлак. Наявність у шлаку оксиду кальцію сприяє зв'язуванню і видаленню фосфору. Період відновлення
включає процеси розкислення сталі, видалення сірки і доведення вмісту компонентів до потрібної кількості.
Для цього до печі подають флюс (вапно, фтористий кальцій, кокс, феросиліцій). Кокс і феросиліцій
відновлюють оксид заліза, кількість його у шлаці зменшується і FeO переходить з металу в шлак, де
8
відновлюється на границі шлак -метал. Завдяки цьому сталь не забруднюється домішками (SiO2, МnО, Аl2О3)
на відміну від звичайного розкислення. Присутність у шлаці СаО інтенсивно видаляє сірку. Тому в
електросталі її вміст не перевищує 0,015 %. У разі необхідності наприкінці періоду відновлення сталь
розкислюють феросиліцієм або алюмінієм.
Плавка без окислення застосовується для виготовлення легованих сталей з брухту або відходів
відповідного складу. Процес зводиться до переплаву і введення деяких компонентів сталі.
Індукційна піч складається з тигля з кришкою (склепінням) і
водоохолоджу-ваного індуктора змінного струму з частотою 500-2000
кГц. Електричний струм збуджує в металі вихрові струми з високою
тепловою дією, які нагрівають його до розплавлення. Індукційні печі
виготовляють об'ємом від десятків кілограмів до 5 т (часом 25-30 т).
Плавку здійснюють переплавом відходів легованих сталей або скрапу
вуглецевих сталей і феросплавів. Шлаком є вапно і плавиковий шпат (в
основних печах) або бій скла та інші матеріали, багаті на SiO2 (в кислих
печах). Завдяки індукційним печам одержують сталь з невисоким
вмістом вуглецю і газів; здійснюють плавку у вакуумі або захисній
атмосфері; переміщують рідкий метал; вирівнюють хімічний склад за
рахунок електродинамічних сил, що виникають у процесі плавки.
Тривалість плавки у печі об'ємом 1 т становить близько 45 хв., витрати
електроенергії на виплавку 1 т сталі - 600-700 кВт/год.
Вуглеце́ва сталь — сталь, що містить вуглець (до 2%) поряд з іншими домішками. На відміну від чистих залізовуглецевих сплавів в ній, крім заліза і вуглецю, є постійні домішки (марганець, кремній, сірка, фосфор, кисень, азот, водень) і домішки випадкові (хром, мідь, нікель тощо).
Вуглецеві сталі бувають низько- (до 0,3%
С), середньо- (0,3-0,5% С) і високовуглецеві (понад 0,5% С); доевтектоїдні
(0,02-0,8% С) з феритоперлітною структурою, евтектоїдні (0,8% С) з перлітною структурою і заевтектоїдні (0,8-2% С),
структура яких складається з перліту і вторинного цементиту.
Вуглецеві сталі за призначенням поділяються на: конструкційні сталі, інструментальні сталі і сталі
спеціального призначення (наприклад, для виготовлення котлів, конструкцій
мостів). Механічні властивості вуглецевих
сталей залежать в основному від вмісту вуглецю. З підвищенням його вмісту
збільшуються твердість і міцність, зменшуються пластичність і ударна в'язкість. Вуглецеві сталі застосовують
у машинобудуванні, будівництві тощо.
Класифікація за показниками якості
Якість конструкційних вуглецевих сталей визначається
наявністю в них шкідливих домішок фосфору (P) і сірки (S). Фосфор додає сталі холодноламкості (крихкості). Сірка
(найшкідливіша домішка) — додає сталі червоноламкості. Вміст шкідливих домішок у
залежності від групи якості для конструкційних сталей наступний:
·
Звичайної якості (ДСТУ 2651:2005/ГОСТ 380–2005, ISO
1052—82 — P і S до 0,05% (маркування Ст за ДСТУ або Fe за
ISO).
·
Якісна — P і S до 0,035%
(маркування сталь).
Конструкційні вуглецеві сталі звичайної якості
Широко застосовуються при виготовленні
конструкцій масового призначення в будівництві та машинобудуванні, як відносно
дешеві, технологічні і що характеризуються
необхідними властивостями. В основному ці сталі використовують в гарячекатаному
стані без додаткової термічної обробки з феритно-перлітною структурою.
За ступенем розкислення вуглецеві сталі
звичайної якості поділяються на спокійні (сп), напівспокійні (пс), киплячі
(кп). Ступінь розкислення визначається вмістом кремнію (Si) у цій сталі:
·
спокійні — 0,12…0,03% (Si),
·
напівспокійні — 0,05…0,17% (Si),
·
киплячі — менше 0,07% (Si).
Залежно від подальшого призначення
конструкційні вуглецеві сталі звичайної якості поділяють на три групи: А, Б, В.
·
Сталі групи А. Постачаються з певними
регламентованими механічними властивостями. Їх хімічний склад не
регламентується. Ці сталі застосовуються в конструкціях, вузли яких не
піддаються гарячій обробці — куванням, гарячому штампуванню,
термічній обробці і т. д. У зв'язку з цим механічні властивості
гарячекатаної сталі зберігаються у виробі.
·
Сталі групи Б. Постачаються з певним регламентованим
хімічним складом, без гарантії механічних властивостей. Ці сталі застосовуються
у виробах, що піддаються гарячій обробці, технологія якої залежить від їх
хімічного складу, а кінцеві механічні властивості визначаються самою обробкою.
·
Сталі групи В. Постачаються з регламентованими
механічними властивостями і хімічним складом. Ці сталі застосовуються для
виготовлення зварних конструкцій. Їх зварюваність визначається хімічним
складом, а механічні властивості поза зоною
зварювання визначені у стані постачання. Такі сталі застосовують для
відповідальніших деталей.
Основні марки конструкційних вуглецевих
сталей звичайної якості: Ст0, Ст1кп, Ст1пс, Ст1сп, Ст2кп, Ст2пс, Ст2сп,
Ст3кп, Ст3пс, Ст3сп, Ст3Гпс, Ст3Гсп, Ст4кп, Ст4пс, Ст4сп, Ст5пс, Ст5сп, Ст5Гпс,
Ст6пс, Ст6сп.
·
Ст — вказує на те, що сталь звичайної якості.
·
Перша цифра — номер за ДСТУ 2651:2005 (від 0 до 6) марки, залежить від
хімічного складу сталі (збільшення номера від 1 до 6 означає підвищення вмісту
вуглецю в сталі від 0,06…0,12% до 0,38…0,49%, для сталі Ст0 вміст вуглецю не
більше 0,23%).
·
Літера Г після першої цифри — підвищений вміст марганцю (Mn) (служить для
підвищення прогартовуваності сталі).
·
сп; пс; кп — ступінь розкиснення сталі.
Якісні вуглецеві конструкційні сталі
Вуглецева якісна конструкційна сталь
виробляється згідно з ДСТУ 7809:2015.
Вуглецева якісна конструкційна сталь
поділяється на категорії:
·
машинобудівну — 08, 10,20, 25, 30, 35,
40, 45, 50, 55, 58,60;
·
автоматну — А12, А20, А30;
·
котельну — 20К.
У позначенні марки сталі цифри означають
середній вміст вуглецю в сотих частках відсотка.
Інструментальна вуглецева сталь ділиться
на якісну і високоякісну. Вміст сірки та фосфору в якісній інструментальної
сталі — 0,03% і 0,035%, у високоякісній — 0,02% і 0,03%
відповідно.
Випускається згідно ДСТУ 3833-98 (ГОСТ
1435-99) таких марок: У7; У8; У8Г; У9; У10; У11; У12; У13; У7А;
У8А; У8ГА; У9А; У10А; У11А; У12А; У13А, де цифрами вказано вміст вуглецю в десятих частках
процента (літера А в кінці маркування означає, що сталь
високоякісна, а літера Г, що має підвищений вміст марганцю). Стандарт поширюється
на вуглецеву інструментальну гарячекатану, ковану,
калібровану сталь, сріблянку.
Перевага вуглецевих інструментальних
сталей полягає в основному в їх дешевизні і достатньо високій твердості (HRC 60…62) в порівнянні з іншими інструментальними матеріалами. До
недоліків слід віднести малу зносостійкість і
низьку теплостійкість (250ºС).
У разі більшої температури твердість інструменту значно знижується і він
втрачає свої різальні властивості.
Застосування сталі для виготовлення деталей автомобілів.
Сталі є основними конструкційними матеріалами машинобудування. З простих вуглецевих сталей виготовляють рядовий прокат - балки, швелери, куточки, прутки, а також листи, труби та поковки. Якісні низьковуглецевих сталі використовують для відповідальних зварних конструкцій і деталей виробів, зміцнюючих цементацією. Середньовуглецеві сталі застосовують для виготовлення невеликих деталей або деталей, які не потребують наскрізний прокаливаемости при термообробці.
Сталі з високим вмістом вуглецю (0,6-0,85% С) володіють підвищеною міцністю, зносостійкістю і пружними властивостями. Їх застосовують після термообробки для деталей, що працюють в умовах тертя при наявності високих статичних, вібраційних навантажень (пружин і ресор, шпинделів, прокатних валків і т.п.).
Леговані сталі широко застосовують для важко-навантажених елементів конструкцій машинобудівних виробів. Термічна обробка істотно покращує їх конструктивно-технологічні властивості.
Низьколегованісталі у вигляді листів сортового і фасонного прокату широко використовують для зварних конструкцій. Застосування термічно оброблених профілів і листів з низьколегованих сталей взамін вуглецевих дозволяє заощадити до 15-50% металу.
Високоміцні середньолеговані сталі використовують для високонавантажених деталей. Так, хромансіл (ЗОХГС, 30ХГСН2А) застосовують для виготовлення циліндрів, балок, що працюють на зріз шпильок і осей, групових болтів, навантажених осьовою силою; сталь 40ХСН2МА - для високонавантажених деталей, що не мають значних концентраторів напруги, і т.д.
Високоміцні, високолеговані сталі володіють унікальним комплексом властивостей: високою міцністю при достатній пластичності і в'язкості, високим опором малим пластичних деформацій, тендітному і втомного руйнування в поєднанні з хладостойкое, теплостійкістю, корозійну стійкість і розмірної стабільністю. Їх використовують для високонавантажених деталей, експлуатованих при екстремальних температурах, в агресивних середовищах і т.п.
Машинобудівні конструкційні сталі використовуються для виготовлення деталей машин, конструкцій приладів.
Автоматні конструкційні сталі використовуються для невідповідальних деталей масового виробництва (дрібне кріплення тощо), що виготовляються на верстатах-автоматах.
Котельні конструкційні сталі використовуються для виготовлення котлів та посудин, що працюють під тиском і при температурах до 450 °C.
З вуглецевих інструментальних сталей виготовляють зубила, кернери, напилки, шабери, ножівкові полотна, мітчики, зенкери, розвертки та інші інструменти.
Леговані сталі, їх механічні і технологічні властивості, маркування, галузь застосування.
Сталь, яка містить крім постійних домішок (манган, силіцій) один або кілька спеціальних елементів з вмістом понад 1 %, називають легованою.
До легованих сталей спеціально вводять легувальні елементи, які помітно змінюють їхні механічні і фізико-хімічні властивості. До таких елементів належать хром, нікель, молібден, вольфрам, ванадій, кобальт, титан та ін. Манган у кількості понад 1 % і силіцій понад 0,5 % Також є легувальними.
Властивості легованих сталей визначаються кількістю введених легувальних елементів і характером їх взаємної дії з основними компонентами — залізом і вуглецем. За цією ознакою легувальні елементи можна поділити на дві групи: елементи, які не утворюють карбідів (Ni, Co, Si, Al, Си); карбідоутворювальні елементи (Cr, Μn, Mo, W, V, Ті, Zn, Nb).
Введення легувальних елементів сприяє досягненню якіснішої термічної обробки, оскільки вони надають аустеніту великої стійкості.
ВПЛИВ ЛЕГУВАЛЬНИХ ЕЛЕМЕНТІВ НА СТРУКТУРУ І ВЛАСТИВОСТІ СТАЛІ
Хром — дешевий легувальний елемент. Його широко застосовують для легування (в конструкційних сталях до 3 %). Він підвищує твердість і міцність сталі при одночасному незначному зниженні пластичності і в'язкості. Він частково розчиняється у фериті й одночасно утворює міцні карбіди. Хром підвищує опір корозії — при вмісті понад 13 % С г сталь стає неіржавною. Крім того, хром підвищує жароміцність, а також змінює магнітні властивості сталі. Завдяки високій зносостійкості хромистої сталі з неї виготовляють підшипники кочення. Хром вводять у сплав швидкорізальної сталі.
Нікель — цінний легувальний елемент (у конструкційних сталях 1...5 %) — надає сталі міцності, високої пластичності і в'язкості. Його використовують у значній кількості, якщо потрібно одержати немагнітну сталь і сталь підвищеної антикорозійності. Розчиняючись у фериті, нікель зміцнює його. Для легування інструментальних сталей нікель не застосовують.
Вольфрам — дорогий метал. Він дуже підвищує твердість сталі і надає їй червоностійкості — здатності зберігати твердість за підвищених температур. Його вводять переважно в інструментальні і швидкорізальні сталі.
Ванадій — карбідоутворювальний елемент — підвищує твердість сталі і надає їй червоностійкості, сприяє утворенню дрібнозернистої структури, підвищує пружність. Його вводять в інструментальні й швидкорізальні сталі, в невеликій кількості (0,1...0,3%) — у конструкційні сталі.
Молібден — карбідоутворювальний елемент — підвищує твердість і міцність сталі за підвищених температур. Він сприяє утворенню дрібнозернистості. Молібден вводять у конструкційні, інструментальні й жароміцні сталі.
Манган — недорогий легувальний елемент — є постійною домішкою сталі. В конструкційних сталях мангану не більше ніж 2 %. Він підвищує міцність і твердість сталі. З підвищенням вмісту мангану сталь стає зносо - і магнітостійкою.
Силіцій — постійна домішка сталі. У разі введення в сталь до 1 % силіцію міцність її збільшується при збереженні в'язкості (ресорні і пружинні сталі). Він збільшує кислотостійкість, жароміцність. Силіцій вводять у конструкційні, електротехнічні та інші сталі.
Кобальт — підвищує жароміцність, магнітні властивості, збільшує опір ударам.
Титан — підвищує міцність, сприяє подрібненню зерен, поліпшує оброблюваність і опір корозії.
КЛАСИФІКАЦІЯ МАРКУВАННЯ І ЗАСТОСУВАННЯ ЛЕГОВАНИХ СТАЛЕЙ
Класифікація легованих сталей. Леговані сталі класифікують за призначенням, хімічним складом, якістю та структурою.
За призначенням леговані сталі поділяють на конструкційні, інструментальні і сталі з особливими фізичними і хімічними властивостями.
Конструкційні сталі застосовують для виготовлення деталей машин і будівельних конструкцій. Конструкційні сталі повинні мати високі механічні властивості.
Інструментальні сталі і сплави застосовують для виготовлення різних виробничих інструментів (різальних, вимірювальних і ударно - штамнових).
Інструментальні сталі повинні мати високу твердість і зносостійкість.
Сталі і сплави з Особливими фізичними і хімічними властивостями застосовують для виготовлення деталей, які працюють в особливих умовах. Ці сталі об'єднано в шість груп: неіржавні (корозійностійкі), з високим електроопором, електротехнічні, з особливим тепловим розширенням, магнітні і для роботи за високих температур (жаростійкі й жароміцні).
За хімічним складом сталі поділяють залежно від того, які легувальні елементи і в якій кількості містяться в сталі.
За якістю леговану сталь поділяють на якісну, високоякісну і особливо високоякісну, яка містить сірку (до 0,015 %), фосфор (до 0,025 %). Залежно від головних легувальних елементів сталь поділяють на групи, наприклад Хромиста (15Х, 40Х), Марганцевиста (15Г, 30Г2), Хромонікелева (12ХНЗ, 20ХН), Хромомангановосиліцієва (25ХГС). Залежно від вмісту легувальних елементів леговані сталі поділяють на три групи: Низьколеговані (загальним вмістом легувальних елементів до 3 %), Середньолеговані (3...10 % легувальних елементів) і Високолеговані (понад 10 % легувальних елементів).
За структурою у відпаленому стані леговані сталі бувають Доевтектогдні, які мають у структурі вільний ферит; заевтектоїдні — надмірні карбіди і ледебуритні — первинні карбіди, які відокремилися з рідкої фази. За структурою після охолодження на повітрі леговані сталі поділяють на Перлітні, Мартенситні й Аустенітні. Ця класифікація надзвичайно важлива, оскільки за структурою сталей повністю встановлюють їхні властивості. Наприклад, сталь, яка має перлітну структуру, характеризується невеликою твердістю і високою пластичністю, а сталь, яка має мартенситну структуру, надто тверда і крихка.
Маркування легованих сталей. Для маркування сталей стандартом прийнято такі умовні позначення легувальних елементів: X — хром, Η — нікель, В — вольфрам, Φ — ванадій, Μ — молібден, Γ — манган, Д — мідь, К — кобальт, С — силіцій, Ю — алюміній, Ρ — бор, Б — ніобій, Π — фосфор, Τ — титан, Ц — цирконій.
Марка сталі складається з цифр і літер: якщо на початку марки
Стоять дві цифри (позначають конструкційні сталі), то вони вказують на середній вміст вуглецю в сотих частках відсотка; якщо одна цифра — вміст вуглецю в десятих частках відсотка і якщо спереду
Марки цифри немає, то це означає, що вуглецю в цій сталі 1 % (позначають інструментальні сталі). Цифри, які стоять за літерами, вказують на вміст певної домішки (легувального елемента) у відсотках. Якщо після літери легувального елемента немає цифри, то вміст цього елемента становить до ІД %- Літери в кінці марки означають: А — високоякісна сталь; літера Ш (через дефіс) вказує, що сталь особливо високоякісна (з обмеженим вмістом сірки і фосфору); Л — сталь, призначена для лиття; Я — сталь, розлита у вакуумі. Наприклад, сталь марки 12Х2Н4А — хромонікелева високоякісна сталь з вмістом 0,12 % вуглецю, хрому 2 %, нікелю 4 %; 5ХНМ — легована інструментальна сталь з вмістом 0,5 % вуглецю, хрому, нікелю і молібдену до 1,5 % кожного легувального елемента.
Деякі леговані сталі виділено в окремі групи і на початку марки позначаються літерами: ПІ — підшипникові, ШХ15 (підшипникова хромиста сталь з вмістом 15 % хрому); Ρ — швидкорізальні, Р18 (Р — швидкорізальна сталь, 18 — вміст вольфраму 18 %); Л — лемішна сталь Л65 (65...0,65 % вуглецю); Ε — магнітні сталі; ЕХЗ — магнітотверда хромова сталь (з вмістом 3 % хрому); Св — зварювальна сталь; Нп — наплавлювальна сталь тощо.
ЛЕГОВАНІ КОНСТРУКЦІЙНІ СТАЛІ
Марка сталі
|
С
|
Cr
|
Μn
|
Інші елементи
|
20Х
|
0,17. .0,23
|
0,7...1,0
|
0,5..0,8
|
_
|
20ХГР
|
0,18...0,24
|
0,8...1,1
|
0,7... 1,0
|
(0,60...0Д6)Ті
|
18ХГТ
|
0,17...0,23
|
1,0...1,3
|
0,8...1,1
|
(0,60...0,12) Ті
|
ЗОХГТ
|
0,24... 0,32
|
1,0...1,3
|
0,8...1,1
|
(0,80...0,20) Ті
|
25ХГМ
|
0,22^.0,28
|
1,0... 1,3
|
0,8...1,1
|
(0Д5...0.25) Мо
|
12ХНЗА
|
0,09..0,16
|
0,6...0,9
|
0,3...0,6
|
(2,76...3,15) №
|
Назва деталі
|
Марка сталі
|
Спосіб зміцнення
|
Сільськогосподарські машини
| ||
Полиця плуга
|
Ст2сп
|
Цементація і гартування
|
Леміш плуга
|
Л53, Л65
|
Гартування і відпускання
|
Леміш картоплекопача
|
65Г, 70Г
|
Те саме
|
Лапа культиватора
|
65Г
|
Гартування
|
Диски сівалки, лущильника, борони
|
70Г
|
Те саме
|
Різальні сегменти сінокосарок, жаток
|
Х12М
|
Гартування і відпускання
|
Рама плуга
|
СтЗ. Ст4
|
Без термічної обробки
|
Трактори і автомобілі
| ||
Підшипники кочення
|
ШХ15,
|
Гартування і відпускання
|
ІНХ15СГ
| ||
Зубчасті колеса
|
45, 40Х, 45Х
|
Те саме
|
Колінчасті і розподільні вали
|
40, 45, 45Г2
|
Гартування СВЧ
|
Півосі вантажних автомобілів
|
40
|
Те саме
|
Капоти автомобілів і тракторів, кожу-
|
10
|
Без термообробки
|
Хи, гальмові стрічки, трубки
| ||
Кулачкові вали, осі, пальці, зірочки,
|
15, 20, 25,
|
Цементація, гартування і
|
Навантажувальні вилки тяг, штовхані
|
15Х, 20Х
|
Відпускання
|
Клапанів, пальці ресор, поршневі
| ||
Пальці
| ||
Фрикційні диски, черв'яки
|
15Г, 20Г,
|
Цементація або ціанування.
|
25Г, аохгр,
|
Гартування і відпускання
| |
STXTP,
| ||
20ХГНР
|
Марка
Сталі
|
С
|
Μη
|
Si
|
Cr
|
W
|
V
|
ЗХ
9Х
ХВГ
ХВСГ 9Х5ВФ
|
1,25... 1,40 0.85... 0,95 0,90... 1,05 0,95... 1,05 0,85... 1,00
|
0,30...0,60 0,30...0,60 0,80... 1.10 0,60... 0,90 0,15...0,40
|
0,16.. .0.35
1,20... 1,60 0,15...0,35 0.65... 1,00 0,15... 0,40
|
0.40..0,70 0,95... 1,25 0,90...1,20 0,60... 1,10 4,50.. .5,50
|
_
_
1,20...1,65 0,50..0,80 0,80... 1,20
|
_
_
_
0.05...0,150,15…0,30
|
Конструкційні леговані сталі застосовують для виготовлення різних відповідальніших деталей машин. Залежно від умов роботи вони повинні мати потрібні механічні властивості: високу міцність при значних статичних навантаженнях; пластичність і в'язкість при динамічних навантаженнях; твердість і зносостійкість при спрацюванні тертям.
Із сталей нормальної і підвищеної міцності найбільше застосовують сталі з підвищеною твердістю поверхні і в'язким осердям (цементовані, азотовані і зміцнені СВЧ сталі), які містять не більше ніж 5 % легувальних елементів.
Низьковуглецеві (0,1...0,3 % С) леговані сталі зазнають цементації і нітроцементації. Цими технологічними методами зміцнюють шестерні, зубчасті колеса, черв'яки, осі, важелі, поршневі пальці та інші деталі. Сталі, які зазнають цементації, наведено в табл.
Як легувальні елементи використовують хром, нікель, манган, молібден, титан та ін. Для деталей, які працюють в умовах спрацювання при терті (поршневі пальці, шліци), застосовують сталі марок 15Х, 20Х, 15ХФ, 20ХФ, 18ХГ, а також сталі підвищеної міцності, в'язкості марок 20ХН, 12ХН2М та ін. Для важконавантажених зубчастих коліс з високою міцністю осердя зуба використовують сталі 18ХГТ, 25ХГТ, 25ХГМ, ЗОХГТ. Сталі 20ХГР, 27ХТР, 20ХНР з додаванням бору застосовують для виробів, які працюють на тертя (черв'яки, кулачки, шарніри). Деталі машин, виготовлені з цих сталей, зазнають термічної обробки (гартування і низького відпускання). Низьковуглецеві сталі крім твердої поверхні (58...63 HRC) мають достатньо міцне і в'язке осердя, стійке до навантажень.
Таблиця Масова частка хімічних елементів у деяких легованих конструкційних сталях для цементації, %
Сталі 38Х2Ю і 38Х2МЮА після азотування використовують для виготовлення деталей з великою твердістю і зносостійкістю поверхні (валики водяних насосів, плунжери та ін.).
Для зміцнення поверхневим гартуванням, тобто нагріванням струмом високої частоти (СВЧ), вибирають середньовуглецеві сталі 40Х, 45Х, ШХ4, які застосовують для виготовлення зубчастих коліс, хрестовин, деталей підшипників кочення.
Леговані сталі з вмістом вуглецю 0,4...0,5 % застосовують для великої групи деталей машин, які працюють не тільки при статичних, а й при ударних навантаженнях (вали, штоки, шатуни тощо).
Хромисті сталі 40Х, 45Х, 50Х належать до дешевих конструкційних матеріалів. Із збільшенням вмісту вуглецю в них підвищується міцність, але знижується пластичність і в'язкість.
Хромосиліцієманганові сталі ЗОХГСА, 35ХГСА містять по 1 % Сг, Μη і Si, мають високі технологічні і механічні властивості, їх широко застосовують в автомобілебудуванні (вали, деталі рульового керування).
Хромонікелеві сталі 40ХН, 45ХН, 50ХН мають високий температурний запас в'язкості і меншу схильність до крихкого руйнування порівняно з хромистими.
Для виготовлення пружин і ресор використовують леговані сталі 50С2, 55С2, 50ХФА, 60С2ХА та ін., які характеризуються високою пружністю, стійкістю, достатньою в'язкістю і пластичністю. Для знищення концентраторів напружень (волосових тріщин, рисок тощо) ресори і пружини піддають дробоструминному наклепу, що підвищує строк роботи у 5...8 разів.
Підшипникові сталі ШХ6, ШХ9, ШХіб, ШХ16СГ використовують для виготовлення підшипників кочення. Вони мають високу твердість і витримують велику кількість циклів високих контактних напружень. Перелічені хромисті сталі подібні до вуглецевих сталей
Приблизно з 1 % вуглецю.
Корозійностійка підшипникова сталь ШХ15 (Ш — підшипникова сталь) призначена для виготовлення деталей, які працюють за температури до 500 °С.
Манганова сталь марки 110Г13Л (Л — ливарна сталь) добре протистоїть абразивному спрацьовуванню. З неї відливають ланки гусениць тракторів, а також деталі землерийних машин.
Низьколеговані будівельні сталі застосовують для виготовлення конструкцій зварюванням. Ці сталі працюють без термообробки в процесі виготовлення, тобто в такому стані, в якому випускаються металургійними заводами. Вони мають добре штампуватися, зварюватися, не давати напружень і тріщин біля зварного шва. Найчастіше застосовують високоміцні сталі таких марок: 14ГА, 14ХГС і 15ХГС.
У табл. наведено перелік окремих деталей сільськогосподарської техніки, які виготовлені з конструкційних сталей.
Таблиця Перелік деталей, які виготовлені із конструкційних сталей
ЛЕГОВАНІ ІНСТРУМЕНТАЛЬНІ СТАЛІ
Леговані інструментальні сталі залежно від умов роботи і вимог поділяють на три групи: для Різальних інструментів; для штампувальних інструментів; для вимірювальних інструментів.
Сталі для різальних інструментів, у свою чергу, поділяють на дві групи: Низьколеговані — для інструментів малої і середньої швидкості різання; Високолеговані — для інструментів високої швидкості різання.
Низьколеговані інструментальні сталі легують хромом, манганом, ванадієм і вольфрамом (загальною кількістю до 3...5 %) головним чином для забезпечення високої твердості при гартуванні в мінеральній оливі. Це такі марки сталі: X, 9ХС — для виготовлення різців, свердел, фрез, зенкерів, розверток; ХВГ, 9Х5ВФ — для свердел, мітчиків, розверток; ХВ5 — для інструментів, які обробляють (ріжуть) твердий матеріал. Твердість цих сталей зберігається при нагріванні до 200...300 °С, а сталь 8Х4ВЗМЗФ2 має високу теплостійкість (300...400 °С). Після гартування і низького відпускання низьколеговані сталі мають твердість 60...62 HRC, а сталь ХВ5 — до 65 HRC. Масову частку хімічних елементів у деяких легованих інструментальних сталях наведено в табл. 2.14.

Таблиця Масова частка хімічних елементів у деяких легованих інструментальних сталях, %
Високолеговані інструментальні сталі — це швидкорізальні сталі, які мають мартенситно-карбідну структуру, зберігають твердість при високих швидкостях різання і тому називаються Швидкорізальними, або Рапідними (Rapid — швидкий). Ці сталі здатні зберігати твердість у нагрітому стані до температури 600...640 °С, оскільки структура відпалених швидкорізальних сталей має до 25 % карбідів. Щоб надати сталі найкращих різальних властивостей, потрібно максимальну кількість легувальних елементів перевести з карбідів у твердий розчин. Цього досягають гартуванням швидкорізальної сталі за температури 1200... 1300 °С. Після такого гартування структура сталі складається з мартенситу, карбідів і залишкового аустеніту (близько 30 %). Наступним дво - або триразовим відпусканням за температури 560 °С зменшують вміст залишкового аустеніту до 3...5 %.
Сталь марок Р9, Ρ12, Ρ18 застосовують для виготовлення всіх видів різальних інструментів при обробці конструкційних матеріалів: Р6М5 — для різьбонарізних інструментів, які працюють з ударними навантаженнями. Сталі марок Р18К5Ф2, Р9М4К8, Р6М5К5 призначені для обробки корозійностійких, жароміцних сталей і твердих матеріалів. Сталь із підвищеним вмістом ванадію (Р9Ф5, Р14Ф14, Р9К5Ф5) застосовують для обробки титанових сплаві» і матеріалів: пластмас, фібри, ебоніту. Масову частку хімічних елементів у деяких марок швидкорізальних сталей наведено в табл.
Таблиця Масова частка хімічних елементів у деяких швидкорізальних сталях,%

Штампові сталі повинні бути твердими, міцними і мати достатню в'язкість для запобігання поломкам штампів при ударному навантаженні, а сталі для гарячого штампування мають зберігати свою твердість і міцність за підвищених температур (до 900... 1200 *0.
Для виготовлення штампів гарячого штампування металів (ковальських штампів) застосовують сталі марок 5ХНМ, 5ХНТ, які мають велику в'язкість (наявність нікелю), а також сталі марок ЗХ2В8Ф, 4Х2В5ФМ, які характеризуються значною стійкістю за високих температур.
Для виготовлення штампів холодного деформування металів застосовують сталі марок X, 9ХС, ХГ, Х8Г, які мають високу твердість.
Запровадження сталей марок 4ХМФС, 5Х2СФ і 4ХСНМФЦР (замість 6ХНМ) для штампування вуглецевих і низьколегованих сталей дало змогу підвищити стійкість інструментів у 2...З рази. Для виготовлення великогабаритних пресових і молотових штампів застосовують сталь 6Х2НМФС, яка забезпечує підвищення стійкості більш як удвічі.
Запровадження сталі марки 4Х2Н5МЗК5Ф (замість сталі ЗХ2В8Ф) при виготовленні матриць для пресування мідних сплавів дало змогу підвищити їхню стійкість у 10 разів.
Сталі для вимірювального інструменту повинні мати високу стійкість до спрацювання, невеликий коефіцієнт лінійного розширення і здатність тривалий час зберігати задані розміри. Цим вимогам відповідають низьколеговані сталі марок X, ХГС, ХВГ, 9ХС. Зі сталей цих марок виготовляють вимірювальний інструмент високого класу точності (калібри, мікрометри, вимірювальні плитки).
ЗАКРІПЛЕННЯ НОВОГО МАТЕРІАЛУ
І так, підбиваючи підсумок уроку давайте повторимо:
1. Що таке сталь?
2. За якими ознаками класифікують сталі?
3. Як класифікують сталі за хімічним складом?
4. Що означає леговані сталі?
5. Як називається сталь з вмістом вуглецю 0,8%?
6. Де застосовують інструментальні сталі?
7. Які сталі поділяються за постачання на три групи?
8. Як маркують сталі звичайної якості?
9. Що означає сталі група «В»?
10. Як класифікують сталі за хімічним складом?
11. Зміст вуглецю в конструкційних сталях.
12. Скільки марганцю в сталі марки 40Х15Н7Г7Ф2МС?
13. Що означають цифри в марках вуглецевих конструкційних сталей звичайної якості?
14. Скільки вуглецю в сталі У10?
15. Скільки хрому в сталі марки 95Х18?
16. Скільки вуглецю в сталі марки 09Г2С?
Кольорові
метали: мідь, олово,
цинк, свинець, алюміній,
магній, їх властивості, галузь застосування.
За фізичними
властивостями і призначенню кольорові метали умовно можна розділити на
благородні, важкі, легкі й рідкі.
До шляхетних
металів відносять метали з високою корозійною стійкістю: золото, платина, паладій, срібло, іридій, родій, рутеній і осмій. Їх
використовують у вигляді сплавів в електротехніці, електровакуумної техніці,
приладобудуванні, медицині і т.д.
До важких
відносять метали з великою щільністю: свинець, мідь, хром, кобальт і
т.д. Важкі метали застосовують
головним чином як легуючі елементи, а такі метали, як мідь, свинець, цинк, кобальт частково, використовуються
і в чистому вигляді.
До легких
металів відносяться метали з щільністю менше 5 грам на кубічний
сантиметр: літій, калій, натрій, алюміній і т.д.
Їх застосовують як розкислювачів металів і сплавів, для легування, в
піротехніці, фотографії, медицині і т.д.
До рідкісних
металів відносять метали з особливими властивостями: вольфрам, молібден, селен, уран і т.д.
До групи
широко застосовуються кольорових металів відносяться алюміній, титан, магній, мідь, свинець, олово.
Кольорові
метали мають цілу низку дуже цінних властивостей. Наприклад, високу
теплопровідність (алюміній, мідь),
дуже малою щільністю (алюміній, магній), високою корозійною стійкістю
(титан, алюміній).
За
технологією виготовлення заготовок і виробів кольорові сплави діляться на
деформуються і литі (іноді спечені).
На підставі
цього поділу розрізняють металургію легких металів і металургію важких металів.
1. Мідь та її сплави
Мідь - метал червоного, в зламі
рожевого кольору. Мідь належить
до металів, відомим з глибокої давнини.
Технічно
чиста мідь володіє
високою пластичністю і корозійною стійкістю, високою електропровідністю і
теплопровідністю (100% чиста мідь-еталон, то 65%-алюміній, 17% залізо), а також стійкістю проти атмосферної корозії.
Дозволяє використовувати її в якості покрівельного матеріалу відповідальних
будівель.
Температура
плавлення міді 1083 ° С. Кристалічна решітка ГЦК. Щільність міді
8,94 г / см 3. Завдяки високій пластичності
мідь добре обробляється тиском (з міді можна зробити фольгу товщиною 0,02 мм),
погано різанням.
Ливарні
властивості низькі через велику усадки.
На
властивості міді великий вплив мають домішки: всі, крім срібла та берилію
погіршують електропровідність.
Вартість
чистої міді постійно підвищується, а світові запаси мідної руди, за
різними оцінками, виснажаться в найближчі 10-30
років.
Мідь
маркують буквою М, після якої стоїть цифра. Чим більше цифра, тим більше в ній
домішок. Найвища марка М00 - 99,99% міді, М4 - 99% міді.
Після
позначення марки вказують спосіб виготовлення міді: к-катодна, б - безкиснева,
р - раскисленная. Мідь вогневого рафінування не позначається.
М00к -
технічно чиста катодна мідь, що містить не менше 99,99% міді і срібла.
МОЗ -
технічно чиста мідь вогневого рафінування, містить не менше 99,5% міді.
1.1 Сплави
міді
У техніці
застосовують 2 великі групи мідних сплавів: латуні та бронзи.
1.1.1 Латуні
Латуні - сплави міді з цинком (до 50%
Zn) і невеликими добавками алюмінію, кремнію, свинцю, нікелю, марганцю (ГОСТ
15527-70, ГОСТ 17711-80). Мідні сплави, призначені
для виготовлення деталей методами лиття, називають ливарними, а сплави,
призначені для виготовлення деталей пластичним деформуванням - сплавами,
оброблюваними тиском.
Латуні
дешевше міді і перевершують її по міцності, в'язкості і корозійної стійкості.
Володіють хорошими ливарні властивості.
Латуні,
застосовуються в основному для виготовлення деталей штампуванням, витяжкою,
розкочуванням, гнуття, тобто процесами, які вимагають високої пластичності
матеріалу заготовки. З латуні виготовляються гільзи різних боєприпасів.
У залежності
від числа компонентів розрізняють прості (подвійні) і спеціальні
(багатокомпонентні) латуні.
Прості
латуні містять тільки Cu і Zn.
Спеціальні латуні
містять від 1 до 8% різних легуючих елементів (Л.Е.), що підвищують механічні
властивості і корозійну стійкість.
Al, Mn, Ni
підвищують механічні властивості і корозійну стійкість латуней. Свинець
покращує оброблюваність різанням. Крем'янисті латуні мають гарну
жидкотекучестью і зварюваністю.
1.1.2 Бронзи
Бронзи - це сплави міді з оловом
(4-33% Sn), свинцем (до 30% Pb), алюмінієм (5-11%
AL), кремнієм (4-5%
Si), сурмою, фосфором та іншими елементами.
Бронзи - це
будь-мідний сплав, крім латуні. Це сплави міді, в яких цинк не є основним легирующим
елементом. Загальною характеристикою бронз є висока корозійна стійкість і
антифрикційні (від анти-і лат. Frictio-тертя). Бронзи відрізняються високою
корозійною стійкістю і антифрикційними властивостями. З них виготовляють
вкладиші підшипників ковзання, вінці черв'ячних зубчастих коліс і інші деталі.
Високі
ливарні властивості деяких бронз дозволяють використовувати їх для виготовлення
художніх виробів, пам'ятників, дзвонів.
За хімічним
складом поділяються на олов'яні бронзи і без олов'яні (спеціальні).
Олов'яні
бронзи мають
високі механічні, ливарними, антифрикційними властивостями, корозійною
стійкістю, оброблюваністю різанням, але мають обмежене застосування через
дефіцитності і дорожнечі олова.
Спеціальні
бронзи не
тільки служать замінниками олов'яних бронз, а й у ряді випадків перевершують їх
за своїми механічними, антикорозійним і технологічним властивостям:
Алюмінієві бронзи
- 5-11% алюмінію. Мають більш високі механічні та антифрикційні властивості,
ніж в олов'яних бронз, але ливарні властивості - нижче. Для підвищення
механічних і антикорозійних властивостей вводять залізо, марганець, нікель
(наприклад, БрАЖ9-4). З цих бронз виготовляють різні втулки, що направляють,
дрібні відповідальні деталі.
Берилієві
бронзи містять 1,8-2,3% берилію відрізняються високою твердістю, зносостійкістю
і пружністю (наприклад, БрБ2, БрБМН1, 7). Їх застосовують для пружин в
приладах, які працюють в агресивному середовищі.
Крем'янисті
бронзи - 3-4% кремнію, леговані нікелем, марганцем, цинком за механічними
властивостями наближаються до сталей.
Свинцюваті
бронзи містять 30% свинцю, є хорошими антифрикційними сплавами і йдуть на
виготовлення підшипників ковзання.
Мідні сплави позначають
початковими буквами їх назви (Бр або Л), після чого слідують перші літери назв
основних елементів, що утворять сплав, і цифри, що вказують кількість елементу у
відсотках.
Приклади:
·
БрА9Мц2Л -
бронза, що містить 9% алюмінію, 2% Mn, решта Cu («Л» вказує, що сплав
ливарний);
·
ЛЦ40Мц3Ж -
латунь, що містить 40% Zn, 3% Mn, ~ l% Fe, решта Cu;
·
Бр0Ф8 ,0-0,
3 - бронза містить 8% олова і 0,3% фосфору;
·
ЛАМш77-2-0,
05 - латунь містить 77% Cu, 2% Al, 0,055 миш'яку, решта Zn (у позначенні
латуні, призначеної для обробки тиском, перше число вказує на вміст міді).
У нескладних
за складом латунях вказують тільки вміст у сплаві міді:
·
Л96 - латунь
містить 96% Cu і ~ 4% Zn (томпак);
·
Лб3 - латунь
що містить 63% Cu і 37% Zn.
Висока
вартість міді і сплавів на її основі призвела в 20 столітті до пошуку
матеріалів для їх заміни. В даний час їх успішно замінюють пластиками,
композиційними матеріалами.
2. Алюміній і його сплави
Алюміній - метал сріблясто-білого
кольору. Температура плавлення 650 ° С. Алюміній має
кристалічну ГЦК грати. Алюміній має електричнупровідність,
складовою 65% електричної провідності міді. Алюміній займає 3 місце з поширення
в земній корі після кисню і кремнію. Алюміній стійкий проти атмосферної корозії
завдяки утворенню на його поверхні щільної
окисної плівки. Найбільш важливою особливістю алюмінію є низька щільність - 2,7
г / см 3 проти 7,8 г / см 3 для заліза і 8,94 г / см 3 для міді. Має хорошу тепло-і
електропровідність. Добре обробляється тиском.
Маркується
літерою А і цифрою, що вказує на вміст алюмінію. Алюміній особливої чистоти
має марку А999 - вміст Al в цій марці 99,999%. Алюміній високої чистоти - А99,
А95 містять Al 99,99% і 99,95% відповідно. Технічний алюміній - А85, А8, А7 і
ін
Застосовується
в електропромисловості для виготовлення провідників струму, в харчовій і
хімічній промисловості. Алюміній не стійкий у кислому і лужному середовищі,
тому алюмінієвий посуд не використовується для маринадів, солінь, кисломолочних
продуктів. Застосовується як розкислювача при виробництві сталі, для
алітірованія деталей з метою підвищення їх жаростійкості. У чистому вигляді
застосовується рідко через низьку міцності - 50 МПа.
Деформуємі алюмінієві сплави
У залежності
від можливості термічного зміцнення деформуються алюмінієві сплави поділяються
на не зміцнюється і зміцнюється термічною обробкою.
До сплавів,
неупрочняемим т / о відносяться сплави Al c Mn (АМц1), і сплави Al c Mg (Aмг 2,
АМг3). Цифра - умовний номер марки.
Ці сплави
добре зварюються, мають високі пластичні властивості і корозійною стійкістю,
але невисокою міцністю, зміцнюють ці сплави нагартовка. Сплави даної групи знайшли застосування
в якості листового матеріалу, що використовується для виготовлення складних за
формою виробів, одержуваних холодної та гарячої штампуванням і прокаткою.
Вироби, одержувані глибокої витяжкою, заклепки, рами і т.д.
Сплави,
зміцнюється т / о, широко застосовуються в машинобудуванні, особливо в
літакобудуванні, тому що володіють малою питомою вагою при досить високих
механічних властивостях. До них відносяться:
Дуралюмина -
основні легуючі компоненти - мідь і магній:
Д1 - лопаті
повітряних гвинтів, Д16 - обшивки, шпангоути, лонжерони літаків, Д17 - основний
заклепувальний сплав.
Високоміцні
сплави - В95, В96 поряд з міддю і магнієм містять ще значна кількість цинку.
Застосовують для високонавантажених конструкцій.
Сплави
підвищеної пластичності та корозійної стійкості - АВ, АД31, АД33. Лопаті
вертольотів, штамповані і ковані деталі складної конфігурації.
Ливарні
алюмінієві сплави
Найбільш
широко поширені сплави системи Al-Si-силуміни.
Силумін має
поєднання високих ливарних і механічних властивостей, мала питома вага. Типовий
силумін сплав АЛ2 (АК12) містить 10-13% Si, Піддається загартуванню і старіння (АК7
(АЛ9), АК9 (АЛ4).
3. Цинк і його сплави
Цинк - в'язкий метал
голубувато-сірого кольору. Метал з невеликою температурою плавлення (419
градусів С) і високою щільністю (7,1 г / см 3).Міцність цинку низька (150 МПа) при
високій пластичності.
Цинк застосовують
для гарячого та гальванічного оцинкування сталевих листів, у поліграфічній промисловості,
для виготовлення гальванічних елементів. Його використовують як добавку в
сплави, в першу чергу в сплави міді (латуні і т.д.), і як основу для цинкових
сплавів, а також як друкарський метал.
У залежності
від чистоти цинк ділиться на марки ЦВ00 (99,997% Zn), ЦВ0 (99,995% Zn), ЦВ
(99,99% Zn), Ц0А (99,98% Zn), Ц0 (99,975% Zn), Ц1 (99 , 95% Zn), Ц2 (98,7% Zn),
ЦЗ (97,5% Zn).
Цинкові
сплави широко застосовуються в машинобудуванні і поділяються на сплави для
лиття під тиском, в кокіль, для відцентрового лиття та на антифрикційні сплави.
Основними легуючими компонентами цинкових сплавів є алюміній, мідь і магній.
Відлиття з цинкових сплавів легко поліруються і сприймають гальванічні
покриття.
Склад,
властивості та застосування деяких цинкових сплавів:
·
ЦА4 містить
3.9-4.3% Al, 0,03-0,06% Mg, тимчасовий опір 250-300 МПа, пластичність 3-6%,
твердість 70-90HB). Застосовується при литті під тиском деталей, до яких
пред'являються вимоги стабільності розмірів та механічних властивостей.
·
ЦАМ10-5Л
містить 9,0-12,4% Al, 4,0-5,5% Cu, 0,03-0,06% Mg, тимчасовий опір не менше 250
МПа, пластичність не менше 0,4%, твердість - не менш 100HB. З сплаву
виготовляють підшипники і втулки металообробних верстатів,
пресів, що працюють під тиском до 200-10000 Па.
·
ЦАМ9-1.5
містить 9,0-11,0% Al, 1,0-2,0% Cu, 0,03-0,06% Mg, тимчасовий опір не менше 250
МПа, пластичність не менше 1%, твердість не менш 90HB. Сплав застосовують для
виготовлення різних вузлів тертя і підшипників рухомого складу.
4. Магній та його сплави
Магній - метал сріблясто-білого
кольору. Температура плавлення магнію 650 ° С. Кристалічна решітка
гексагональна. Відрізняється низькою щільністю (1,74 г / см 3), хорошою оброблюваністю
різанням, здатністю сприймати ударні і гасити вібраційні навантаження.
У залежності
від вмісту домішок встановлені наступні марки магнію: Мг96 (99,96% Mg), Мг95
(99,95% Mg), Мг90 (99,90% Mg), магній високої чистоти (99,9999% Mg).
Магній хімічно
активний метал, легко окислюється на повітрі. Чистий магній з-за низьких
механічних властивостей (тимчасовий опір 100-190 МПа, відносне подовження
6-17%, твердість 30-40НВ) як конструкційний матеріал практично
не застосовують. Його використовують в піротехніку, в хімічній промисловості
для синтезу органічних сполук, в металургії різних металів і сплавів як
розкислювач, відновник і легуючий елемент.
4.1 Сплави на
основі магнію
Перевагою
магнієвих сплавів є висока питома міцність. Межа міцності магнієвих сплавів
досягає 250-400 МПа при щільності менше 2 грамів на кубічний сантиметр. Сплави в гарячому стані добре
куються, прокочуються і пресуються. Магнієві сплави добре обробляються різанням
(краще, чим стали, алюмінієві та мідні сплави), добре
шліфуються і поліруються. Задовільно зварюються контактної і дугового зварювання в
середовищі захисних газів.
До недоліків
магнієвих сплавів поряд з низькою корозійною стійкістю і малим модулем
пружності слід віднести погані ливарні властивості, схильність до
газонасичення, окислювання і займання при їх приготуванні.
За
механічними властивостями магнієві сплави поділяють на сплави невисокою і
середньої міцності, високоміцні і жароміцні, по схильність до зміцнення за
допомогою термічної обробки - на зміцнюється і неупрочняемие.
Деформуємі
магнієві сплави. У сплавах МА1 і МА8 основним легирующим елементом є марганець.
Термічною обробкою ці сплави не упрочняются, мають гарну корозійною стійкістю і
здатністю до зварювання. Сплави МА2-1 і МА5 відносяться до системи Mg-Al-Zn-Mn.
Алюміній і цинк підвищують міцність сплавів, надають хорошу технологічну
пластичність, що дозволяє виготовляти з них ковані і штамповані деталі складної
форми (крильчатки і жалюзі капота літака). Сплави системи Mg-Zn, додатково
леговані цирконієм (МА14), кадмієм, рідкісноземельними металами (МА15, МА19 та
ін) відносять до високоміцних магнієвим сплавам. Їх застосовують для
незварюваний сильно навантажених деталей (обшивки літаків, деталей
вантажопідйомних машин, автомобілів, ткацьких верстатів та ін.)
Ливарні
магнієві сплави. Найбільше застосування знайшли сплави системи Mg-Al-Zn (МЛ5,
МЛ6). Вони широко застосовуються в літакобудуванні (корпуси приладів, насосів,
коробок передач, ліхтарі і
двері кабін і т.д.), ракетній техніці (корпуси ракет, обтічники, паливні й
кисневі баки, стабілізатори), конструкціях автомобілів, особливо гоночних
(корпусу, колеса , помпи та ін), в приладобудуванні
(корпуси і деталі приладів). Внаслідок малої здатності до поглинання теплових
нейтронів магнієві сплави використовують в атомній техніці, а завдяки високій
демпфирующей здібності - при
виробництві кожухів для електронної апаратури.
Більш
високими технологічними і механічними властивостями володіють сплави магнію з
цинком і цирконієм (МЛ 12), а також сплави, додатково леговані кадмієм (МЛ8),
рідкісноземельними металами (МЛ9, МЛ10). Дані сплави застосовують для
навантажених деталей літаків і авіадвигунів (корпусів компресорів, картерів,
ферм шасі, колонок управління та
ін.)
Магнієві сплави піддаються таким
видам термічної обробки: Т1 - старіння, Т2 - відпал, Т4 - гомогенізація і гарт
на повітрі, Т6 - гомогенізація, гарт на повітрі і старіння, Т61 -
гомогенізація, загартування у воду
і старіння.
Цікаві факти про метали
§ Самим твердим металом
на Землі є хром. Цей блакитно-білий метал був відкритий в 1766 році під
Єкатеринбургом.
§ І навпаки, найбільш
м’якими металами є алюміній, срібло та мідь. Завдяки своїй м’якості вони
знайшли широке застосування в різних областях, наприклад, в електроапаратобудуванні.
§ Золото – яке протягом
століть було самим дорогоцінним металом має і ще одну цікаву властивість – це
самий пластичний метал на Землі, що володіє до того ж відмінною тягучістю та
ковкістю. Також золото не окислюється при нормальній температурі (для цього
його треба нагріти до 100С), володіє високою теплопровідністю і
вологостійкістю. Напевно всі ці фізичні характеристики роблять справжнє золото
таким цінним.
§ Ртуть – унікальний
метал, перш за все тим, що він єдиний з металів, що має рідку форму. Причому в
природних умовах ртуті в твердому вигляді не існує, оскільки її температура
плавлення -38С, тобто в твердому стані вона може існувати в місцях, де просто
таки дуже холодно. А при кімнатній температурі 18С ртуть починає випаровуватися.
§ Вольфрам цікавий тим,
що це найбільш тугоплавкий метал у світі, щоб він почав плавитися потрібна
температура 3420С. Саме з цієї причини в електричних лампочках нитки
розжарювання, що приймають основний тепловий удар, виготовлені з вольфраму.
Термообробка сплавів,види,призначення.
Повний дифузійний розпад аустеніту відбувається при незначному переохолодженні. У даному випадку утворюється пластинчастий перліт (механічна суміш фериту і цементиту вторинного). Якщо переохолодження збільшити до 373-393 0К, пластинки фериту і цементиту встигають вирости тільки до товщини (0,25-0,30 мнм), таку структуру називають сорбітом. Твердість сорбіту вища за твердість перліту.
Коли переохолодження досягає 453-473 0К, ріст пластинок припиняється на товщині 0,1-0,15 мнм, така структура називається трооститом. Твердість трооститу вища від твердості сорбіту.
При значному переохолодженні аустеніту (до 513 0К) дифузійний розпад його стає неможливим, перекристалізація має бездифузійний характер. У такому випадку утворюється перенасичений твердий розчин вуглецю в залізі, який називається мартенситом. Твердість мартенситу вища від твердості трооститу.
Структура перліту є рівноважною, а структури сорбіту, трооститу і мартенситу є не рівноважними.
1. Види термічної обробки
Розрізняють такі види термічної обробки: відпал, нормалізація, загартування і відпуск.
Відпал. Відпалом називають нагрівання до високих температур, видержування і повільне охолодження разом з піччю.
Розрізняють такі види відпалу: рекристалізаційний, дифузійний, на зернистий перліт, ізотермічний, повний і неповний. Відпал підвищує пластичність, зменшує внутрішні напруження, понижує твердість сталей.
Нормалізація. Нормалізацією називають нагрівання до високої температури, видержування і повільне охолодження на повітрі. Нормалізація доводить сталь до дрібнозернистої та однорідної структури. Твердість і міцність сталі після нормалізації вищі, ніж після відпалу.
Загартування сталі. Загартуванням називають нагрівання до високої температури, видержування і швидке охолодження (у воді, мінеральній оливі та інших охолоджувачах). Є такі види загартування: в одному охолоджувачі; перервне; ступінчасте; ізотермічне; поверхневе та ін. Загартування сталей забезпечує підвищення твердості, виникнення внутрішніх напружень і зменшення пластичності. Твердість збільшується у зв'язку з виникненням таких структур: сорбіт, троостит, мартенсит. Практично загартуванню піддається середньо- і високовуглецеві сталі.
Відпуск сталі. Відпуском називають нагрівання до температур нижче 973 0К, видержування і повільне охолодження на повітрі.
Розрізняють три види відпуску: низький (нагрівання до температури 473 0К; середній (573-773 0К); високий (773-973 0К). Після відпуску в деякій мірі зменшується твердість і внутрішні напруження, збільшується пластичність і в'язкість сталей. До цього приводить зміна структур після відпуску. Структура мартенситу сталі переходить відповідно в структуру трооститу і сорбіту. Чим вища температура відпуску, тим менша твердість відпущеної сталі і тим більша її пластичність та в'язкість.
Відпуск, в основному, проводять після загартування для зняття внутрішніх напружень. Низький відпуск застосовують при виготовленні різального інструменту, вимірювального інструменту, цементованих деталей та ін..; середній - при виробництві ковальських штампів, пружин, ресор; високий - для багатьох деталей, що зазнають дії високих напружень (осі автомобілів, шатуни і т.п.).
2. Основи теорії хіміко-термічної обробки
Хіміко-термічною обробкою називають насичення поверхні виробу різними елементами.
Мета хіміко-термічної обробки - надати поверхневому шару стальних деталей підвищеної твердості, зносостійкості, жаростійкості, корозійної стійкості та ін. Для цього нагріті деталі поміщають у середовище, з якого в процесі дифузії у поверхневий шар переходять деякі елементи (вуглець, азот, алюміній, хром, кремній, бор та ін.).
Такі елементи найкраще поглинаються тоді, коли вони виділяються в атомарному стані при розпаді якої-небудь сполуки. Подібний розпад найлегше відбувається у газах, тому їх і намагаються застосовувати для хіміко-термічної обробки сталі. Активізований атом елемента, що виділяється при розпаді, проникає у решітку кристалів сталі і утворює твердий розчин або хімічну сполуку. Найпоширенішими видами хіміко-термічної обробки сталі є: цементація, азотування, ціанування, дифузійна металізація.
Цементацією називається насичення поверхні стального виробу вуглецем. Після загартування такого виробу він стає твердим на поверхні і в'язким у серцевині. Цементації піддають в основному деталі, які працюють на стирання і удар одночасно. Цементація придатна для маловуглецевих сталей. Є два види цементації: цементація твердим карбюризатором і газова цементація.
Азотування - це насичення поверхневого шару виробу азотом, щоб надати йому високої твердості, підвищити зносостійкість та опір агресивним середовищем. Азотують леговану сталь, що містить алюміній, титан, ванадій, вольфрам, молібден або хром. Такі елементи, при взаємодії з азотом, утворюють тверді, стійкі в агресивних середовищах нітриди (TіN і т.п.).
Ціанування - насичення поверхневого шару виробів одночасно вуглецем і азотом. Воно буває рідинне і газове, низькотемпературне (773-9730К), високотемпературне (1073-1123 0К). Ціанування в основному застосовують для обробки інструментів із швидкорізальної сталі, підвищується твердість і корозійна стійкість.
Дифузійна металізація - насичення поверхневого шару виробу різними металами. Найбільш поширені: алютування (насичення алюмінієм); хромування (насичення хромом); нікелювання (насичення нікелем); силіціювання (насичення кремнієм). Дифузійна металізація проводиться для підвищення твердості, корозійної стійкості, жаростійкості.
3. Спосіб хіміко-термічної обробки деталей із металів та сплавів
Спосіб хіміко-термічної обробки деталей із металів та сплавів, який включає їх обробку в парогазовому середовищі з наступним охолодженням до кімнатної температури на повітрі, який відрізняється тим, що обробку проводять перегрітою парою водного розчину 5-8 % алюмохромофосфатної солі при температурі 600±20°С протягом 30-60 хвилин, а охолодження проводять до температури 200°С разом з контейнером, а потім на повітрі. Винахід відноситься до металургії, а саме до зміцнення деталей із металів та сплавів дифузійним насиченням металічної поверхні в твердому стані елементами, які підвищують експлуатаційні властивості матеріалу, та може бути використаний в машинобудуванні, для отримання зносостійких покриттів.
4. Відпал
Відпал - термічна обробка полягає в нагріванні металу до певних температур, витримка і подальшого дуже повільного охолодження разом з піччю. Застосовують для поліпшення обробки металів різанням, зниження твердості, отримання зернистої структури, а також для зняття напружень, усуває частково (або повністю) всякого роду неоднорідності, які були внесені в метал при попередніх операціях (механічна обробка, обробка тиском, лиття, зварювання), покращує структуру сталі.
Відпал першого роду . Це відпал при якому не відбувається фазових перетворень, а якщо вони мають місце, то не роблять впливу на кінцеві результати, передбачені його цільовим призначенням. Розрізняють такі різновиди відпалу першого роду: Гомогенізаціонний і рекрісталлізаціонний.
Гомогенізаціоний - це відпал з тривалою витримкою при температурі вище 950 С (Зазвичай 1100-1200 С) з метою вирівнювання хімічного складу.
Рекрісталлізаціоний - це відпал наклепаної сталі при температурі, що перевищує температуру початку рекристалізації, з метою усунення наклепаного отримання певної величини зерна.
Відпал другого роду. Це відпал, при якому фазові перетворення визначають його цільове призначення. Розрізняють такі види: повний, неповний, дифузійний, ізотермічний, світлий, нормалізований (Нормалізація), сфероідізірующій (на зернистий перліт).
Повний відпал виробляють шляхом нагрівання сталі на 30-50 ° С вище критичної точки, витримкою при цій температурі і повільним охолодженням до 400-500 ° С зі швидкістю 200 ° С на годину вуглецевих сталей, 100 ° С на годину для низьколегованих сталей і 50 ° С на годину для високолегованих сталей. Структура стали після відпалу рівноважна, стійка.
Неповний відпал проводиться шляхом нагрівання сталі до однією з температур, що знаходиться в інтервалі перетворень, витримкою і повільним охолодженням. Неповний відпал застосовують для зниження внутрішніх напружень, зниження твердості і поліпшення оброблюваності різанням.
Дифузійний відпал . Метал нагрівають до температур 1100-1200 Вє С, так як при цьому більш повно протікають дифузійні процеси, необхідні для вирівнювання хімічного складу.
Ізотермічний відпал полягає в наступному: сталь нагрівають, а потім швидко охолоджують (частіше перенесенням в іншу піч) до температури, що знаходиться нижче критичної на 50-100 С. В основному застосовується для легованих сталей. Економічно вигідний, так як тривалість звичайного відпалу (13 - 15) год, а ізотермічного відпалу (4 - 6) год полягає в нагріванні сталі вище критичної температури на 20 - 30 ° С, витримці при цій температурі і повільному охолодженні.
Світлий відпал здійснюється за режимами повного або неповного відпалу із застосуванням захисних атмосфер в печах з частковим вакуумом. Застосовується з метою захисту поверхні металу від окислення і обезуглероживания.
Нормалізація - полягає в нагріванні металу до температури на (30-50) ° С вище критичної точки і наступного охолодження на повітрі. Призначення нормалізації різна залежно від складу сталі. Замість відпалу низьковуглецевих сталі піддають нормалізації. Для середньовуглецевих сталей нормалізацію застосовують замість гарту і високого відпустки. Високовуглецеві стали піддають нормалізації з метою усунення цементітной сітки. Нормалізацію з подальшим високим відпусткою застосовують замість відпалу для виправлення структури легованих сталей. Нормалізація в порівнянні з відпалом - Більш економічна операція, так як не вимагає охолодження разом з піччю.
Загартування - це нагрів до оптимальної температури, витримка і подальше швидке охолодження з метою отримання нерівноважної структури.
У результаті загартування підвищується міцність і твердість і понижується пластичність сталі. Основні параметри при загартування - температура нагріву і швидкість охолодження. Критичною швидкістю гарту називається швидкість охолодження, забезпечує отримання структури - мартенсит або мартенсит і залишковий аустеніт.
У Залежно від форми деталі, марки сталі та необхідного комплексу властивостей застосовують різні способи гарту.
Загартування в одному охолоджувачі. Деталь нагрівають до температури загартування і охолоджують в одному охолоджувачі (вода, масло).
Загартування в двох середовищах (переривчаста гарт) - це гарт при якій деталь охолоджують послідовно в двох середовищах: перше середовище - охолоджуюча рідина (вода), друге - повітря або масло.
Ступеневе гартування. Нагріту до температури гарту деталь охолоджують в розплавлених солях, після витримки в плині часу необхідного для вирівнювання температури по всьому перетину, деталь охолоджують на повітрі, що сприяє зниженню гартівних напруг.
Ізотермічне гартування так само, як і ступінчасте, проводиться у двох охолоджуючих середовищах. Температура гарячої середовища (соляні, селітрові або лужні ванни) різна: вона залежить від хімічного складу сталі, але завжди на (20-100) ° С вище точки мартенситного перетворення для даної сталі. Остаточне охолодження до кімнатної температури проводиться на повітрі.
Ізотермічне гартування широко застосовується для деталей з високолегованих сталей. Після ізотермічного загартування сталь набуває високі міцнісні властивості, тобто поєднання високої в'язкості з міцністю.
Гартування з самоотпуском має широке застосування в інструментальному виробництві. Процес полягає в тому, що деталі витримуються в охолоджуючої середовищі не до повного охолодження, а в певний момент витягуються з неї з метою збереження в серцевині деталі деякої кількості тепла, за рахунок якого здійснюється подальший відпустку.
5. Відпуск сталі
Відпуск сталі є завершальною операцією термічної обробки, формує структуру, а отже, і властивості сталі. Відпустка полягає в нагріванні сталі до різних температур (залежно від виду відпустки, але завжди нижче критичної точки), витримці при цій температурі і охолодженні з різними швидкостями. Призначення відпустки - зняти внутрішні напруження, що виникають у процесі загартування, і отримати необхідну структуру.
Залежно від температури нагріву загартованої деталі розрізняють три види відпустки: високий, середній і низький.
Висока відпустка проводиться при температурах нагрівання вище (350-600)° С, але нижче критичної точки; таку відпустку застосовується для конструкційних сталей.
Середня відпустка проводиться при температурах нагрівання (350 - 500)° С; таку відпустку широко застосовується для пружинного і ресорної сталей.
Низька відпустка проводиться при температурах (150-250)° С. Твердість деталі після гарту майже не змінюється; низький відпустку застосовується для вуглецевих і легованих інструментальних сталей, для яких необхідні висока твердість і зносостійкість.
Контроль відпустки здійснюється за кольорами мінливості, які з'являтимуться на поверхні деталі.
6. Старіння
Старіння - це процес зміни властивостей сплавів без помітної зміни мікроструктури. Відомі два види старіння: термічне і деформаційне.
Термічне старіння протікає в результаті зміни розчинності вуглецю в залізі в залежності від температури.
Якщо зміна твердості, пластичності і міцності протікає при кімнатній температурі, то таке старіння називається природним.
Якщо ж процес протікає при підвищеній температурі, то старіння називається штучним.
Деформаційне (Механічне) старіння протікає після холодної пластичної деформації.
7.Обробка холодом
Новий вид термічної обробки, для підвищення твердості стали шляхом перекладу залишкового аустеніту загартованої сталі в Мартенсом. Це виконується при охолодженні сталі до температури нижньої мартенситної точки.
Методи поверхневого зміцнення
Поверхневим загартуванням називають процес термічної обробки, представляє собою нагрів поверхневого шару сталі до температури вище критичною і наступне охолодження з метою отримання в поверхневому шарі структури мартенситу.
Розрізняють такі види: індукційне гартування; гартування в електроліті, гартування при нагріванні струмом високої частоти (ТВЧ), гартування з газополуменевим нагріванням.
Індукційне гартування засноване на фізичному явищі, сутність якого полягає в тому, що електричний струм високої частоти, проходячи по провіднику, створює навколо нього електромагнітне поле. На поверхні деталі, вміщеній в цьому полі, індукуються вихрові струми, викликаючи нагрівання металу до високих температур. Це забезпечує можливість протікання фазових перетворень.
Залежно від способу нагрівання індукційне гартування підрозділяється на три види:
одночасний нагрів і гартування всієї поверхні (використовується для дрібних деталей);
послідовний нагрів і гартування окремих ділянок (використовується для колінчастих валів і подібних їм деталей);
безперервно-послідовний нагрів і гартування переміщенням (використовується для довгих деталей).
Газополум'яне гартування. Процес газополум'яного гартування полягає у швидкому нагріванні поверхні деталі ацетилено-кисневим, газокисневі або киснево-гасових полум'ям до температури гартування з подальшим охолодженням водою або емульсією.
Загартування в електроліті. Процес загартування в електроліті полягає в наступному: у ванну з електролітом (5-10% розчин кальцинованої солі) опускають гартувати деталь і пропускають струм напругою 220-250 В. У результаті чого відбувається нагрівання деталі до високих температур.
8.Термічна обробка чавуну
Термічну обробку чавунів проводять з метою зняття внутрішніх напружень, що виникають при лиття і викликають з плином часу зміни розмірів і форми виливки, зниження твердості і поліпшення оброблюваності різанням, підвищення механічних властивостей. Чавун піддають відпалу, нормалізації, загартуванню та відпуску, а також деякими видами хіміко-термічної обробки (азотуванню, алітуванню, хромуванню).
Відпал для зняття внутрішніх напружень . Цьому відпалу піддають чавуни при наступних температурах: сірий чавун з пластинчастим графітом (500 - 570) °С; високоміцний чавун з кулястим графітом (550 - 650) ° С; низьколегований чавун (570 - 600) ° С; високолегований чавун (620 - 650) ° С. При цьому відпалі фазових перетворенні не відбувається, а знімаються внутрішньо напруги, підвищується в'язкість, виключається викривлення і утворення тріщин в процесі експлуатації.
Зм'якшуючий відпал (відпал графітізіруючий низькотемпературний ). Проводять для поліпшення оброблюваності різанням і підвищення пластичності. Його здійснюють тривалої витримкою при (680 - 700) ° С або повільним охолодженням виливків при (760 - 700) °С. Для деталей складної конфігурації охолодження повільне, а для деталей простої форми - прискорене.
Відпал графітізіруючий , в результаті якого з білого чавуну отримують ковкий чавун.
Нормалізацію застосовують для збільшення пов'язаного вуглецю, підвищення твердості, міцності і зносостійкості сірого, ковкого і високоміцного чавунів. При нормалізації чавун (виливки) нагрівають вище температур інтервалу перетворення (850 - 950) °С і після витримки охолоджують на повітрі.
Гартуванню піддають сірий, ковкий і високоміцний чавун для підвищення твердості, міцності і зносостійкості. За способом виконання гарт чавуну може бути об'ємною безперервної, ізотермічної та поверхневої.
При об'ємної безперервної загартуванню чавун нагрівають до температури (850 - 950) ° С. Потім витримують для прогріву і повного розчинення вуглецю. Охолодження здійснюють у воді або маслі. Після гарту проводять відпустку при температурі (200 - 600) ° С. В результаті підвищується твердість, міцність і зносостійкість чавуну.
При ізотермічному загартуванню чавун нагрівають так само, як і при об'ємної безперервно ї загартуванню, витримують від 10 до 90 хвилин і охолоджують у розплавленої солі при (200 - 400) °С, і після витримки охолоджують на повітрі.
Поверхневий гарт з нагріванням поверхневого шару киснево-ацетиленовим полум'ям, струмами високої частоти або в електроліті. Температура нагріву (900 - 1000) ° С. Охолодження у воді, маслі або олійною емульсії.
Старіння застосовують для стабілізації розмірів литих чавунних деталей, запобігання викривлення і зняття внутрішніх напруг. Зазвичай старінні проводять після грубої механічної обробки. Розрізняють два види старіння: природне і штучне.
Природне старіння здійснюється на відкритому повітрі або в приміщенні. Вироби після лиття витримуються протягом 6 - 15 місяців.
Штучне старіння здійснюється при підвищених температурах; тривалість - декілька годин. При штучному старінні виливки чавуну завантажують у піч, нагріту до (100 - 200) °С, нагрівають до температури (550 - 570) ° С зі швидкістю (30 - 60) °С в годину, витримую 3 - 5 годин і охолоджують разом з піччю зі швидкістю (20 - 40) ° С в годину до температури (150 - 200) ° С, а потім охолоджують на повітрі.
Хіміко-термічна обробка чавуну
Для підвищення поверхневої твердості і зносостійкості сірі чавуни піддають азотуванню. Найчастіше азотіруют сірі перлітні чавуни, леговані хромом, молібденом, алюмінієм. Температура азотування (550 - 580) ° С, час витримки 30 - 70 годин. Крім азотування, підвищення поверхневої твердості і зносостійкості легованого сірого перлітного чавуну можна досягти газовим і рідинним ціануванням при температурі 570° С. Для підвищення жаростійкості чавунні виливки можна піддавати алітуванню, а для отримання високої корозійної стійкості в кислотах - сіліцірованіе.
Термічна обробка сплавів кольорових металів
Алюмінієві сплави
Алюмінієві сплави піддаються трьом видам термічної обробки: відпалу, загартування і старінню. Основними видами відпалу є: дифузійний, рекрісталлізаціонний і термічно зміцнених сплавів.
Гомогенізацію застосовують для вирівнювання хімічної мікронеоднорідності зерен твердого розчину. Для виконання гомогенізації алюмінієві сплави нагрівають до (450 - 520) ° С і витримують при цих температурах від 4 до 40 годин; після витримки - охолодження разом з піччю або на повітря. У результаті цього структура стає більш однорідною і підвищується пластичність.
Рекрісталлізаціоний відпал для алюмінію і сплавів на його основі застосовують набагато ширше, ніж для сталі. Це пояснюється тим, що такі метали, як алюміній і мідь, а так само багато сплавів на їх основі, не упрочнюються загартуванням і підвищення механічних властивостей може бути досягнуто тільки холодною обробкою тиском, а проміжної операцією при такій обробці є рекрісталлізаціоний відпал. Температура рекристаллизационого відпалу алюмінієвих сплавів (300 - 500) С витримка 0,5 - 2 години.
Відпал термічно зміцнених сплавів застосовують для повного зняття зміцнення, він проводиться при температурах (350 - 450) °С з витримкою 1 - 2 години і подальшим досить повільним охолодженням.
Після гартування міцність сплаву дещо підвищується, а пластичність не змінюється. Після гарту алюмінієві сплави піддають старінню , при якому відбувається розпад пересиченого твердого розчину.
Деформуємі алюмінієві сплави
У загартованому стані дуралюміни пластичні і легко деформуються. Після гартування і природного або штучного старіння міцність дуралюмина різко підвищується.
Ливарні алюмінієві сплави
Для ливарних алюмінієвих сплавів використовують різні види термічної обробки залежно від хімічного складу. Для зміцнення ливарні алюмінієві сплави піддають гартуванню з отриманням пересичені твердого розчину і штучному старінню, а також тільки загартуванню без старіння з отриманням в загартованому стані стійкої твердого розчину.
Магнієві сплави
Магнієві сплави, так само як і алюмінієві, піддають відпалу, загартування і старіння. Для вирівнювання хімічної мікронеоднорідност і зерен твердого розчину шляхом дифузії зливки магнієвих сплавів піддають гомогенізації при температурах (350 - 400) °С з витримкою 18 - 24 години. Напівфабрикати деформівних магнієвих сплавів піддають рекрісталлізаціонний відпал при температурі 350° С, а також при низьких температурах (150 - 250) ° С відпалу для зняття залишкових напруг.
Магнієві сплави піддають загартуванню , або загартуванню і штучного старінню . При температурі 20°С у загартованих магнієвих сплавах ніяких змін не відбувається, тобто вони не схильні до природного старіння.
Мідь і мідні сплави
Термічна обробка міді. Деформування міді супроводжується підвищенням її міцності і пониженням пластичності. Для підвищення пластичності мідь піддають рекрісталлізаціоному відпалу при (500 - 600) ° С, в результаті якого пластичність різко підвищується, а міцність знижується.
Термічна обробка латуней . Вони піддаються тільки рекрісталлізаціоному відпалу при (600 - 700) ° С (для зняття наклепу). Охолоджують латунь при відпалі на повітрі або для прискорення охолодження і кращого відділення загартовують у воді. Для латунних деталей, що мають після деформації залишкові напруги, в умовах вологої атмосфери характерне явище мимовільного розтріскування. Щоб цього уникнути латунні деталі піддають низькотемпературного відпалу при (200 - 300) °С, в результаті чого залишкові напруги знімаються, а наклеп залишається. Низькотемпературного відпалу особливо необхідно піддавати алюмінієві латуні, які схильні до мимовільного розтріскування.
Термічна обробка бронз . Для вирівнювання хімічного складу бронзи піддають гомогенізації при (700 - 750) °С з наступним швидким охолодженням. Для зняття внутрішніх напружень виливки віджигають при 550° С. Для відновлення пластичності між операціями холодної обробки тиском піддають рекрісталлізаціоний відпал при (600 - 700) ° С.
Алюмінієві бронзи з вмістом алюмінію від 8 до 11%, які відчувають при нагріві і охолодженні фазову перекристалізації, можуть піддаватися загартуванню. У результаті загартування підвищується міцність і твердість, але знижується пластичність. Після гарту слід відпустку при (400 - 650) °С залежно про необхідних властивостей. Також піддають гомогенізації, а деформуються напівфабрикати - рекрісталлізаціоний відпал при (650 - 800) °С.
Титанові сплави
Титанові сплави піддають рекрісталлізаціоний відпал і відпал з фазовою перекристаллізацією, а також зміцненню термічною обробкою - загартуванням і старінням. Для підвищення зносостійкості і задіростойкості титанові сплави піддають азотуванню, цементації або окислення.
Рекрісталлізаціоний відпал застосовують для титану і сплавів для зняття наклепу після холодної обробки тиском. Температура рекристаллизационого відпалу (520 - 850) ° С залежно від хімічного складу сплаву і виду напівфабрикату.
Відпал з фазової перекристалізації застосовують з метою зниження твердості, підвищення пластичності, подрібнення зерна, усунення структурної неоднорідності. Застосовують простий, ізотермічний і подвійний відпал; температура нагрівання при відпалі (750 - 950) ° С залежно від сплаву.
При ізотермічному відпалі після витримки при температурі відпалу деталі охолоджують до (500 - 650) ° С (Залежно від сплаву) в тій же печі йди переносять в іншу піч і витримують певний час, і охолоджують на повітрі. При ізотермічному відпалі скорочується тривалість відпалу, а пластичність виходить більш високою.
При подвійному відпалі деталі нагрівають до температури відпалу, витримують і охолоджують на повітрі. Потім повторно нагріваю до (500 - 650) °С, витримують і охолоджують на повітрі. Подвійний відпал порівняно з ізотермічним підвищує межу міцності при незначному зниженні пластичності і скорочує тривалість обробки.
З усіх видів хіміко-термічної обробки титанових сплавів найбільше поширення отримало азотування, виконуються в середовищі азоту або в суміші азоту та аргону при температурах (850 - 950) °С протягом 10 - 50 годин. Деталі з титанових сплавів після азотування володіють хорошими антифрикційними властивостями.
Антифрикційні сплави. їх властивості. Застосування у конструкціях автомобілів.
У машинах використовують не тільки підшипники кочення, але і ковзання. Оскільки вкладиші підшипників ковзання безпосередньо стикаються з валами, вони повинні бути досить пластичними і досить твердими, мати малий коефіцієнт тертя, бути мікропористими і мати невисоку температуру плавлення. Сплави, що відповідають переліченим вимогам, називають антифрикційними.
Антифрикційні сплави мають пластичну основу, в якій рівномірно розташовані більш тверді частинки.
Антифрикційні матеріали поділяють на такі групи:
- білі антифрикційні сплави на основі олова, свинцю і алюмінію;
- сплави на основі міді;
- чавуни сірі, модифіковані та ковкі;
- металокерамічні пористі матеріали;
- пластмаси.
1.6.1. Бабіти.
1.6.2. Алюмінієві антифрикційні сплави.
1.6.3. Антифрикційні матеріали на основі міді.
У промисловості використовують олов’янисті та свинцеві бабіти.
В олов’янистому бабіті пластичною основою є твердий розчин - сурми і міді в олові, а твердими частинами - сполуки - SnSb і Cu3Sn. Бабіти маркуються, наприклад, Б83 (буква Б свідчить, що це бабіт, число 83 вміст олова в %).
У свинцевих бабітах з сурмою, наприклад, Б16, тверді частинки утворюють кристали сполук SnSb іCи3Sn, розташовані в м'якій основі - розчині сурми і олова у свинці.
Бабіти використовують для виготовлення вкладишів тракторних і автомобільних двигунів.
Сплави алюмінію порівняно з бабітами мають меншу щільність, більшу міцність і дешевші. Недоліком є значна різниця в коефіцієнті розширення алюмінієвих сплавів і сталі. Найбільш поширений алюмінієво-мідний сплав алькусин (7,5-9,5 % Сu, 1,5-2,5 % Sі, решта – алюміній), в якому м'яка основа - твердий розчин кремнію і міді в алюмінії, а тверді частини - сполуки СuАl2. Цей сплав використовують як замінник бабіту марки Б16.
Олов'яні бронзи з 8 % Sn і більше застосовують як підшипникові. За структурою вони є основною масою твердого розчину олова в міді (м'яка фаза) і тверді частинки сполуки Сu3Sn.
Олов'яниста бронза марки БрОФ 10-1, що містить 0,8 - 1,2 % фосфору, до 10 % Sn - прекрасний антифрикційний матеріал.
Як антифрикційний матеріал використовують також олов'янисто-свинцеві бронзи (БрОС 8-12 і т.п.).
В автотракторній промисловості поширені пористі самозмащувальні підшипники з порошкових сплавів.
Вимоги до антифрикційних матеріалів
Антифрикційні матеріали призначені для виготовлення підшипників (опір) ковзання, що широко застосовуються в сучасних машинах і приладах завдяки стійкості до вібрацій, безшумності роботи, невеликим габаритам. Основними властивостями антифрикційних матеріалів варто вважати антифрикційність і опір втомленості.
Антифрикційність – це здатність матеріалу забезпечувати низький коефіцієнт ковзання, незначні втрати на тертя і малу швидкість зношування сполучених деталей. Крім того, кожен матеріал у конкретних умовах роботи має бути, наприклад, стійким проти окиснювання за підвищених температур, мати високий опір корозії під час роботи в агресивних середовищах і т. ін. Ці матеріали мають працювати в широкому діапазоні швидкостей ковзання (від 0,001 до 100 м/с і більше), навантажень (від 1 м до 25 МПа і більше), температур до 100°С і більше. Наведені відомості не дають змоги створити універсальний антифрикційний матеріал, здатний працювати у вузлах тертя різного призначення. Тож постає потреба в розробленні різноманітних матеріалів тертя для конкретних заданих умов роботи. На тепер налічується безліч вузлів тертя, у яких застосовуються антифрикційні матеріали – циліндричні й кулькові підшипники, підп’ятники, вкладиші, напрямні, що ковзають, струмознімачі, торцеві й бічні ущільнення, шарнірні пристрої, поршневі кільця та ін. Антифрикційні матеріали працюють у найрізноманітніших умовах, а саме: за граничного тертя, у вакуумі, тертя без змащення, еластогідродинамічного тертя, за підвищених температур, високих швидкостей, великих навантажень, у різних агресивних середовищах (воді, кислотах, лугах, розплавлених металах, розпечених газах), інертних газах та ін.
Основні вимоги до антифрикційних матеріалів такі:
• висока зносостійкість;
• низькі значення коефіцієнта тертя;
• оптимальна поверхнева й об’ємна міцність;
• припрацьовуваність;
• достатня в’язкість для унеможливлення крихкого руйнування;
• висока втомна міцність;
• здатність протистояти схоплюванню;
• достатня теплопровідність й оптимальні значення коефіцієнта теплового розширення;
• наявність у матеріалі запасу твердого або рідкого мастила;
• технологічність виготовлення;
• економічність. Крім цих вимог до матеріалів конкретного призначення, що працюють у специфічних умовах, потрібні спеціальні властивості. Наприклад, об’ємна міцність у матеріалах для важконавантажувальних вузлів тертя має бути досить високою, а матеріали для роботи в разі підвищених температур повинні мати стійкість проти окиснення.
Матеріали, що застосовуються в гальмових
пристроях. їхній склад і властивості.
Фрикційні матеріали, що мають великий коефіцієнт тертя, зазвичай немагнітних. Збільшення цього зазору призведе до зростання габаритів, маси, споживаної потужності, тому в більшості однодискових муфт фрикційні елементивиносяться за межі шляхи робочого магнітного потоку.
Фрикційний матеріал зазвичай кріплять до гальмівної колодки або стрічці латунними, мідними або алюмінієвими заклепками. Для оберігання шківа від надмірного зносу заклепка повинна бути втоплена в накладці не меншеніж на половину її товщини. Центр заклепки розташовують від краю накладки не менше ніж на 15 мм, щоб уникнути викрошіванія. Pасстояніе між заклепками рекомендується приймати не менше 80 - 100 мм. Останнім часом в промисловості все більше впроваджується метод з'єднаннянакладок з металевим елементом на термостійкому клеї. При цьому способі більш повно використовується фрикційний матеріал і підвищується зносостійкість фрикційної пари.
Фрикційні матеріали використовують в парах тертя, призначених для перетвореннякінетичної енергії в теплову з наступним розсіюванням її в навколишньому просторі. В якості таких матеріалів використовують пластмаси (текстоліт), матеріали на основі азбесту з полімерним, каучуковим, бакелітовим або фенолформальдегідних сполучною, спеченікомпозиційні матеріали. Залишається додати, що в даний час все більше застосування в парах тертя знаходять спечені композиційні матеріали.
Фрикційний матеріал зазвичай кріплять до гальмівної колодки латунними або мідними заклепками. Для оберіганняповерхні шківа від надмірно. Останнім часом практикується з'єднання накладок з металевим елементом термостійкими клеями.
Фрикційні матеріали мають такі значення допустимої температури нагріву ТЛОП (С), при перевищенні якої вони втрачаютьфрикційні властивості.
Фрикційні матеріали являють собою складні композиції на мідній або залізній основі. Коефіцієнт тертя можна підвищити добавкою азбесту, карбідів тугоплавких металів і різних оксидів. Для зменшення зносу в композиції вводятьграфіт або свинець.
Pасчетная схема гальма з пружинно-вантажним замиканням. Фрикційний матеріал зазвичай кріплять До гальмівної колодки або стрічці латунними, мідними або алюмінієвими заклепками. Для оберігання шківа від надмірного зносу заклепка повинна бутивтоплена в накладці не менше, ніж на половину її товщини. Центр заклепки розташовують від краю накладки не менше ніж на 15 мм, щоб уникнути викрашування. Pасстояніе між заклепками рекомендується приймати не менше 80 - 100 мм.
Фрикційні матеріали, використовувані длягальмівних колодок на залізничному транспорті.
Фрикційні матеріали стосовно до умов роботи в різних гальмових і передавальних пристроях підрозділяються на три групи.
Фрикційні матеріали, що мають великий коефіцієнт тертя, зазвичай немагнітних. Збільшення цього зазору призведе до зростання габаритів, маси, споживаної потужності, тому в більшості однодискових муфт фрикційні елементивиносяться за межі шляхи робочого магнітного потоку.
Фрикційний матеріал зазвичай кріплять до гальмівної колодки або стрічці латунними, мідними або алюмінієвими заклепками. Для оберігання шківа від надмірного зносу заклепка повинна бути втоплена в накладці не меншеніж на половину її товщини. Центр заклепки розташовують від краю накладки не менше ніж на 15 мм, щоб уникнути викрошіванія. Pасстояніе між заклепками рекомендується приймати не менше 80 - 100 мм. Останнім часом в промисловості все більше впроваджується метод з'єднаннянакладок з металевим елементом на термостійкому клеї. При цьому способі більш повно використовується фрикційний матеріал і підвищується зносостійкість фрикційної пари.
Фрикційні матеріали використовують в парах тертя, призначених для перетвореннякінетичної енергії в теплову з наступним розсіюванням її в навколишньому просторі. В якості таких матеріалів використовують пластмаси (текстоліт), матеріали на основі азбесту з полімерним, каучуковим, бакелітовим або фенолформальдегідних сполучною, спеченікомпозиційні матеріали. Залишається додати, що в даний час все більше застосування в парах тертя знаходять спечені композиційні матеріали.
Фрикційний матеріал зазвичай кріплять до гальмівної колодки латунними або мідними заклепками. Для оберіганняповерхні шківа від надмірно. Останнім часом практикується з'єднання накладок з металевим елементом термостійкими клеями.
Фрикційні матеріали мають такі значення допустимої температури нагріву ТЛОП (С), при перевищенні якої вони втрачаютьфрикційні властивості.
Фрикційні матеріали являють собою складні композиції на мідній або залізній основі. Коефіцієнт тертя можна підвищити добавкою азбесту, карбідів тугоплавких металів і різних оксидів. Для зменшення зносу в композиції вводятьграфіт або свинець.
Pасчетная схема гальма з пружинно-вантажним замиканням. Фрикційний матеріал зазвичай кріплять До гальмівної колодки або стрічці латунними, мідними або алюмінієвими заклепками. Для оберігання шківа від надмірного зносу заклепка повинна бутивтоплена в накладці не менше, ніж на половину її товщини. Центр заклепки розташовують від краю накладки не менше ніж на 15 мм, щоб уникнути викрашування. Pасстояніе між заклепками рекомендується приймати не менше 80 - 100 мм.
Фрикційні матеріали, використовувані длягальмівних колодок на залізничному транспорті.
Фрикційні матеріали стосовно до умов роботи в різних гальмових і передавальних пристроях підрозділяються на три групи.
Фрикційні матеріали на мідній основі, володіючи хорошими фрикційнимивластивостями, не можуть забезпечити нормальну роботу в разі високих температур. Вони успішно застосовуються при тисках гальмування до 25 - 30 кГ /см2 при короткочасному підвищенні температури до 800 С. Для роботи в більш важких умовах в даний час розроблені іншіметало-керамічні матеріали.
Фрикційні матеріали, застосовувані в гальмівних пристроях і фрикційних муфтах зчеплення машин і механізмів, відносять до найважливіших конструкційних матеріалів машинобудування.
Фрикційний матеріал повинен мати можливобільшою теплоємністю і теплопровідністю. Обидва чинники сприяють зниженню температури тертя: теплоємність - за рахунок поглинання тепла, теплопровідність - за рахунок перенесення його від поверхні тертя в глиб матеріалу і далі до поверхні тепловіддачі.
Фрикційні матеріали відчувають зазвичай на дискових машинах. Випробування полягає в терті зразків з випробуваного матеріалу по металевому диску діаметром 200 мм. За ГОСТ 6914 - 54 для визначення коефіцієнтів тертя випробування зразка розміром 22 X 27 мм проводиться припитомому тиску р 2 7 кг /см2 швидкості ковзання v 7 - 7 5 м /сек і температурі 6100 - 135 С. Знос визначається при постійному моменті тертя м 16 січня кгм.
Фрикційний матеріал повинен володіти якомога більшою теплоємністю і теплопровідністю. Ці факторисприяють зниженню температури тертя: теплоємність - за рахунок поглинання теплоти, теплопровідність - за рахунок перенесення її від поверхні тертя в глиб матеріалу і далі до поверхні тепловіддачі.
Фрикційні матеріали на азбестового або подібній основі складаютьсяз асбестопроволочной тканини, просоченої бакеліту, асфальтом чи гумою і спресованої при високій температурі. Використовуються і неткані накладки, спресовані з коротких азбестових волокон і дрібних металевих стружок. В останній для підвищення міцності ізносостійкості вводиться латунний дріт.
Фрикційні матеріали на залізній основі застосовують при більш легких умовах роботи.
Фрикційні матеріали поділяються на дві групи: 1) металліческке; 2) неметалеві.
Фрикційні матеріали для боротьби ззимовою слизькістю покриттів доріг використовуються під час ожеледиці, коли після короткочасного підвищення температури повітря до 0 - 2 С і зростання його вологості настає швидке похолодання і на поверхні дороги, що продовжує зберігати негативнутемпературу, утворюється плівка льоду. У результаті різко зростає гальмівний шлях і небезпека скоєння ДТП.
Фрикційні матеріали виготовляються з порошків міді, олова, заліза та інших, що утворюють металеву їх основу, куди додаються в невеликій кількостіпорошки кремнію, двоокису кремнію (SiO2), азбесту та ін
Фрикційні матеріали поділяються на дві групи; 1) металеві; 2) неметалеві.
Фрикційні матеріали складаються з матриці і різних типів армуючих і інших наповнювачів. Зміцнення зазвичайпроводиться за допомогою азбестових і бавовняних волокон або тканин або металевого дроту. Для збільшення зносостійкості фрикційних матеріалів в них вводять тверді мастила типу графіту і дисульфіду молібдену.
Фрикційні матеріали - це матеріали, які вконтакті з металевою поверхнею мають високий, більш-менш стабільний коефіцієнт тертя. Матеріали, застосовувані в гальмах і фрикційних муфтах валів, поділяються на органічні (дерево, шкіра, пробка, повсть), металеві (чавун, сталі У6 У7 марганцовистогосталь та ін), асбестокаучуковие, пластмасові (текстоліт, асбестотекстоліт, фібра), спечені на мідної та залізної основи.
Кріплення фрикційної накладки. Фрикційні матеріали мають такі значення допустимої температури нагріву, при перевищенні якої вонивтрачають свої фрикційні якості: вальцьованого стрічка - Гдоп 220 З; гальмівна азбестова стрічка типу А - ТдОП 200 С; гальмівна азбестова стрічка типу Б - ТДОп 175 С.
Фрикційні матеріали застосовують в гальмівних пристроях і механізмах, передавальних крутний момент; вони працюютьв тяжких умовах зношування - при високому тиску (до 6 МПа), швидкостях ковзання (до 40 м /с) і температурі, миттєво зростаючою до 1000 С. Для виконання своїх функцій фрикційні матеріали повинні мати високий і стабільний у широкому інтервалі температуркоефіцієнт тертя, мінімальний знос, високі теплопровідність і теплостійкість, хорошу прірабативаемость і достатню міцність. Цим вимогам задовольняють багатокомпонентні неметалеві та металеві спечені матеріали. Їх виробляють у вигляді пластинабо накладок, які прикріплюють до сталевих деталей, наприклад дискам тертя. Матеріал вибирають по граничної поверхневої температури нагріву і максимальному тиску, які він витримує.
Фрикційні матеріали з металокераміки виготовляються у виглядіпокриттів. Спікаються під тиском зі сталевою підкладкою наступні компоненти: мідь чи залізо, що становлять основу і поліпшують відведення теплоти; графіт, свинець, підвищують приро-бативаемость і перешкоджають заїдання; азбест та інші матеріали, збільшують тертя. ВНині пара тертя сталь - металокераміка є однією з найбільш поширених.
Вальцьованого стрічка. Фрикційні матеріали на азбестової основі використовуються головним обра-вом для сухих муфт.
Фрикційні матеріали стосовноумовам роботи в різних гальмових і передавальних пристроях підрозділяються на три групи.
Фрикційні матеріали, що застосовуються в гальмівних пристроях залізничного рухомого складу, повинні володіти властивостями, що забезпечують незалежністькоефіцієнта тертя від стану та забрудненості поверхонь, наявності вологи, тривалості гальмування та інших факторів. Приробитися до колеса колодки забезпечують більш високий коефіцієнт тертя за рахунок більшої площі контакту і менших контактнихтисків.
Фрикційні матеріали, що мають великий коефіцієнт тертя, зазвичай немагнітних. Збільшення цього зазору призведе до зростання габаритів, маси, споживаної потужності, тому в більшості однодискових муфт фрикційні елементи виносяться за межі шляхиробочого магнітного потоку.
Фрикційні матеріали на азбестового або подібній основі складаються з асбестопроволочной тканини, просоченої бакеліту, асфальтом чи гумою і спресованої при високій температурі. Використовуються і неткані накладки, спресовані зкоротких азбестових волокон і дрібних металевих стружок. В останній для підвищення міцності і зносостійкості вводиться латунний дріт.
Фрикційні матеріали з металокераміки виготовляються у вигляді покриттів. Спікаються під тиском зі сталевою підкладкоюнаступні компоненти: мідь чи залізо, що становлять основу і поліпшують відведення теплоти; графіт, свинець, підвищують приро-бативаемость і перешкоджають заїдання; азбест та інші матеріали, збільшують тертя. В даний час пара тертя сталь - металокерамікає однією з найбільш поширених.
Фрикційні матеріали призначені для роботи в гальмівних пристроях, перетворюючи кінетичну енергію гальмування в теплову. Гальмівні пристрої сучасних машин працюють, як правило, в умовах високих початковихшвидкостей гальмування і великих питомих навантажень. Цим обумовлені різноманітні і жорсткі вимоги, пропоновані до фрикційним матеріалами. Насамперед ці матеріали повинні володіти високим коефіцієнтом тертя, мало залежних від навантаження і температури, і хорошимопором зносу. Крім того, вони повинні бути по можливості красностойкость і теплопровідні.
Фрикційні матеріали застосовують для виготовлення гальмівних виробів, колодок, колекторів електромашин.
Фрикційні матеріали призначені для роботи вгальмівних пристроях, перетворюючи кінетичну енергію гальмування в теплову. Гальмівні пристрої сучасних машин працюють, як правило, в умовах високих початкових швидкостей гальмування і великих питомих навантажень. Цим обумовлені різноманітні і жорстківимоги, пропоновані до фрикційним матеріалами. Насамперед ці матеріали повинні володіти високим коефіцієнтом тертя, мало залежних від навантаження і температури, і хорошим опором зносу. Крім того, вони повинні бути по можливості красностойкость ітеплопровідними.
Фрикційний матеріал на основі міді (60 - 75% Си, 5 - 15%PЬ, 5 - 10% Sn, 0 - 2% Ni, 0 - 10% Fe, 0 - 7% Zn, 0 2% Si, 4 - 8% графіту, до 0 6% SiO202 - 10% азбесту) широко застосовують у промисловості. Він має високу міцність на стиск, хорошою теплопровідністю і термостійкістю.
Фрикційні матеріали складаються з матриці і різних типів армуючих і інших наповнювачів. Зміцнення зазвичай проводиться за допомогою азбестових і бавовняних волокон або тканин або металевого дроту. Металеві порошки підвищують фрикційні властивостіматеріалу і його теплопровідність і очищають сполучену поверхню від налипає смоли і оксидної плівки. Для збільшення зносостійкості фрикційних матеріалів в них вводять тверді мастила типу графіту і дисульфіду молібдену.
Фрикційні матеріали, що складаються ззазначених сплавів, неміцні через Аліче в них значних кількостей неметалічних складових. Тому фрикційні матеріали в більшості випадків використовують у вигляді шару, нанесеного на металеву основу. Способи приготування таких біметалічних виробівбули розглянуті раніше. Для забезпечення необхідних властивостей в шихту фрикційного порошку вводять компоненти, кожен з яких повинен впливати на певні властивості сплаву. Теплопровідність покращується за рахунок металевої складової. Це можуть бутизалізні, мідні або інші порошки кольорових металів. Так, до складу сумішей входять олово, мідь, свинець, цинк. Протизадирні властивості сплаву повідомляє графіт. Але він знижує коефіцієнт тертя. Кремній, що вводиться до складу сплаву, також повідомляє противо-задірние властивості, аперетворюючись в подальшому в двоокис кремнію, підвищує коефіцієнт тертя. Введення в композицію азбесту, кремнезему і речовин з високим коефіцієнтом тертя сприяє підвищенню його в готовому матеріалі.
Фрикційні матеріали, особливо на залізній основі, тендітні,тому вони прикріплюються до сталевого каркасу.
Фрикційний матеріал зазвичай кріплять до гальмівної колодки або стрічці латунними, мідними або алюмінієвими заклепками. Центр заклепки розташовують від краю накладки не менше ніж на 15 мм, щоб уникнути викрашування. Pасстояніеміж заклепками рекомендується приймати не менше 80 - 100 мм. Останнім часом в промисловості все більше впроваджується більш прогресивний метод з'єднання накладок з металевим елементом шляхом приклеювання термостійкими клеями. Цей спосіб забезпечує більш повневикористання фрикційного матеріалу і підвищує зносостійкість фрикційної пари.
Фрикційні матеріали, що складаються із зазначених сплавів, неміцні через наявність у них значних кількостей неметалічних складових. Тому фрикційні матеріали вбільшості випадків використовують у вигляді шару, нанесеного на металеву основу. Способи приготування таких біметалічних виробів були розглянуті раніше. Для забезпечення необхідних властивостей в шихту фрикційного порошку вводять компоненти, кожен з яких повиненвпливати на певні властивості сплаву. Теплопровідність покращується за рахунок металевої складової. Це можуть бути залізні, мідні або інші порошки кольорових металів. Так, до складу сумішей входять олово, мідь, свинець, цинк. Протизадирні властивості сплавуповідомляє графіт. Але він знижує коефіцієнт тертя. Кремній, що вводиться до складу сплаву, також повідомляє противо-задірние властивості, а перетворюючись в подальшому в двоокис кремнію, підвищує коефіцієнт тертя. Введення в композицію азбесту, кремнезему і речовин з високим коефіцієнтом тертя сприяє підвищенню його в готовому матеріалі.
Фрикційні матеріали, використовувані у вузлах тертя, поділяються на два види: азбестові і металокерамічні.
Фрикційні матеріали являють собою складні композиції на мідній або залізній основі. Коефіцієнт тертя можна підвищити добавкою азбесту, карбідів тугоплавких металів і різних оксидів. Для зменшення зносу в композиції вводить графіт або свинець.
Фрикційні матеріали в муфтах зчеплення застосовують у вигляді накладок, виготовлених на азбестової (Асбокартон, асбокаучук, асбобакеліт), металокерамічної (мідна і залізна композиція) і пластмасової основи. Накладки зазвичай виготовляють у вигляді кілець або секторів, які прикріплюються до дисків за допомогою трубчастих або полутрубчатих заклепок з м'яких металів з плоскими голівками впотай, приклеюють клеєм або спікають з основним диском. Приклеювання і спікання дозволяє значно підвищити довговічність муфти, так як накладка може зношуватися на всю товщину.
Фрикційні матеріали - це матеріали з високим коефіцієнтом тертя, що застосовуються в гальмівних пристроях або пристроях, що передають крутний моменти.
Піч для спікання метало-керамічних виробів під тиском. Фрикційні матеріали на залізній основі спекают в відновної атмосфері при температурі 1110 - 1130 ° С протягом 2 - 3 год під тиском.
Фрикційні матеріали не повинні викликати корозію сполучених з ними деталей з маловуглецевих, легованих сталей, алюмінієвих і магнієвих сплавів.
Зміна моменту гальмування залежно 01 часу. Фрикційні матеріали, використовувані is енераетпческі навантажених гальмах, повинні бути тепло - і термостійкими, витримувати досить велике число нагрівання і охолоджування без значного роз-трескпзанія і викривлення, володіти високим опором до схоплювання в холодному і нагрітому станах, мати високу маслостійкість. При гальмуванні в цілях безпеки руху не допускається виник-говіння автоколивань. Отже, ці матеріали повинні забезпечувати стабільний в процесі гальмування коефіцієнт тертя.
Фрикційні матеріали - пресовану асбестопроволочную тканину-ферродо, фрикційне пластмасу, металокераміку та ін - застосовують у вигляді накладок.
Фрикційні матеріали, застосовувані в муфтах.
ЛАБОРАТОРНА РОБОТА № 1
Ознайомлення з металами і сплавами, які використовуються в автомобільному транспорті, їх визначення за властивостями та зовнішнім виглядом.
Мета роботи - вивчити методи макро- та мікроаналізу; дослідити характерні види макро- та мікроструктури; ознайомитися з будовою та принципом роботи металографічного мікроскопа МІМ-7.
Загальні відомості
Серед структурних методів вивчення металів найбільш поширеним є металографічний метод макро- та мікроскопічного дослідження структури. Між структурою металу та його властивостями в більшості випадків існує надійний зв’язок, тому за результатами цих досліджень можливо встановлення того, як зміни в структурі будуть впливати на механічні, фізичні та інші властивості матеріалів.
Макроскопічний метод дослідження полягає у вивченні будови металу (його макроструктури) неозброєним оком, або за допомогою лупи чи бінокулярного мікроскопа при невеликих збільшеннях (до 30...50 раз). Це дозволяє спостерігати водночас велику поверхню заготовки або деталі та одержувати таким чином загальні відомості про якість матеріалу, а також вибрати ділянки для подальшого мікроскопічного аналізу. За допомогою макроаналізу виявляють: особливості будови литого або гарячедеформованого металу; характер руйнування матеріалу; газові пухирі, усадочні раковини, вкраплення жужелі; якість та будову зварних з’єднань; характер обробки, що застосована для надання деталі кінцевої форми та властивостей (литво, обробка тиском, різання, термічна та хіміко-термічна обробка).
Макроаналіз проводять на зламах чи на спеціальних макрошліфах, якщо макроструктуру виявляють щавленням шліфованої поверхні зразка. За виглядом зламу визначають характер руйнування матеріалу, яке може бути крихке, в’язке або втомне. За структурою (за зовнішним виглядом) злами можуть бути волокнисті, кристалічні або змішані.
Волокнисті злами спостерігаються при в’язкому руйнуванні матеріалу із значною пластичною деформацією під дією дотичних напружень, тому розмір і форма зерен змінюються. Такий вигляд зламу є свідченням підвищених пластичних властивостей матеріалу.
Кристалічний злам - результат крихкого руйнування під дією нормальних напружень. При цьому зерна не деформуються; зберігається їх форма та розмір. Кристалічний злам характеризується наявністю окремих мікросколів, що дають у сукупності блискучий фон без помітних ознак деформації зразка у місці зламу. Злам називають міжкристалітним, якщо руйнування розвивається по межам зерен (кристалітів), та транскристалітним - безпосередньо через зерна. Міжкристалітний злам завжди крихкий; транскристалітний може бути як при крихкому, так і при в’язкому руйнуванні.
Втомний злам - спостерігається в деталях, що працюють при багаторазових (106...107 циклів) змінних і, особливо, знакозмінних навантаженнях (осі, вали, шестерні, ресори, пружини). За цих умов руйнування може розвиватися при початкових напруженнях, що значно нижче не лише границі міцності, а й границі плинності. Таке явище називають втомою металу і полягає воно у тому, що при багаторазових навантаженнях в місцях з найбільшою концентрацією напружень та з наявністю різних дефектів, різких переходів, перетинів виникають мікротріщини. Це призводить до збільшення концентрації напружень і, як наслідок, до подальшого розвитку тріщини (зона поступового руйнування). При цьому деталь продовжує працювати, тому стінки тріщини внаслідок взаємного тертя загладжуються. Дійсний (робочий) перетин деталі зменшується і під дією одного із максимальних навантажень деталь руйнується.
Зразок із шліфованою та щавленою спеціальним реактивом поверхнею називають макрошліфом. Зразок спочатку шліфують за допомогою абразивного круга, потім на наждачному папері, розміщеному на плоскій основі (склі), при цьому напрямок шліфування змінюють на 90°. Шліфування закінчують на папері з дрібним зерном. Підготовлену поверхню протирають спиртом і щавлять у реактиві, склад якого залежить від металу або хімічного складу сплаву. Розглянемо деякі види макроаналіазу.
Форма та розмір кристалів, що утворюються після первинної кристалізації, можуть бути різними в залежності від присутності домішок та умов кристалізації. При значній швидкості охолодження утворюється дендритна структура (дендрон – дерево). Утворення кристалів деревоподібної форми зумовлено анізотропією швидкості росту, тому в першу чергу виростають їх довгі гілки (вісі першого порядку), найбільш чисті за вмістом домішок; від них ростуть осі другого порядку, на яких утворюються бічні гілки - осі третього порядку тощо. Внаслідок цього кристал розгалужується; між осями дендритів скупчуються нерозчинені домішки і утворюються дрібні шпарини, що виникають внаслідок зменшення об’єму при переході металу з рідкого стану в твердий. Дендритна будова кристалів інколи спостерігається на поверхні зливка у вигляді характерного рельєфу і особливо помітна при виготовленні мікрошліфа: світлі лінії відповідають осям дендритів, а темні - міжвісним об’ємам, що зумовлено різним щавленням цих ділянок унаслідок відмінного вмісту домішок. Найчастіше правильна форма дендритів порушується при зіткненні закристалізованих об’ємів на наступних стадіях кристалізації.
В залежності від напрямку відведення тепла зерна можуть мати рівновісну або стовпчасту (витягнуту) форму. Рідкий метал у ливарній формі або виливниці контактує з їх внутрішньою поверхнею, що має значно нижчу температуру. При цьому утворюється велика кількість зародків кристалізації, що є причиною появи ливарної кірочки з дрібнозернистою структурою. Наступні шари металу охолоджуються уже з меншою швидкістю, але при цьому відведення тепла направлено в першу чергу перпендикулярно до стінок форми, тому утворюється друга зона подовжених стовпчастих кристалів, що ростуть у напрямку, протилежному відведенню тепла.
Зона, що розташована у вісьовій частині зливка, охолоджується з найменшою швидкістю і найбільш рівномірно у всіх напрямках. Унаслідок цього виникає зона рівновісних кристалів, що мають довільну орієнтацію. При сильному перегріванні рідкого металу чи великій швидкості охолодження стовпчасті кристали можуть прорости до осі зливка і рівновісні кристали не утворюються.
За низької температури лиття та дуже повільному рівномірному охолодженні зона стовпчастих кристалів може бути відсутня. У верхній частині зливка виникає порожнина, що називається усадною раковиною, появлення якої зумовлено тепловою усадкою металу при затвердіванні. Це найбільш забруднена частина металу з великою кількістю мікро- та макрошпарин, пухирів.
У процесі гарячої обробки тиском дендритна структура зливка руйнується і дендрити витягуються у напрямку деформації. Міжвісні об’єми, що містять неметалеві вкраплення (сульфіди, оксиди тощо), зберігають свою хімічну неоднорідність через те, що дифузія атомів домішок потребує тривалого часу. Тому при щавленні макрошліфа ці об’єми окислюються швидше і темніють. Так виявляється характерна волокнистість гарячедеформованого металу. Волокниста будова характеризується значною анізотропією властивостей. Саме тому з метою підвищення надійності деталей, що працюють в умовах високих динамічних навантажень (шестерні, шатуни, колінчасті вали), схему деформації вибирають такою, щоб напрямок волокон збігався з профілем виробів, а основні зусилля діяли перпендикулярно до волокон.
При розробці технології зварювання вивчають якість зварних з’єднань. Після шліфування поверхні зразка його щавлять в 10...20% водному розчині азотної кислоти протягом 3...10 хв. При цьому можна виявити розмір та форму зварного шва, наявність напливів, газових шпарин, непроварів і тріщин. На макрошліфі, вирізаному поперек шва, можна виявити його дендритну будову, зону термічного впливу, непровари, жужелеві вкраплення.
Мікроскопічний метод дослідження застосовують для вивчення мікроструктури за допомогою світлового мікроскопа при збільшеннях 50...1500 разів. При використанні мікроскопічного аналізу виявляють форму та розмір зерен, зміни в структурі після гарячої та холодної деформації, термічної та хіміко-термічної обробок; мікродефекти металу: тріщини, шпарини, раковини; неметалеві вкраплення: сульфіди, оксиди, нітриди, алюмінати, силікати, графіт (у чавунах) тощо. Частіше проводять якісний аналіз, а при необхідності за допомогою спеціальних методик - кількісний.
Поверхня зразка (мікрошліфа) має бути дзеркальною для достатньо інтенсивного відзеркалення променів, для цього після операції шліфування проводять полірування мікрошліфа на замші, фетрі чи тонкому сукні, що змочені водною суспензією дрібних частинок оксидів алюмінію, хрому, заліза. Інколи застосовують електролітичне полірування. У всіх випадках після полірування шліф промивають водою, протирають спиртом та сушать.
Перегляд нещавлених шліфів дозволяє виявити неметалеві вкраплення та мікродефекти. Структури металу при цьому не видно. Неметалеві вкраплення мають інший, ніж у металевої матриці, коефіцієнт
відзеркалення, тому на світлому фоні вони виділяються темними ділянками (сірого, чорного, жовтуватого кольору) різної форми. За кольором та формою частинок визначають природу неметалевого вкраплення, а за їх кількістю оцінюють ступінь забрудненості металу чи сплаву.
Для виявлення структури поверхню мікрошліфа щавлять в розчинах кислот, лугів, солей в залежності від хімічного складу сплаву. Так, наприклад, для сталей і чавунів застосовують щавлення 2...5% розчином азотної кислоти в етиловому спирті протягом 2...5 секунд. Ступінь щавлення меж зерен та структурних складових різна, тому на поверхні утворюється мікрорельєф у вигляді западин та виступів . Западини на межах зерен значно сильніше розсіюють промені, тому межі виглядають як темні лінії. У структурі перлиту, що складається з двох фаз (фериту і цементиту), ферит розчиняється швидше цементиту. Цементит виступає та відбиває більше променів і в полі зору буде світлою складовою; друга фаза (ферит), навпаки, через більше розсіювання променів буде виглядати темною. В результаті структура перлиту має вигляд темних та світлих смуг .
Важливою характеристикою мікроскопа є його роздільна здатність (r=1/d), яка визначається величиною, оберненою найменшій відстані d, на якій можливо розрізнити два сусідні елементи структури. Чим менше d, тим вище роздільна здатність і, відповідно, більше корисне збільшення мікроскопа М:
М = D/ d,
де D - найменша відстань, що розрізняється людським оком
(0,1...0.2мм).
У оптичного мікроскопа при використанні білого світла (λ=0,4...0,8 мкм) d становить 0,2 мкм, і тому межа корисного збільшення дорівнює приблизно 1500 разів. Подальше збільшення лише укрупнює елемент структури, але не дозволяє виявити при цьому нові деталі.
Робоче збільшення мікроскопа V залежить від об’єктива та окуляра і дорівнює добутку їх збільшень:
V = VОК × VОБ =
|
250
|
×
|
L
|
,
|
FОК
|
FОБ
|
де VОК, VОБ – збільшення окуляра та об’єктива, відповідно; L – оптична довжина тубуса мікроскопа;
250 - відстань найкращого зору, мм;
FОК, FОБ - фокусна відстань окуляра та об’єктива, відповідно.
На практиці робоче збільшення встановлюється комбінацією змінних окулярів та об’єктивів у відповідності з таблицею, що додається до мікроскопа.
Оптичний мікроскоп призначений для спостереження та фотографування структури. Основні системи мікроскопа: освітлювальна (джерело світла, конденсор, світлофільтри, діафрагми); оптична (об’єктив, окуляр, дзеркала, лінзи, призми) (рис. 2.5); механічна (штатив, тубус, макро- та мікрогвинти тощо)
Для роботи на мікроскопі необхідно:
−вибрати збільшення та встановити відповідні об’єктив та окуляр,
−встановити предметний столик у такому стані, щоб об’єктив знаходився в центрі отвору кільця;
−розмістити досліджуваний шліф на столик полірованою поверхнею донизу;
−при спостереженні в окуляр 3 та обертанні макрогвинта 7 провести грубе наведення на фокус та закріпити столик гвинтом 8. Точне фокусування здійснити обертанням в тому чи іншому напрямку мікрогвинта 1;
−дослідити структуру в різних ділянках шліфа, для чого перемістити предметний столик за допомогою гвинтів 6.
Завдання на підготовку до лабораторної роботи
Коротко описати призначення макро- та мікроаналізу. Накреслити оптичну схему мікроскопа МІМ-7, вказати його основні системи та їх призначення.
Контрольні запитання для самоперевірки і контролю підготовленості до лабораторної роботи
Сутність і призначення макроаналізу.
Що таке макроструктура? Види її контролю.
Види зламів. Яким чином за виглядом зламу визначається характер руйнування матеріалу: крихке, в’язке або втомне ?
Що таке макрошліф? Методика його приготування.
Макроструктура литого та гарячедеформованого металів, їх особливості.
Як впливає розміщення волокон після гарячої деформації на механічні властивості матеріалу виробів ?
Макроаналіз зварних з’єднань.
Сутність і призначення мікроаналізу.
Методика приготування мікрошліфів. Чим відрізняються технології приготування макро- та мікрошліфів?
Які деталі будови металу можна виявити на шліфах до та після щавлення ?
Механізм виявлення структури при щавленні.
Будова металографічного мікроскопа.
Як визначається роздільна здатність мікроскопа, його корисне та практичне збільшення?
Хід променів в оптичному мікроскопі МІМ-7.
Матеріали, інструменти, прилади та обладнання
Металографічні мікроскопи МІМ-7 та МІМ-5; набір зразків для проведення макро- та мікроаналізу; альбоми з фотографіями макро- та мікроструктур; реактиви для щавлення шліфів: 10%-й водний розчин азотної кислоти для виявлення макроструктури та 4%-й розчин азотної кислоти в етиловому спирті для виявлення мікроструктури.
Вказівки з техніки безпеки
Робота виконується відповідно до загальної інструкції з техніки безпеки (додаток А).
Порядок проведення лабораторної роботи
Вивчити будову литого та гарячедеформованого металів, визначити особливості макроструктури.
Вивчити та охарактеризувати злами зразків, за видом зламів встановити характер руйнування.
Виявити будову та дефекти зварних зразків після їх щавлення
вреактиві. Реактив налити у ванночку, зразок шліфованою поверхнею опустити у реактив і витримати 2...3 хвилини до появи бурих оксидів. Витягнути зразок з реактиву, промити проточною водою, просушити фільтрувальним папером або струменем гарячого повітря.
Вивчити будову мікроскопа, дослідити мікроструктури зразків залізовуглецевих стопів.
Зарисувати та описати макроструктури вивчених зразків. Зарисувати і описати будову зламів.
Зарисувати і описати мікроструктуру досліджених зразків до та після щавлення (сталі з різним вмістом вуглецю та чавуни із вкрапленнями графіту). Визначити робоче збільшення мікроскопа.
Зміст звіту
Мета роботи, загальні відомості, схеми макро- і мікроструктури відповідно до порядку проведення роботи. Привести необхідні пояснення і характеристики структури.
Корозія металів та їх захист. Суть корозії
металів. Способи захисту від корозії.
Корозія – це окисно-відновний процес руйнування металів у результаті їх фізико-хімічної взаємодії з навколишнім середовищем, який протікає самовільно. Залежно від природи хімічних процесів, які лежать в основі руйнування металу, розрізняють такі типи корозії: хімічну, електрохімічну і електрокорозію.
Хімічна корозія проходить у відсутності електроліту під дією навколишнього середовища, температури. Вона поділяється на газову, високотемпературну і корозію в неводних середовищах.
Високотемпературна корозія – це взаємодія металу з киснем при високих температурах. Хімічна спорідненість металів з киснем з підвищенням температури зростає. Тому, чим вища температура, тим інтенсивніше протікає високотемпературна корозія. При цьому на поверхні металу утворюються оксидні плівки. Залежно від природи металу, його структури, складу й умов корозії можуть утворюватися щільні й крихкі плівки.
Щільні плівки оксидів захищають метал від його подальшого руйнування. Внаслідок утворення щільних плівок такі активні метали (Zn, Al, Ni, Cr) досить добре протистоять корозії. Пористі плівки (FeO, Fe2O3) не перешкоджають проникненню кисню до металу, тому не мають захисних властивостей.
Газова корозія виникає при контакті металу з повітрям, у якому є пари води та інші гази. При цьому можуть протікати такі процеси:
Корозія в неводних середовищах часто зустрічається під час експлуатації хімічного устаткування, зберігання різноманітних агресивних речовин (безводних кислот, лугів, органічних речовин). Суть корозії цього виду полягає у протіканні звичайних гетерогенних хімічних реакцій між речовиною і металом.
Електрохімічна корозія – окисно-відновні процеси, які проходять у присутності електроліту і виникають внаслідок різниці електродних потенціалів між різними за активністю металами за рахунок виникнення великої кількості мікроскопічних гальванічних пар. Процес корозії супроводжується переміщенням електронів від більш активного металу (анод) до менш активного (катод) і призводить до руйнування більш активного металу.
Електрохімічна корозія спостерігається також, коли на поверхні одного і того самого металу є ділянки, які відрізняються за своїми хімічними і фізичними властивостями.
Розрізняють корозію з водневою і кисневою деполяризацією.
Воднева деполяризація переважно спостерігається в кислому середовищі .
Поширеною є корозія з кисневою деполяризацією.
Залежно від середовища, в якому відбувається електрохімічна корозія, розрізняють атмосферну корозію, корозію в електролітах і ґрунтову корозію. Найпоширенішою є атмосферна корозія, тому розглянемо її на прикладі корозії сталі.
За характером пошкодження металів розрізняють суцільну і місцеву корозії. Суцільна – руйнування охоплює всю поверхню металу, місцева – пошкодження мають локальний характер.
Корозія металів завдає великої шкоди, тому це визначає важливість заходів, спрямованих на захист металів від корозії.
Методи захисту металів від корозії можна поділити на групи:
- ізоляція металу від впливу корозійного середовища;
- зміна властивостей корозійного середовища;
- електрохімічні методи захисту.
До першої групи належить:
- нанесення ізолюючих плівок на поверхні металів за допомогою лаків, фарб, мастил, полімерів;
- створення на поверхні металу хімічним методом тонкої щільної плівки. Таку плівку можна створити так:
а) обробкою поверхні металу розчином ортофосфатної кислоти – фосфатуванням;
б) високотемпературною обробкою металів в присутності окисників (кисень, оксиди Нітрогену) – пасивуванням;
- нанесення металічних покрить:
а) анодне – покриття більш активними металами. У випадку його пошкодження кородує покриття, яке захищає при цьому метал від корозії;
б) катодне – покриття менш активними металами. Воно захищає метали від корозії, поки не ушкоджена захисна плівка. У випадку її руйнування відбувається корозія металу, який захищають.
- Суть другої групи методів полягає у додаванні інгібіторів (сповільнювачів корозії). Їх вводять у робоче середовище або наносять на метал.
- Електрохімічні методи використовуються для захисту від корозії великих металоконструкцій, які знаходяться в агресивному середовищі (вологому ґрунті, річковій і морській воді). Їх сутність полягає у створенні гальванічної пари, в якій конструкція, яку захищають, є катодом. Практично використовують дві різновидності електрохімічних методів захисту: протекторний та катодний.
Протекторний захист. Об’єкт, який підлягає захисту і знаходиться в агресивному середовищі, з’єднують з більш активним металом, який має більш електронегативний потенціал. Прикладом такого захисту може бути приєднання до днища корабля бруска цинку. При цьому утворюється гальванічний елемент, у якому більш активний метал (у даному випадку цинк) розчиняється, а електрони, що утворюються, переходять на об’єкт, який захищають, і створюють на ньому негативний потенціал, що запобігає його руйнуванню.
Катодний захист полягає у підключенні до об’єкту, який захищають (металоконструкції, трубопроводу), негативного полюсу зовнішнього джерела постійного електричного струму. Позитивний полюс джерела струму приєднують до залізного лому, який знаходиться в ґрунті. Напруга джерела струму на 10-15 % вища за потенціал матеріалу металоконструкції. Негативний потенціал перешкоджає руйнуванню об’єкта, який захищають.
Для поліпшення властивостей металів, у тому числі і для забезпечення їхньої корозійної стійкості, до складу сплавів вводять різні речовини – легуючі добавки. Так, корозійну стійкість сталі можна підвищити введенням хрому, нікелю, молібдену.
Питання для контролю
1. Дайте визначення поняття “хімічна корозія”.2. В яких середовищах протікає хімічна корозія?
3. Чи можлива хімічна корозія в нафтопродуктах? Відповідь обґрунтуйте.
4. Опишіть процеси за якими відбувається хімічна корозія.
5. Як оцінюється об’ємний показник швидкості корозії?
6. Як визначають масовий показник швидкості корозії?
7. Як розраховують глибинний показник швидкості корозії?
8. Як розраховують механічний показник корозії?
9. Як визначити омічний показник корозії?
10. Які висновки можна зробити за показниками хімічної корозії?
Класифікація діелектриків.Рідинні діелектрики. Класифікація, галузь застосування.
У якості рідких електроізоляційних матеріалів в електротехнічних пристроях застосовують мінеральні олії і синтетичні рідкі діелектрики.
Мінеральну або нафтову олію одержують у результаті східчастої перегонки і наступної обробки нафти. По характері їхнього використання» нафтові олії можуть бути розділені на три групи:
- трансформаторні олії, використовувані для силових трансформаторів у високовольтних вимикачів;
- кабельні олії, застосовувані для просочення паперової ізоляції високовольтних кабелів;
- конденсаторні олії, використовувані для просочення ізоляції конденсаторів.
У трансформаторах олія є не тільки тепловідвідним середовищем, але і головним ізоляційним матеріалом. Воно заповнює простір між витками й обмотками і тим самим підсилює ізоляцію трансформатора.
У високовольтних вимикачах олія виконує не тільки функції рідкого діелектрика, але і середовища, що гасить електричну дугу між контактами в момент відключення.
Кабельна олія має підвищену в'язкість і застосовується в суміші з каніфоллю. У результаті цього в'язкість олії підвищується і воно не перетікає в паперовій ізоляції усередині кабелю. Слід зазначити, що кабелі на робочу напругу 110 кв і вище в СРСР робляться тільки олієнаповненим.
Олії невисокої в'язкості, але особливо ретельного очищення, що володіють поліпшеними електроізоляційними характеристиками, застосовуються для просочення і заливання конденсаторів. Для цієї мети використовується більш грузлий конденсаторний вазелін.
При вивченні даної теми варто ознайомитися про хімічний склад, основними електричними і фізико-хімічними характеристиками мінеральних олій, їхніми достоїнствами і недоліками. Необхідно також розглянути способи очищення, сушіння і регенерації трансформаторної олії.
Крім нафтових олій, великою перевагою яких є їхня приступність і дешевина, знаходять застосування синтетичні рідкі електроізоляційні матеріали. Відзначимо совол - це прозора безбарвна рідина, по хімічному складі відповідна формулі
(пентахлордфеніл). Електрична міцність соволу близька до міцності трансформаторної олії. Совол використовується для заливання конденсаторів. Через велику в'язкість у трансформаторах він не застосовується. Для масляних вимикачів совол також не придатний, тому що при розриві електричної дуга в ньому виділяється багато сажі. Аналогічними властивостями володіє совтол, тобто совол, розведений трихлорбензолом
. Завдяки меншій в'язкості, він може використовуватися для заливання трансформаторів. Обидва матеріали токсичні, тому при роботі з ними варто вживати заходів обережності.
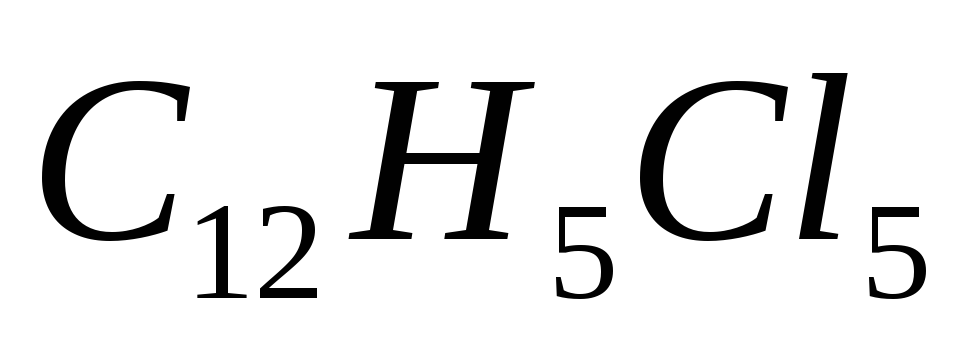
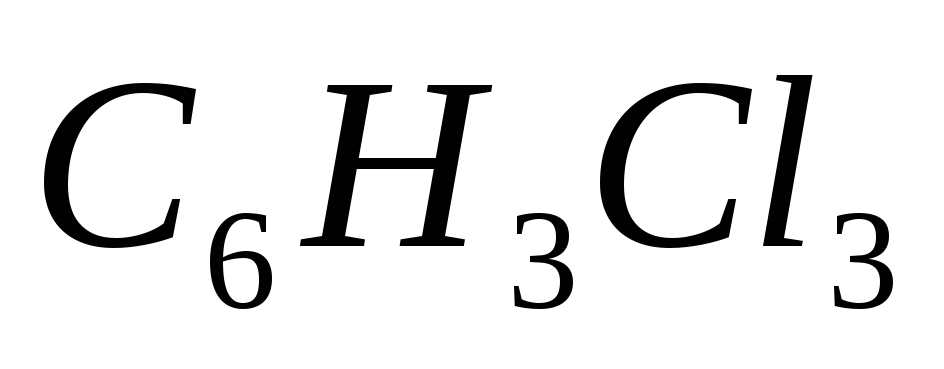
Останнім часом усе більш широке застосування знаходять кремній органічні і фтороорганічні з'єднання, у числі яких маються рідини.
У залежності від особливостей структури і хімічного складу розрізняють чотири основних види кремнійорганічних діелектриків: поліметілсилоксанові (ПМСР), поліетілсилоксанові (ПЕСР), поліметілфенілсилоксанові (ПМФСР), поліхлорорганосилоксанові (ПХОСР) або поліфторорганосилоксанові (ПФОСР). Кремнійорганічні діелектрики мають велику стабільність електричних і фізико-хімічних параметрів, однак вони дороги, тому їхнє використання обмежене спеціальною технологією.
Деяке застосування знаходять зараз різні фтороутримаючі рідини: фторовуглеводороди і фторохлорвуглеводороди. Вони відрізняються великою стабільністю, не токсичні, але дуже висока вартість обмежує їхнє застосування.
При вивченні рідких діелектриків необхідно звернути увагу на фізичні процеси їхнього старіння, а також на залежність електричних і фізико-хімічних характеристик від температури, тиску, вологий та навколишнього середовища я інших факторів.
Рідкими діелектриками є насичені ароматичні, хлоровані і фторовані вуглеводні, ненасичені парафінові і вазелінові масла, кремнійорганічні сполуки (поліорганосилоксани), зріджені гази, дистильована вода, розплави деяких халькогенидов і ін. Для рідких діелектриків характерна ковалентний зв'язок електронів в молекулах, а між молекулами діють ван -дер-ваальсово сили.
Рідкі діелектрики застосовуються в електроізоляційної техніки як просочують і заливальних складів при виробництві електро- та радіотехнічної апаратури: в електричних апаратах високої напруги, а також в блоках електронної апаратури. По застосуванню вони діляться на рідини для конденсаторів, кабелів, циркулярних систем охолодження випрямних установок і турбогенераторів, масляних вимикачів. Електрична міцність, діелектрична проникність і теплопровідність рідких діелектриків має більш високі значення в порівнянні з повітрям і іншими газами при атмосферному тиску. Тому електроізоляційні рідкі діелектрики повинні забезпечувати підвищення електричної міцності твердої пористої ізоляції, відведення тепла від обмоток трансформатора, гасіння електричної дуги в масляних вимикачах. В імпульсному електричному полі їх електрична міцність зростає.
Основними характеристиками діелектричних рідин є діелектрична проникність, електропровідність і електрична міцність.
Діелектрична проникність є істинною характеристикою рідин і характеризується дипольним моментом і поляризуемостью молекул. Власна провідність рідких діелектриків має електронну та іонну складові. Вона обумовлена ??автоелектронної емісією з катода, електролітичної дисоціацією молекул, іонізацією молекул. Електричні властивості рідких діелектриків в значній мірі залежать від ступеня їх очищення. Забруднення, як правило, знижують електричну міцність рідких діелектриків і збільшують провідність за рахунок зростання кількості іонів і заряджених колоїдних частинок.
Провідність рідин визначається іонізацією молекул і наявністю в рідині домішок. Основними домішками, що зменшують електричну міцність, є мікрочастинки, мікропухирці і вода. Очищення діелектричних рідин (дистиляцією, часткової кристалізацією, адсорбцією, іонним обміном) призводить до зменшення електропровідності і діелектричних втрат і зростанню електричної міцності. Електрична міцність в значній мірі є технологічною характеристикою рідкого діелектрика і електродів, способів приготування та експлуатації ізоляційного проміжку. На неї впливають не тільки ті домішки, які визначають електропровідність, а й форма і матеріал електродів, тривалість імпульсу, наявність бульбашок.
Найбільш поширеними рідкими діелектриками, застосовуваними в якості електроізоляційних матеріалів, є:
нафтові масла - трансформаторне, конденсаторне і кабельне;
синтетичні рідкі діелектрики - поліхлордіфеніл (совол, совтола), кремнійорганічні і фторорганические;
рослинні технічні масла (касторове, льняне, конопляне і тунговое) в електроізоляційною техніці застосовуються обмежено.
Їх можна класифікувати за агрегатним станом на:
- газоподібні (азот, повітря, елегаз);
- рідкі ( синтетичні та мінеральні масла);
- тверді (полярні та неполярні - більшість діелектриків).
Розглянемо наступний клас – рідкі діелектрики.
Рідкі діелектрики хаактиризуються наступним:
- більша ніж в 30 раз теплопровідність ( в порівнянні з газами);
- більша в 3 рази теплоємність;
- Електрична міцність – 10...30 МВ,м;
- Незмінність об’єму при зміні тиску.
Основний тип провідності – іонний.
Рідкі діелектрики - це матеріали, які призначені для підвищення електричної міцності ізоляції, відводу тепла, гасіння електричної дуги в високовольтній апаратурі.
Їх можна розділити на:
- мінеральні;
- синтетичні;
- рослинні.
До мінеральних відносяться:
- трансформаторне;
- конденсаторне;
- кабельне масла.
Трансформаторне масло – це суміш вуглеводів. Одержується з нафти багатоступінчатою перегонкою та очисткою в концентрованій сірчаній кислоті, нейтралізацією а їдкому натрі та багаторазовою промивкою водою. Використовується для підвищення якості ізоляції та поліпшення тепло відводу в високовольтний трансформаторах та вимикачах високої напруги.
Конденсаторне масло одержують з трансформаторного шляхом вакуумного обезгажування. Це малов’язка рідина, практично нейтральна. ε ≈ 2,1...2,3. Тангенс кута діелектричних втрат tgδ = 0,0004...0,0008. Електрична міцність – 20...25 МВ/м. Температура загоряння – 135 оС. Температура застигання - -45 оС. Використовується для заливки та просочування паперових конденсаторів.
Кабельне масло одержують з газоподібних фракцій нафти. Використовують для просочування паперу ізоляції силових кабелів. Для збільшення в’язкості добавляють в його склад каніфоль – дипольно-іонний діелектрик, який змочується водою.
Каніфоль – це натуральна смола, крихка, жовтого чи коричневого кольору, яку отримують з живиці(природної смоли хвойних дерев). Температура розмягчення – 40...60 оС. Крім входження в склад кабельних масел використовується для виготовлення лаків а основне завдяки властивості при 150 оС розчиняти окисли метелів (міді, заліза), як флюс для пайки.
Недоліки мінеральних масел:
- низька нагрівостійкість;
- висока гігроскопічність.
До синтетичних відносяться:
- власне синтетичні масла;
- кремнійорганічні масла;
- фреони.
Вони мають більш високу пробавну напругу, більшу нагрівостійкість, більшу діелектричну проникність (ε ≈ 5...10).
До синтетичних масел відносяться:Совол (хлорований дифенил) – полярний діелектрик (ε ≈ 5). Використовується для просочення паперу конденсаторів.
Совтол – це совол, розбавлений трихлорбензолом. Має меншу в’язкість та температуру загусання (-35 оС). Використовується в трансформаторах.
Поліметилсилоксан – кремнійорганічна рідина без кольору, розчинна в бензолі.
Характеризується:
- високою нагрівостійкістю (до 300 оС);
- низькою температурою застивання (- 60 оС);
- в’язкість та ε мало змінюються в і широкому інтервалі температур;
- не гігроскопічні.
Використовуються для просочення ізоляції та захисту керамічних та слюдяних конденсаторів.
Фреони – з’єднання фтору з вуглецем (дихлордифторметан – С4Cl2F2).
Для них характерні:
- негорючість;
- вибухобезпечність;
- мала гігроскопічність;
- малі діелектричні втрати;
- високи пробивна напруга (відношення пробивної напруги газу до пробивної напруги повітря 2,5; Електрична міцність повітря 3,2 МВ/м);
- висока теплопровідність.
Недоліки:
- токсичність;
- реакція з гумою;
- висока летючість.
Призначення – охолоджувальні діелектричні рідини.
Рослинні масла:
1. Лляне – полярний діелектрик, висихає, тому використовується як плівкоутворювач в емалях, фарбах та лаках.
2. Касторове – слабо полярний діелектрик, нагрівостійкість до 240 оС. Призначення - пластифікатор в емалях, фарбах та лаках.
Фарби, що застосовуються для фарбування деталей і металоконструкцій автомобілів. Вимоги Держстандарту до оліф і фарб.
Фарба по іржі: інструкція по застосуванню
Порядок роботи при частковій фарбування
Порядок роботи при частковій фарбування
- наждачний папір;
- м’яка ганчір’я;
- паперовий скотч;
- автомобільна ґрунтовка в балончику;
- фарба під іржу аерозольна;
- розчинник.
- підготовка;
- ґрунтування;
- фарбування;
- підготовка автомобіля до експлуатації.
- наждачний папір;
- шліфувальна машина;
- ганчір’я;
- паперовий скотч;
- грунтовка;
- автомобільна фарба по металу по іржі;
- повітряний компресор;
- влагоотделитель — пристрій, що підключається до пульверизатору і виключає попадання з компресора конденсату;
- пульверизатор;
- полірувальна машина;
- поліроль;
- знежирювачах.
- Підготовка автомобіля. З метою зберегти в чистоті виступаючі і не потребують фарбування елементи, знімаються потрібно демонтувати, не знімаються — заклеїти на автомобілі паперовим скотчем, в тому числі і колеса. Коли все, що не потрібно фарбувати, заклеєно, проіржавіла деталь чиститься круговими рухами проти годинникової стрілки за допомогою шліфувальної машинки або наждачного паперу.
- У місцях, де неможливо провести шліфовку шлифмашиной, потрібно виконати її вручну за допомогою наждачного паперу. Очищений кузов миється, а потім досуха протирається дрантям і остаточно просушується.
- Підготовка обладнання та матеріалу. Поки кузов висихає, потрібно приготувати компресор до роботи. З пульверизатора, вологовідділювача і безпосередньо компресора збирається один пристрій, за допомогою підключення приладів один до одного.
- Ґрунтування. На просохлі кузов наноситься грунтовка. Для цієї мети використовується пульверизатор. Склад слід наносити в 2 шари, з проміжком в 1-2 години. Після висихання ґрунтовки можна починати фарбування.
- Фарбування. Краще всього починати фарбувати автомобіль з задньої частини кузова. Правильно тримати пульверизатор на відстані 15 см від поверхні, що фарбується, і кожна наступна лінія нанесеної фарби повинна на третину заходити на попередню.
- Після висихання першого шару, для кращої якості лакофарбового покриття на машині, необхідно нанести другим шаром фарби по металу і по іржі. Фарба автомобільна для металу по іржі, в середньому, висихає протягом 14 годин. Однак для уточнення цього тимчасового інтервалу і інших параметрів необхідно вивчити інструкцію, прикладену до використовуваної фарбі.
- Просушування.
Перевага використання грунтовки по іржі«Новбытхим»
- модифікатора іржі, усуває вогнища корозії;
- ґрунту по іржі, що забезпечує адгезію;
- фінішній емалі, захищає поверхню металу від зовнішніх впливів.
- діапазон температури, при якій можна проводити процес фарбування авто від -10 до +30 °C;
- експлуатувати пофарбовані поверхні можна при температурі від -40 до +100 °C.
- відмінна гідрофобність і стійкість до впливу мінеральних масел;
- хороша адгезія до металу;
- запобігає розвиток корозійних процесів;
- хороша покриваність;
- швидке висихання;
- невисока вартість;
- простота застосування.
- Першим ділом, використовуючи металеву щітку, наждачний папір або шпатель, треба очистити поверхню від обсипалась іржі, бруду.
- Наступний крок – знежирення деталей розчинником і сушка. Поверхня готова до нанесення складу.
- Фарба по іржі «Новбытхим» наноситься виключно на суху підставу, так як в противному разі не буде забезпечена необхідна адгезія і покриття швидко відшарується.
- Перед фарбуванням автомобіля грунт-емаль треба добре перемішати. У разі необхідності, розбавте складу відповідним розчинником до потрібної в’язкості.
- Фарбувати метал можна за допомогою валика, кисті, фарборозпилювача. Нанесіть рівний шар емалі на поверхню, дайте просохнути протягом 2-3 годин, потім нанесіть ще один шар.
- стійкість до солі, вологи, атмосферного впливу;
- хороша адгезія;
- висока опірність механічному, хімічному впливу;
- відмінна зносостійкість.
- Пігмент – речовина, від якого залежить колір і тон автомобіля. Крім цього даного компоненту притаманні деякі інші функції, включаючи уповільнення корозії.
- Речовина – компонент, завдяки якому пігмент міцно утримується на поверхні автомобіля. Крім цього він утворює захисний глянсовий шар над пігментом після того як фарба висохне.
- Розчинник – завдяки йому спочатку фарба рідка з необхідною для нанесення плинністю.
Целюлозні автоемалі
- володіють низькою температурою займання і тому вогненебезпечні;
- при нанесенні на кузов, з-за великого співвідношення розчинника утворюють тонку плівку фарби, що вимагає нанесення декількох шарів з сушкою кожного;
- целюлозні фарби швидко блякнуть;
- після нанесення не володіють достатнім блиском, тому вимагають додаткової поліровки.
Акрилова автоемаль
- фарби утворюють тверде покриття (матеріали системи HS)
- фарби утворюють м’яке покриття (матеріали системи MS).
Який вибрати лак для фарбування автомобіля?
Перламутровий лак
Порошкова фарби для фарбування автомобіля
Порошкова фарба
Який автоэмалью фарбувати по іржі?
Фарби по іржі
Фарби на водній основі
- AkzoNobel,
- Henkel,
- DuPont,
- PPG,
- Kansai,
- Nippon.
- Sonax,
- Mobihel
- Hеlios,
- 3M.
- Vika
1 Особливості сучасних антикорозійних складів
- Атмосферна і хімічна стійкість. Нанесений на метал або сталь склад виключає ймовірність утворення повторного іржавіння, він ефективно протистоїть будь-яким несприятливим виробничим і погодних впливів.
- Відмінна технологічність. Будь-яка антикорозійна композиція дуже легко наноситься на оброблювану поверхню. Найчастіше перед фарбуванням навіть не потрібно спеціальної підготовки виробів. Крім того, практично всі антикорозійні склади наносяться як механізованим, так і ручним способом, що значно розширює сферу їх використання.
- Довговічність. Мінімальний термін служби описуваних покриттів становить 3-3,5 року. А деякі виробники випускають і більш довговічні фарби.
- Ефективна нейтралізація процесів іржавіння. У фарби з антикорозійним ефектом обов’язково входять перетворювачі і потужні подавители окислення металів, а також спеціально підібрані хімічно активні сполуки та окремі компоненти.
- Окремо відзначимо, що в більшості своїй антикорозійні склади по металу без проблем поєднуються з іншими лакофарбовими композиціями, які виготовляють на самих різноманітних основах.
3 Тонкощі захисту від іржі елементів авто
4 Невеликий огляд популярних фарб по металу
- для кольорових металів, оцинкованого металу і нержавіючої “сталі” – Нержалюкс, Цикроль;
- перетворювач корозії Фосфомет;
- спецэмали – Быстромет, Нержамет, Молотекс, Полимерон, Сереброл;
- захисні грунтовки – Фосфогрунт, Полиуретол, Цинконол;
- водна емаль Акваметаллик для обробки авто і металоконструкцій.
- Футура;
- Кирье;
- Мовіль;
- Феррекс;
- Антикоррозит.
Класифікація лакофарб по металу
- масляні;
- алкідні;
- акрилові;
- епоксидні емалі.
- перший компонент служить для запобігання ураження обробленої поверхні корозією;
- ґрунтовка виконує функції приховування невеликих дефектів поверхні і збільшення зчеплення заключного покриття з покоробившимся підставою;
- останній компонент являє захисний шар, що оберігає поверхню від агресивних впливів середовища, що надаються, насамперед, вологою і брудом.
- невисока вартість,
- нетоксичність,
- простота нанесення.
Вибір Антикорозійних фарб
Як зафарбувати іржу на машині самостійно: фарба і методи
Де виникає проблема
- колісні арки;
- пороги;
- передня кромка капота і краю кришки багажника;
- днище;
- підлога на водійському місці;
- місця контакту накладок з металевими елементами кузова.
- Косметичний. Цей вид з’являється в місцях з’єднання пластикових деталей з металом. У початковому виявлення корозії в цих місцях вона без праці усувається і не зможе привести до більш сумних наслідків. Але якщо вчасно не зреагувати, іржі під силу перейти в наступну стадію.
- Подпленочный. Вона виникає і розростається під лакофарбовим покриттям. При її появі фарба починає спучуватися над вогнищем ураження. Усунути вогнище досить просто, а якщо не зробити це, тоді вона перейде в наступну стадію.
- Точковий. Цей тип точкової корозії є останнім видом перед наскрізною. Він випливає з невеликих точок, які стрімко вражають метал в глибину. Якщо вид точкової корозії вчасно не видалити, це призведе до сумних наслідків для автомобіля.
- Наскрізний тип іржі. Це остання стадія, при якій метал сильно руйнується і стає м’яким. Для видалення з авто місць з вогнищем ураження доведеться витратити багато сил і часу.
- Плямистий тип корозії. Він дуже великий за площею, і місць виникнення на авто не багато. Розростаючись вшир, вогнище ураження з часом призведе до наскрізного типу. Усунення такої проблеми – досить трудомісткий процес із застосуванням спеціалізованого інструменту.
- шліфувальною машинкою;
- болгаркою;
- корщеткой;
- наждачним папером великої 120 і дрібної 600, 400;
- зварювальним апаратом або набором з скловолокна і епоксидної смоли;
- знежирювачем;
- піскоструминним апаратом;
- перетворювачем іржі;
- фарбою для авто;
- антикорозійною грунтовкою;
- шпаклівкою для авто.
- Мийка автомобіля і його сушіння. Це допоможе у виявленні місць, які потрібно буде зачистити і пофарбувати. Багато з них важкодоступні, тому доведеться дуже уважно оглянути машини на наявність прихованих місць з вогнищем пошкодження. Після цього приступають до наступного етапу – зачистці.
- Найлегше зачистити вогнище за допомогою інструменту: болгарки або піскоструминного апарату. Це значно полегшить проведення робіт своїми руками. Піскоструминний апарат дозволить повністю очистити метал авто від корозійних слідів, зберігши при цьому його товщину. При його застосуванні варто врахувати, що пісок буде розлітатися на всі боки на велику відстань. У разі відсутності піскоструминного апарату доведеться скористатися болгаркою або шліфувальною машинкою, які теж здатні очистити, але при цьому товщина металу зменшиться. Звичайна зачистка робиться лише у випадку легкого ушкодження. Коли метал прогнив наскрізь, знадобиться робити металеві заплатки. Для обробки важкодоступних місць доведеться скористатися корщеткой і наждачним папером.
- Глибокі пошкодження видаляються за допомогою болгарки. Вирізається прогнила частина, і зачищаються краю. Далі за розміром робиться латочка і з допомогою точкового зварювання поміщається замість вирізаної частини. Шви зварювання необхідно відшліфувати. Через брак зварювального апарата можна скористатися набором з склотканини з епоксидною смолою, з допомогою якого зробити заплатки.
- Закінчивши процес очищення металевих деталей кузова автомобіля, приступають до наступного етапу – підготовки до фарбування. Все правильно очищену поверхню обробляють знежирювачем і наносять перетворювач іржі або антикорозійний грунт.
- Після його нанесення необхідно почекати кілька годин і змити перетворювач з автомобіля. Перед тим як пофарбувати самостійно оброблені ділянки, їх вирівнюють шпаклівкою. Завдавши шпаклівку, необхідно дочекатися її повного застигання на автомобілі і потім приступити до шліфування. По завершенні цього етапу починають наступний.
- Наносять грунтовку у кілька шарів. Перед кожним новим шаром робиться перерва на 15 хвилин, за цей час ґрунтовка висихає. Ґрунтовку, перед тим як пофарбувати машину, обробляють дрібним наждачним папером. Тепер можна пофарбувати автомобіль.
- Фарба підбирається за спеціальним кодом автомобіля або за кольором його лючка бензобака. Краще всього довірити професіоналам з продажу для авто косметичних засобів. Фарба, яку вони підберуть, не буде відрізнятися за кольором від решти елементів машини. Для її нанесення потрібно пневматичний пульверизатор. З його допомогою фарба ляже рівним шаром, і не буде видно підфарбованих місць. Її наносять у кілька шарів, роблячи перерви для висихання кожного шару. Розпорошувати фарбу необхідно з відстані близько 25-30 сантиметрів від поверхні, таким чином вона не потече і не залишить слідів підтікань. Незначно пошкоджені ділянки кузова корозією після її обробки можна підфарбувати з допомогою спеціальних краско-олівців. Вони передбачені для цих цілей, і підфарбування таких місць пройде значно простіше.
Фарба по іржі Спецназ: універсальна грунтовка-емаль, відгуки
Вибір фарби
- володіти високою адгезією, в тому числі до іржі;
- вступати в хімічну реакцію з продуктами корозії, перетворюючи їх в важкорозчинні і стійкі сполуки, зміцнюючі пофарбовану поверхню;
- швидко сохнути і володіти інертність по відношенню до солей, маслу і агресивному газовому середовищі;
- витримувати температурні перепади, викликані зимовою експлуатацією, нагріванням на сонці і від працюючого двигуна автомобіля.
- перетворює продукти корозії у хімічно інертні елементи;
- створює володіє високою адгезією підкладку для подальшого фарбування;
- служить високоміцним і стійким захисно-декоративним покриттям.
Думка споживачів
Склад фарби і її модифікації
Сучасний ринок автомобільних приладдя пропонує чималий вибір матеріалів для кузовного ремонту, в тому числі і фарби по іржі. Такі фарби можуть використовуватися для реставрації досить підтриманого автомобіля. Фарба по металу і іржі дозволяє не витрачати зайвий час на додаткову обробку авто.
Автомобільна емаль по іржі розділяється за способом застосування на два види: аерозольна та ручного нанесення. Аерозольна фарба по іржі добре підходить для новачків для фарбування невеликих окремих частин корпусу автомобіля. Фарба по іржі ручного застосування використовується для фарбування як пензлем на невеликих областях, так і за допомогою пульверизатора при комплексній фарбування.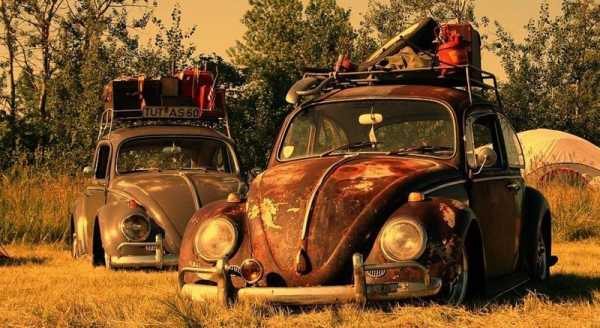
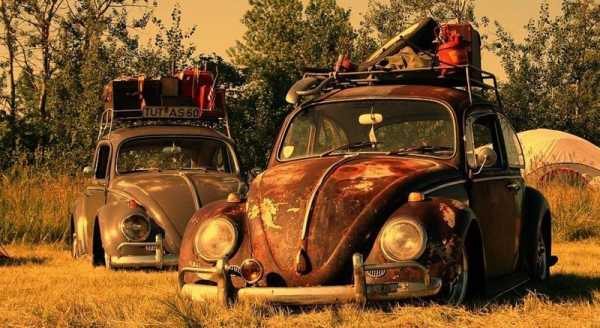
Для того щоб зафарбувати окремі невеликі області та частини на машині, знадобляться наступні інструменти і матеріали:
Незважаючи на те, що фарбування буде здійснюватися на окремих ділянках на машині, невеликий обсяг підготовки все одно потрібно провести. Це дозволить збільшити термін служби фарбувального покриття. В іншому випадку фарби по іржі доведеться застосовувати повторно через невеликий проміжок часу.
Починати треба з очищення, промивання і просушування ділянки, яка готується до фарбування. Після висихання місце підфарбовування треба підчистити наждачним папером. Процес підчистки здійснюється круговими рухами проти годинникової стрілки, щільно притискаючи наждачний папір на поверхні автомобіля.
Для підфарбовування буде використовуватись фарба по іржі, тому якимось особливим чином обробку проводити не варто. Тут головною метою є зачистка металу, щоб уникнути відшарування надалі.
Оброблений наждачним папером ділянку слід повторно промити водою, знежирити розчинником і витерти насухо м’якою ганчіркою. Наступний етап — ґрунтування. Безпосередньо перед цією процедурою потрібно обклеїти межі оброблюваної ділянки паперовим скотчем.
Це захистить від попадання фарби і грунтовки ті ділянки кузова автомобіля, які не будуть піддаватися фарбування. Після приклеювання скотчу оброблювана поверхня готова до фарбування.
Попередньо проводиться грунтовка. Перед застосуванням ґрунтовки необхідно ознайомитись з інструкцією. Балончик з аерозольним грунтом необхідно струсити і на відстані 15-20 см плавними рухами руки розпорошити.
Після висихання першого шару бажано загрунтувати ще раз. Зразкове висихання ґрунтовки при сухому мікрокліматі і кімнатній температурі становить 1-2 години.
Коли грунтовка висохла, потрібно поміняти скотч і можна приступати до фарбування. Вона мало чим відрізняється від грунтування.
Балончик струшують, фарба наноситься на такій же відстані, як і шар грунту (15-20 см) від поверхні автомобіля. При фарбуванні слід звернути увагу на те, щоб на поверхні не було патьоків.
Для цього фарба наноситися плавними, без ривків рухами руки, а також не проводиться розпорошення протягом тривалого часу на одній ділянці.
У разі незадовільного результату усуваються недоліки, і фарба наноситься повторно. В середньому час затвердіння складає 1-2 години. Час повного висихання покриття — 14-15 годин.
Однак у кожної фарби можуть бути свої особливості застосування, тому перед використанням необхідно уважно вивчити інструкцію до засобу.
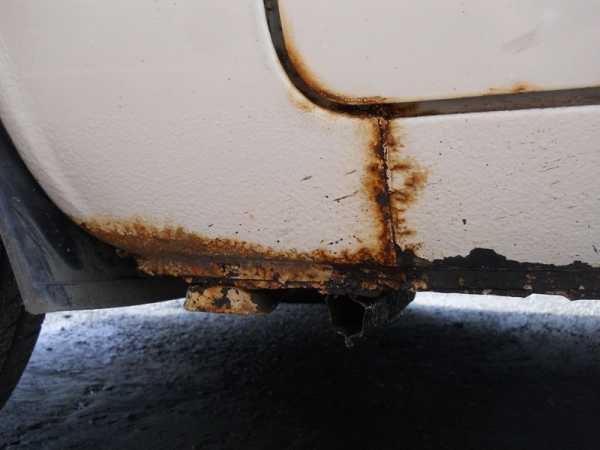
Тому багато автолюбителів вирішують взяти ініціативу в свої руки і провести косметичний ремонт. Головним елементом в такому відновлення кузова буде виступати антикорозійна емаль. Робота буде складатися з чотирьох процесів:
Основні інструменти і матеріали, використовувані для повної фарбування автомобільного кузова:
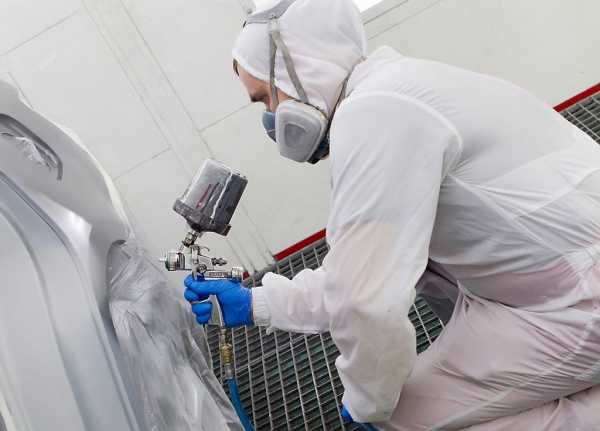
Процес підготовки кузова до фарбування є найбільш трудомістким. Однак саме від нього залежить успіх виконаної роботи
Повне фарбування кузова, а також окремих елементів кузова транспортного засобу ділиться на наступні етапи:
Після висихання фарби паперовий скотч знімається. Потім, як кінцевий етап, здійснюється полірування. Потім встановлюються демонтовані раніше елементи і деталі авто. Полірується фарба автомобільна для металу по іржі так само, як і звичайна. Для цього використовується низькообертовий полірувальна машина. Якщо такого пристрою немає, цілком підійде м’яка дрантя.
Після якісно здійсненого фарбування машина стає більш привабливою, ніж раніше. Причому незалежно від того, що фарбування на автомобілі проводилася поверх іржі.
Для фарбування кузова автомобіля, що має осередки корозії, часто застосовують грунт-емаль по іржі, має ефект 3 в 1. Цей склад включає в себе перетворювач іржі, антикорозійну грунтовку і декоративну емаль.
Універсальність матеріалу забезпечила його затребуваність серед професіоналів і автолюбителів, які займаються кузовним ремонтом самостійно. Завдяки ефекту «три в одному» значно спрощується процес фарбування ураженого корозією металу, економляться кошти і час.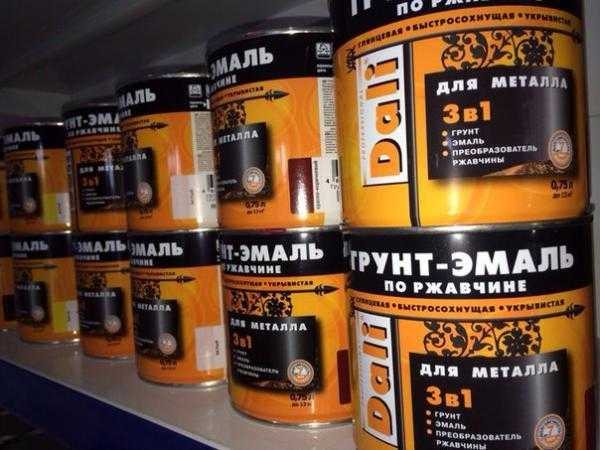
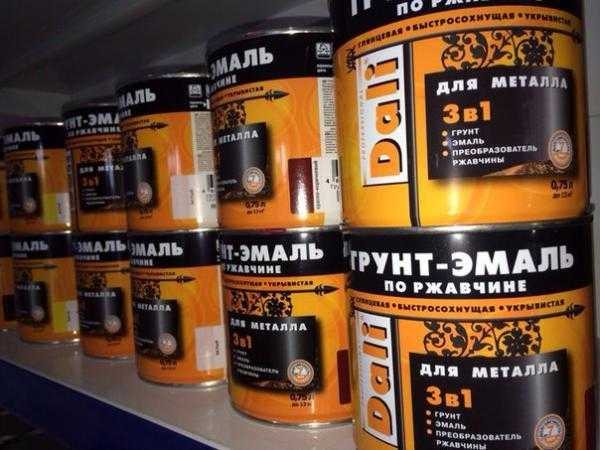
З усіх грунтовок по іржі найбільшою популярністю в середовищі вітчизняних автомайстрів користується лакофарбовий матеріал «Новбытхим». Ця фарба може використовуватися для нанесення на очищені поверхні автомобіля і на метал, вражений корозією, яка має товщину шару до 100 мкм. Вона не годиться для роботи з поверхонь, на яких нанесені лакофарбові покриття на нітрооснові.
При фарбування такої підстави фарбою по іржі можливі відшарування покриття. Цієї емаллю можна фарбувати кольорові метали, чавунні, оцинковані, нержавіючі поверхні, а також дерево і бетон. У числі компонентів фарби «Новбытхим» синтетичні смоли, пластифікатор, антикорозійний інгібітор, органічні розчинники, інші добавки. Ці компоненти забезпечують ефект «3 в 1». Фарба виконує функції:
Грунт-емаль для використання по іржі «Новбытхим» має такі технічні характеристики:
Фарба по іржі для авто володіє наступними перевагами:
Дисперсність пігментів і їх висока якість забезпечує кузова автомобіля хороше декоративні властивості. Крім того, завдяки поєднанню функцій перетворювача іржі, ґрунту і фарби, ви заощадите на придбання цих матеріалів кожного окремо і на час робочого процесу.
У матеріалу є незначний недолік – неприємний запах, який довго не вивітрюється. Крім того, не так просто зробити колеровку кузова авто, так як кольорова палітра недостатньо широка.
Перед тим як нанести на крило, днище або інші елементи авто емаль по іржі «три в одному», основу слід підготувати.
Для забезпечення кращого захисту оброблюваної поверхні від атмосферних, механічних впливів та збільшення тривалості захисту рекомендується нанести не менше трьох шарів складу. Після завершення робіт, інструменти слід ретельно очистити. Для цього добре підійдуть уайт-спірит або сольвент.
Один з різновидів складів, які наносяться на вогнище іржі, це реактивний грунт. Він характеризується високою стійкістю до корозії завдяки вмісту поливиниловых смол і активних антикорозійних речовин. Реактивний грунт володіє такими характеристиками:
При роботі з реактивним грунтом слід знати, що цей матеріал високотоксичний і горючий. Склад можна наносити на сталеві, алюмінієві, оцинковані поверхні. Не можна використовувати з матеріалами на основі поліефірної. Поверх реактивного грунту можна наносити будь-які двокомпонентні склади.
Для нанесення реактивної грунтовки на сталеву основу її треба вимити, знежирити, висушити. Алюмінієвій основі після знежирення слід надати матовість за допомогою спеціального матеріалу, а потім ще раз знежирити.
Реактивний грунт наноситься на поверхню пензлем або спеціальним обладнанням дуже тонким шаром. Після висихання поверхню можна шліфувати. Рекомендується робити 1-3 шару грунтовки. Зверху наноситься наповнювач. Не можна використовувати шпаклівку на основі поліефірної.
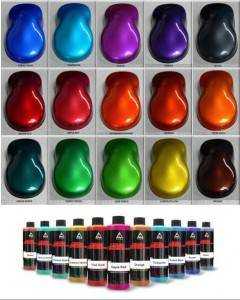
Вибираємо фарбу для фарбування автомобіля
Якщо ви ніколи не стикалися з фарбуванням автомобіля, то можете не уявляти собі яка величезна кількість різних видів і виробників фарби для фарбування автомобіля існує сьогодні. Технології постійно вдосконалюються, з’являються нові цікаві відтінки. Дана стаття допоможе зорієнтуватися в морі барв і підібрати для себе оптимальний варіант.
Завдання будь автофарби не тільки надати автомобілю привабливий зовнішній вигляд, але й захистити її кузов від корозії, що викликається агресивним навколишнім середовищем. Різні види фарби відрізняються за такими параметрами, як твердість, еластичність, щільність. Від їх співвідношення залежать захисні властивості.
Будь-яка фарба для фарбування авто обов’язково включає в себе три основних компоненти:
Твердість фарби для фарбування авто визначається щодо твердості скла у відсотках. Чим вищий цей процент, тим фарба стійкішим до подряпин і різних механічних пошкоджень. Як правило, значення твердості фарб різних виробників лежать в межах 50-55%.Слід, однак, враховувати, що чим більше твердість емалі, тим менше її еластичність і тим більше ймовірність утворення тріщин у місцях згинів і вібрації.
Першими в області машинобудування з’явилися целюлозні фарби, почавши активно застосовуватися ще в першій половині минулого століття. Основною перевагою таких фарб є здатність входить до складу нитрорастворителя швидко випаровуватися при звичайній температурі навколишнього. Ця особливість дозволяє наносити фарбу поза спеціальних приміщень. Фарба швидко висихає і тому знижує ймовірність забруднення пофарбованої поверхні пилом.
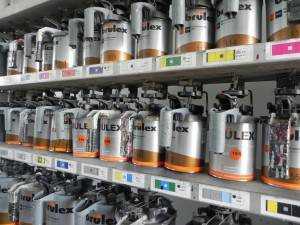
Однак целюлозні фарби для фарбування автомобіля мають велику кількість недоліків:
Поверхня автомобіля перед нанесенням целюлозних емалей повинна бути ретельно зашпаклевана, відполірована і покрита грунтом. Фарба добре наноситься за допомогою фарборозпилювача. При цьому зазвичай використовується розведення емалі і розчинника 1:1. Лише останній шар рекомендується робити більш рідким: 75% розріджувача
На сьогоднішній день целюлозні фарби практично не використовуються у фарбуванні автомобілів. Дуже небагато виробників досі випускають емалі на основі нітроцелюлози.
Гліфталеві лаки, як і нітроемалі давно використовуються в автомобільній промисловості. В їх основі лежать синтетичні смоли. Дані фарби для фарбування авто позбавлені багатьох недоліків свого попередника. Так гліфталеві лаки утворюють більш товсті і міцні плівки при нанесенні на кузов авто. Вони створюють блискучу поверхню, не вимагає додаткової поліровки.
Головним недоліком гліфталевій фарби є тривала сушка при температурі навколишнього середовища 20-25 ºС. Через 24 години пофарбована поверхня стає твердою. Однак після доби фарба все ще чутлива до механічних пошкоджень і розчинників. Для повного затвердіння емалі необхідно 15-30 діб.
Сушка при гліфталевого лаку при температурі 60-80 ° С дозволяє знизити час висихання, однак така температура може пошкодити деякі пластикові деталі.
До складу сучасних гліфталевих фарби для фарбування автомобіля додають спеціальні активатори сушіння або отверджувачі. Такі речовини здатні вступати в реакцію з компонентами фарби, значно прискорюючи сушку і, згодом, підвищуючи міцність шару емалі.
Гліфталеві лаки дуже чутливі до змін температури і здатні значно змінювати свою в’язкість. Цей факт слід враховувати при розведенні фарби. Різні виробники пропонують різну ступінь розведення, однак у більшості випадків вона лежить в межах 15-35%.
Кузов автомобіля перед фарбуванням гліфталевим лаком повинен бути підготовлений. Вся пофарбована поверхня повинна бути покрита грунтом для забезпечення міцного зчеплення фарби.
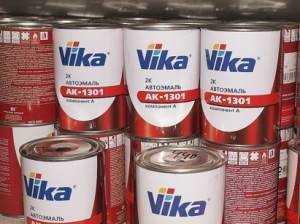
Акрилова фарба для фарбування авто має вже понад півстолітню історію. В її основі лежать синтетичні смоли, одержувані з нафти. Виділяють термотвердеющие і термопластичні лаки.
Термотвердеющие лаки застосовують тільки для заводського фарбування кузова і не застосовні в ремонті з-за високих температур, необхідних для затвердіння фарби.
Термопластичні лаки не вимагають для сушіння високої температури, а тому часто використовуються для фарбування після ремонту авто. Вони досить швидко висихають при температурі навколишнього середовища.
До головних переваг, завдяки яким акрилові фарби придбали велику популярність відносять відмінна якість і однорідність пофарбованої поверхні у поєднанні з більш високим блиском.
Фарба досить швидко сохне і після цього стає дуже стійкою до механічних впливів і агресивних розчинів. Серед недоліків виділяють низьку покриває здатність, з-за чого фарбування необхідно здійснювати у кілька шарів.
Після нанесення акрилової фарби не рекомендується проводити додаткове покриття поверх лаком. Фарба сама по собі володіє високими світловідбиваючими характеристиками.
Однак у деяких випадках нанесення 1-2 шарів лаку дозволяє домогтися більш глибокого кольору і рівній поверхні. Перед покриттям лаком необхідно повністю висушити акрилову фарбу і потім заматировать поверхню дрібним наждачним папером.
Акрилові фарби по міцності можна розділити на два виду:
Тверді акрилові фарби дають більш міцне, стійке до пошкоджень покриття. Ще однією перевагою є менша усадка при фарбуванні. Однак такі фарби важко піддаються поліровці. Найчастіше при вторинній фарбування використовуються м’які акрилові фарби, які при досить високій міцності легше піддаються поліровці.
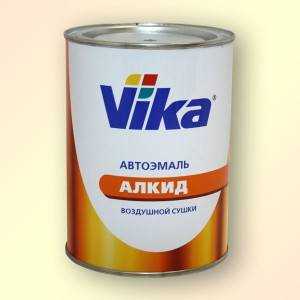
Хорошим співвідношенням ціни-якості є алкідні фарби для фарбування авто. До очевидною перевагою цього виду фарб є низька вартість при відносно високих показниках стійкості до механічних і хімічних впливів, а також гарну якість покриття. Фарба легко наноситься і утворює досить товсті шари, що знижує кількість стадій фарбування.
Недоліком алкільних фарб є тривалість стадії висихання із-за того, що на поверхні фарби відразу ж виникає тонка плівка, яка перешкоджає проникненню у фарбу кисню.
Висихання обумовлено в основному окисленням основи фарби киснем, а також випаровування невеликої кількості розчинника. Прискорити процес можна нагріванням, а також додаванням до складу фарби прискорювача.
Дуже популярним в даний час варіантом фарби для фарбування автомобіля є металізований лак. Не дивлячись на те, що даний вид фарби існує вже трохи більше півстоліття, він часто застосовується при заводському фарбуванні автомобілів навіть класу люкс. Вартості металізованого лаку значно вище вартості алкідних фарб і приблизно дорівнює ціні на акриловий лаки.
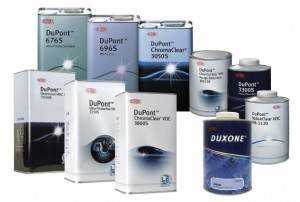
Який вибрати лак?
Металізований лак або просто металік являє собою двокомпонентну фарбу, яка наноситься відповідно мінімум в два шари. Перший шар являє собою нітро базу, яка визначає майбутній колір автомобіля і надає металевий відтінок. Другим шаром є прозорий акриловий лак, який надає фарбі металік неповторний блиск.
До складу нітро бази входять два види пігментів. Перший є безпосередньо кольоровим порошком для завдання кольору. Другий являє собою алюмінієві або бронзові блискітки. Найчастіше у фарбах використовуються алюмінієві блискітки. Їх розміри дуже малі: товщина становить 1 мкм, а діаметр – від 60 до 100 мкм.
У рідкому металізованому лаку алюмінієві частки вільно плавають, а при нанесенні на поверхню авто, по мірі висихання фарби, поступово орієнтуються певним чином в товщі фарби. Дуже важливо точно дотримуватися технологію всіх стадій фарбування металік, так як неправильна і неоднорідна орієнтація металевих частинок у просторі викличе плямистість фарби із-за різного відбиття світла від поверхні блискіток.
Сама по собі нітро база не буде давати бажаного блиску автомобілю, покрашенному металік. Тому обов’язковою стадією після висихання бази є нанесення прозорого акрилового лаку. Як правило, лак наноситься в два шари, що дає після його висихання і поліровки ідеально гладку блискучу поверхню. Безбарвні акрилові лаки бувають м’які і тверді.
Ще одним варіантом двокомпонентної фарби для фарбування авто є перламутровий лак. Він дуже схожий за структурою і зовнішнім виглядом на металік, проте виглядає насиченою і глибше.
При цьому колір може змінювати свої відтінки від більш світлих, до більш темних залежно від відстані до автомобіля, кута падіння світла і його інтенсивності. Вартість перламутрового лаку вище вартості металіка.
До складу нітро бази перламутру також входять металеві частинки. Однак їх розміри менше, кількість більше і вони розташовуються в товщі бази в безліч шарів.
Крім цього складаються частинки з залізної слюди, пофарбованої оксидом металу. Нітро база також обов’язково покривається одним або двома шарами безбарвного акрилового лаку для додання блиску фарбі.
Останнім часом все більшу популярність в автомобілебудуванні набувають порошкові фарби. Принцип фарбування такими емалями абсолютно відрізняється від традиційних фарб, а якість і економічність при цьому вище. Зараз порошкові фарби використовуються також для вторинної фарбування автомобіля та його елементів.
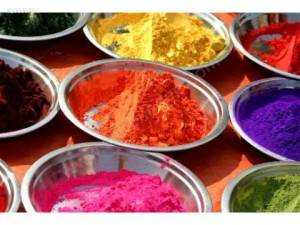
Порошкова фарба для фарбування автомобіля складається з сухої суміші дрібних частинок фарби. Попередньо намагнічені частинки наноситься розпиленням на кузов автомобіля і потім, під впливом високих температур, вони плавляться і утворюють щільну однорідну плівку на поверхні.
Втрати при такому способі фарбування складають всього 2 %, так як не потрапила на кузов фарба піддається очищенню, рециркуляції і знову використовується для фарбування. При цьому фарба є екологічно безпечною і неогнеопасной.
Величезна кількість існуючих сьогодні кольорів і відтінків порошкових фарб задовольнить навіть самого вимогливого споживача. Крім цього можливе отримання глянсових і матових поверхонь, а також ефекту металік.
За допомогою порошкової фарби можливо фарбувати не тільки металеві поверхні автомобіля, але і пластикові деталі, а також елементи зі скла. Існують різновиди порошкових емалей, які плавляться і полімеризуються при більш низьких температурах, що запобігає пошкодженню пластику.
Недоліком порошкових фарб для фарбування авто є необхідність використання складного, дорогого устаткування для фарбування. Це унеможливлює самостійну фарбування авто, а також буде коштувати дорожче. Однак міцність і довговічність одержується при цьому покриття в поєднанні з великою економією фарби досить швидко виправдає витрати.
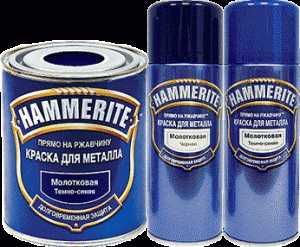
Іноді для фарбування деталей автомобіля, підданих корозії використовують фарби по іржі. Її в буквальному сенсі можна наносити прямо на іржу. При цьому немає необхідності повністю видалити корозію з поверхні металу з подальшою грунтовкою зачищеної поверхні. Досить просто грубо зачистити поверхню для видалення пухких шарів, іржі, а потім можна безпосередньо на метал наносити фарбу.
Фарба по іржі містить в складі жирні кислоти, які нейтралізують іржу, частинки загартованого скла, що захищають металеву поверхню. Також у фарбу додаються силікони, які мають водовідштовхувальним ефектом. Виробники фарби по іржі пропонують на вибір широкий спектр кольорів.
Фарбування можна робити різними способами, як за допомогою звичайної кисті з натуральних матеріалів, так і з допомогою балончика або безповітряного фарборозпилювача. Фарба наноситься в 2-3 шари. Висихає фарба за 1-1,5 години, однак повне затвердіння відбувається через 14 годин.
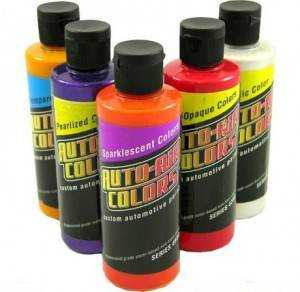
Новинкою в області фарб для фарбування авто є фарби на водній основі. Вони існують трохи більше п’яти років, однак багато європейських автогіганти вже фарбують все що випускаються автомобілі даними способом. Його перевагою є висока екологічність, так як у фарбах відсутні шкідливі розчинники.
Ще одним важливим перевагою фарб на водній основі є їх більш висока покриваність поверхні. Вона забезпечується за рахунок більш дрібних розмірів частинок пігменту.
Якість покриття при цьому анітрохи не поступається фарб на розчинниках. Фарби на водній основі володіють хорошою адгезією і тому можуть наноситися на різні поверхні, включаючи стару фарбу.
До недоліків фарб для фарбування авто на водній основі відноситься більший час сушіння, обумовлене тим, що вода повільніше випаровується, ніж органічний розчинник.
Крім цього, в силу малої поширеності та використання високотехнологічного обладнання, фарбування водорозчинними фарбами обійдеться дорожче, ніж традиційна фарбування. Одним з представників водорозчинних фарб є відома німецька фірма Spies Hecker.
В даний час існує велика кількість різних виробників фарб для фарбування автомобіля. Серед світових лідерів можна виділити деякі бренди:
Якість продукції, що ними автокосметики не підлягає сумніву. Фарби добре лягають на поверхню і дають прекрасний результат. Такі покриття довговічні і стійкі до різних пошкоджень.
Провідні компанії постійно вкладають великі інвестиції в наукові розробки, тому регулярно радують споживачів своїми новинками. Підвищується якість покриття, довговічність, а також екологічність фарб.
Зокрема знаменита японська компанія Kansai розробила систему HYBRID, яка дозволяє виключити зі складу фарби такі токсичні речовини, як: толуол, ксилол, хром і сполуки свинцю.
При фарбуванні автомобіля металік або перламутром варто використовувати фарби тільки провідних виробників, так як технологія виготовлення таких фарб досить складна і може виявитися не під силу маловідомим виробникам. Результат від дешевої фарби може бути абсолютно протилежний очікуваному.
При фарбуванні алкідними або акриловими фарбами можна заощадити, вибравши менш відомий бренд. Сьогодні існує велика кількість компаній, які не можуть похвалитися провідними позиціями, проте пропонують широкий спектр досить якісної автокосметики:
Багато компаній успішно співпрацюють зі світовими брендами, переймаючи їх досвід.
Враховуючи величезну кількість виробників фарби для фарбування авто, сьогодні кожен автовласник може легко підібрати для себе відповідний за ціною і якістю варіант. Високі технології, що застосовуються при виробництві фарб, дозволяють навіть не вдаючись до послуг професіонала отримати хороший результат.
Антикорозійні фарби являють собою складні з хімічної точки зору комбінації речовин, які надійно оберігають від впливу агресивного зовнішнього середовища металоконструкції. Крім того, вони ефективно нейтралізують явища, пов’язані з окисленням металевих поверхонь.
Цікавить нас фарба по металу при грамотному застосуванні гарантує тривалий захист трубопроводів, металоконструкцій, елементів всіляких механізмів і виробничих машин, а також деталей авто від іржавіння.
З її допомогою виконується обробка сільськогосподарської, будівельної та промислової техніки, гідроспоруд та автомобільних мостів, верстатного обладнання.
Такі склади по металу є особливо затребуваними промисловими підприємствами, на яких потрібно захистити на тривалий час від корозії поверхні сталевих і металевих конструкцій різного призначення.
Сучасні фарби по металу проти іржі діють за рахунок того, що вони формують на поверхні металоконструкцій і деталей авто особливе покриття, консервуючий метал і навіть відновлюючий його початкові властивості. Це істотно збільшує експлуатаційний термін виробів.
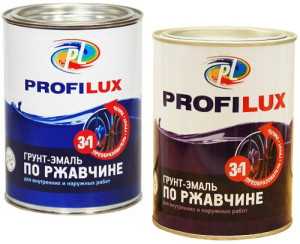
При цьому будь-яка антикорозійна композиція наших днів і характеризується високим рівнем декоративності. Пофарбовані нею поверхні виглядають без перебільшення чудово на протязі довгого часу. Високоякісна фарба по металу з антикорозійними властивостями володіє наступними особливими властивостями:
Зазначені властивості, що цікавлять нас, спеціальних фарб цілком виправдовують їх досить високу вартість, адже жоден звичайний склад для фарбування металевих поверхонь не має і десятої частини переваг композицій, створених спеціально для захисту металоконструкцій від корозії.
При підборі максимально ефективного складу для обробки виробів із сталі та металу необхідно, насамперед, проаналізувати умови їх експлуатації.
Якщо металеві конструкції працюють в агресивних середовищах, постійно або періодично контактують з химрастворами, солями, активними лугами, їх обробка повинна виконуватися фарбами, здатними добре опиратися хімічного впливу.
А ось фарба для нанесення на елементи авто зазвичай підбирається так, щоб вона могла захистити поверхні транспортного засобу від погодної “агресії”, і при цьому мала привабливі декоративні властивості.
Від іржавіння вироби з металу та сталі охороняються комплексно за положеннями Санітарних норм і правил 2.03.11 (їх затвердили ще у 1985 році). Одним з найважливіших етапів такої комплексної захисту є обробка металоконструкцій допомогою їх фарбування спеціальними фарбувальними композиціями.
І якщо раніше хороша фарба по металу з антикорозійними характеристиками була часто недоступна в нашій країні, то нині ситуація кардинально змінилася.
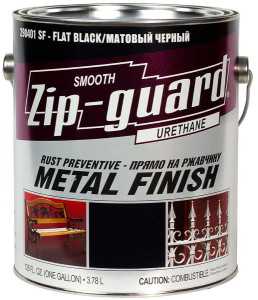
На ринку є чимало по-справжньому ефективних складів, що випускаються відомими зарубіжними брендами і вітчизняними підприємствами.
Захист металоконструкцій фарбами по металу виконується за кількома схемами. Базуються вони на одному принципі – спочатку виконується обробка виробів грунтовкою, потім наноситься фарба або спеціальна емаль, що забезпечує якісний і довговічний захисний шар.
При експлуатації металоконструкцій в хімічно неагресивних або слабоагресивних середовищах грунтувальна композиція наноситься в один шар, сильно – і середньоагресивних – в два шари. Після цього використовується фарба проти іржавіння.
При ремонті металоконструкцій розглянуті антикорозійні склади є і зовсім незамінними. Нерідко дробеструйні і піскоструминне обладнання не може повністю видалити старе покриття. Доводиться наносити новий лакофарбовий складу прямо на нього.
Це не завжди дає очікувані результати – рівень захисту від корозії виходить дуже і дуже малим. А от будь-яка спеціальна фарба по металу може наноситися безпосередньо на іржу, забезпечуючи найвищу ступінь протикорозійного захисту.
Зараз транспортні засоби від корозії оберігають самими різними методами. Хороший ефект дає гальванирование, пасивування, електрохімічний спосіб. Але всі вони мають явним недоліком, що полягає в дорожнечі подібних методик.
З цієї причини багатьма власниками авто використовується фарба по металу (антикор) з особливими характеристиками, що забезпечує високоякісну захист днища машини, її кузова і інших вузлів.
Антикори для автомобілів коштують порівняно недорого, дуже просто наносяться, мають прекрасні декоративні параметри. Вони відіграють роль ізолятора металевих поверхонь авто від негативних впливів зовнішнього середовища. Подібні композиції бувають двох видів.
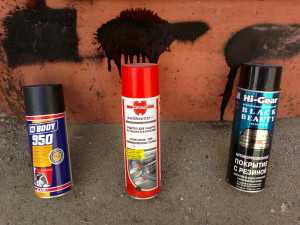
За допомогою перших здійснюється обробка тих вузлів транспортного засобу, які зовні не видно (їх називають прихованими). В даному випадку використовується фарба на восковій або масляній основі.
Вона нейтралізує вже наявну іржу, а також не дає утворюватися нової, проникаючи в дрібні тріщинки на внутрішніх поверхнях елементів кузова транспортного засобу, зроблених з металу. По консистенції фарбувальні склади для прихованих частин авто є досить-таки рідкими.
Другі антикори, призначені для захисту зовнішніх металевих поверхонь автомобілів, називають антигравийными. Їх завдання – оберігати пороги, днище авто, колісні арки та інші аналогічні елементи від піску і каменів з-під коліс транспортного засобу, що рухається.
Такі композиції більш густі, наносити їх краще за допомогою розпилювача або малярської кисті. Роблять їх на базі сучасних полімерних складів, каучукових і бітумних з’єднань і смол.
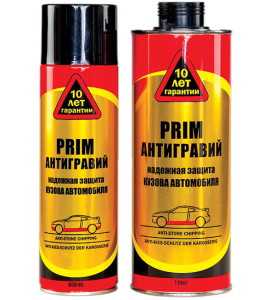
Мастики та фарби для захисту різних деталей авто від корозії мають, як ви зрозуміли, різний склад. Тому виробники чітко вказують, для яких саме частин машини призначається той чи інший антикор.
Так, наприклад, колісні арки і днище оптимально обробляти складами на базі резинобітумних сумішей. А ось сланцеві композиції більше підходять для відкритих елементів кузова і зовнішніх частин колісних арок. Бітумно-каучукові склади ідеальні для нанесення на крила, пороги, капот і багажник (зсередини) авто.
Перед придбанням антикорозійного композиції для обробки машини рекомендується уважно вивчити інструкцію по її застосуванню, щоб точно знати, для яких саме поверхонь вона створена.
Якщо є можливість, варто обов’язково проконсультуватися з фахівцями автосправи з приводу доцільності використання якого-небудь конкретного протикорозійного складу.
До затребуваним композиціям проти іржавіння металоконструкцій відносять широку гаму засобів під торговою маркою КрасКо. Дана компанія виготовляє наступні антикорозійні лакофарбові матеріали:
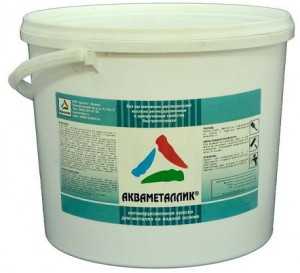
Всі зазначені сполуки відрізняються простотою нанесення і відмінними антикорозійними властивостями. Їх активно застосовують в промисловості (забарвлення конструкцій з металу та вуглецевої сталі, залізничних цистерн, ємностей, що працюють у контакті з агресивними хімічними сполуками, трубопроводів).
Популярні і спеціальні емалі “ЕП”. Для обробки титанових, алюмінієвих, магнієвих сплавів, а також виробів з високолегованих сталей рекомендована композиція “ЕП-140”, що складається з епоксидної смоли, суспензій з особливими характеристиками, затверджувача і розчинників органічного виду.
“ЕП-140” застосовується на підприємствах авіабудівної промисловості, машинобудівної галузі, так як відмінно захищає метал від впливу бензину, нафтопродуктів, кислот, мінеральних масел, лугів і вологи.
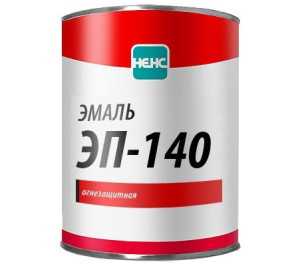
Для антикорозійного захисту сталі і чавуну використовується фарба “ЕП-5287” – підібрана суспензія органічних і неорганічних наповнювачів і пігментів, а також поліетиленполіамін (грає роль потужного затверджувача).
А ось захист опор мостів, резервуарів для нафти і будь-яких видів трубопроводів краще проводити за допомогою композиції “ЕП-5116”, яка зарахована до складів вищого класу якості.
Ефективне запобігання елементів автомобілів від іржавіння забезпечується матеріалами для фарбування під брендами:
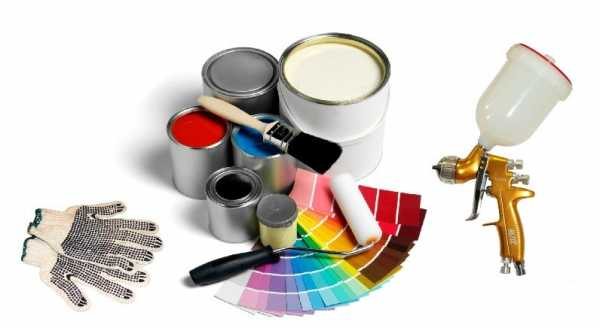
Ці засоби служать для фарбування металевих поверхонь з метою зміни зовнішнього вигляду і захисту від агресивно впливають факторів середовища, які призводять до утворення корозії.
Лакофарбові матеріали виконують захисні функції шляхом механічної ізоляції обробленого металу від зовнішнього середовища. Антикорозійний захист забезпечується ними завдяки взаємодії ЛКМ з поверхнею.
Для уражених корозією об’єктів або деталей кузова авто фарба по металу і іржі дозволяє запобігти подальше руйнування, а також служить для відновлення зовнішнього вигляду. Мова піде про те, якими бувають фарби і про антикорозійних емалях.
Для початку проведемо невеликий загальний огляд лакофарбових коштів по металу. Для металевих поверхонь, крім фарб проти корозії, існує безліч інших варіантів іншого призначення із специфічними властивостями. За складом їх класифікують на такі фарби:
У складі олійних фарб роль сполучного речовини виконує оліфа. В більшості випадків в якості основи для її виробництва застосовують натуральні масла. Дані лакофарбові матеріали добре підходять в основному для побутових робіт, частіше внутрішніх, але їх небажано використовувати для фарбування зовнішніх елементів, таких, як наприклад, покрівля.
Це обумовлено тим, що олійні фарби не забезпечують захист оброблених ними металевих поверхонь від корозії. До того ж, згідно з відгуками, вони швидко вицвітають і розтріскуються, не витримують температури понад 80°С. Зрозуміло, що для фарбування авто ця група матеріалів не використовується.
Алкідні фарби служать для обробки покритих цинком металевих поверхонь. Серед фарб по металу дані речовини мають найкращою схватываемостью, однак вони горючі і не витримують високих температур.
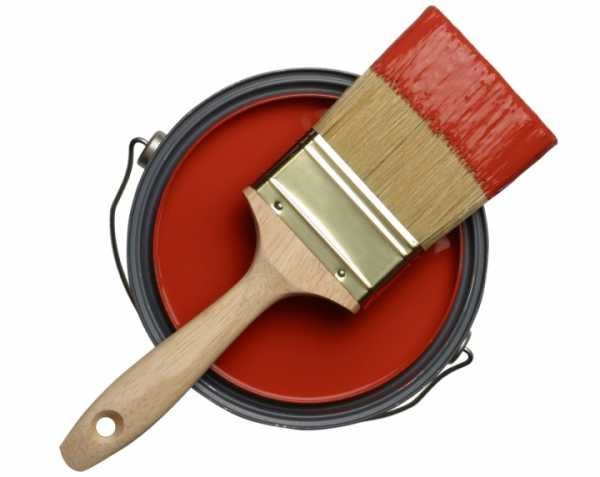
Акрилові фарби. Незважаючи на те, що це відносно новий вид лакофарбових матеріалів по металу, такі матеріали в даний час найбільш часто застосовують для їх фарбування.
Це обумовлено рядом характеристик даних речовин. Вони довговічні, забезпечують захист від корозії, не розтріскуються і не вицвітають. Завдяки цьому, вони підходять як для внутрішніх, так і для зовнішніх робіт.
Акрилові фарби витримують високі температури – до 120°С. Це дозволяє застосовувати їх в якості фарбування нагрівальних елементів. Внаслідок того, що аналізовані фарби водорастворимы, вони нетоксичні і негорючі.
Це дозволяє використовувати їх на вибухонебезпечних об’єктах і сильно нагріваються деталях. Асортимент акрилових автоемалей дуже широкий. Про ефективність названих варіантів фарб в різних умовах можна судити з відгуків.
Існує декілька способів захисту металу авто від корозії, на основі яких діють лакофарбові матеріали. Досить ефективними проти іржі вважають варіанти, які містять інгібітори, про що свідчать відгуки користувачів.
Під цим терміном розуміють речовини, що зменшують активність корозійного впливу води. Найбільш поширена речовина такого типу – свинцевий сурик. Зазвичай його застосовують в якості грунтовки і нерідко залишають без покриття. Однак внаслідок нееластичності даної речовини можлива подпленочная корозія.
Більшість антикорозійних фарб має трикомпонентний складу. Він представлений основним речовиною, грунтовкою і заключним покриттям:
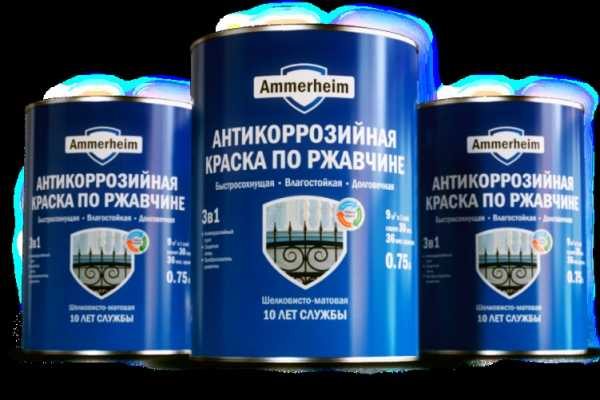
Ще більш ефективна протекторний захист. Про це свідчать як теоретичні основи, так і відгуки. Принцип даної технології полягає в утворенні пари металів, поверхневим з яких є більш активний. Отже, він першим піддається впливу корозії.
Для заліза і його сплавів найбільш часто застосовують як протекторного покриття цинк. Його широке поширення обумовлене безліччю чинників, серед яких:
У побутових умовах його наносять лише способом холодного цинкування. На ринку пропонують безліч цинкоутримуючий складів. Велика частина представлена цинконаполненными фарбами, які не забезпечують взаємодії між металами, так як є діелектриками.
Тому має сенс застосовувати лише склади для холодного цинкування. Вони являють собою фарби, в яких цинкова пудра перебуває у зваженому стані в полімерній основі.
Дані речовини володіють електропровідністю і високою щільністю, у зв’язку з чим мають велику масу. Для фарбування бажано використовувати цинкові склади в рідкій формі, а не аерозолі у зв’язку з більш низьким вмістом цинку в останніх і меншою товщиною шару.
Прикладом цинкового грунту для обробки автомобіля є Mipa AK 105-20, епоксидний грунт з цинком Zn-Primer від Hi-Geer та інші. Найчастіше вони використовуються для зварних швів, сталевих панелей.
Обробка металевих поверхонь фарбами є найбільш поширеним способом їх захисту від ураження корозією. Це пояснюється кількома причинами. По-перше, це найбільш доступний варіант обробки металу проти іржі, що дозволяє продовжити його експлуатаційний термін. По-друге, у цьому випадку не важлива форма оброблюваної поверхні, а розміри визначають кількість речовини. По-третє, шляхом застосування фарби можна надати металу будь-яку забарвлення.
Як видно, в процесі вибору фарб по металу попередньо потрібно визначитися з умовами застосування. Іншими словами, лакофарбовий матеріал вибирають на основі необхідності антикорозійного захисту, стійкості до підвищених температур, довговічності, токсичності.
Основними параметрами розглянутих лакофарбових матеріалів, які слід враховувати в процесі вибору, вважають адгезію, під якою розуміють зчеплення з офарблює поверхнею, і стійкість до підвищених температур. Інформацію про найбільш ефективних моделях фарб по металу можна отримати з відгуків споживачів.
Кузов автомобіля зроблений з металу, і це значить, що рано чи пізно він почне піддаватися шкідливому впливу вологи з киснем і буде іржавіти. Ця одна з найбільш неприємних рис металу.
Щоб уповільнити прояви корозії, необхідно ретельно стежити за станом лакофарбового покриття автомобіля і вчасно усувати виниклі дефекти.
Але в будь-якому випадку прийде час, коли буде необхідно усувати іржу з авто, і дізнатися, як це зробити своїми руками, допоможе ця стаття.
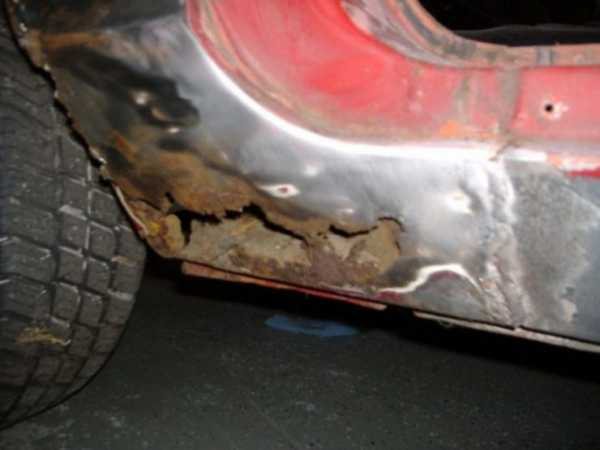
Основними місцями початкового появи слідів корозії є:
Їржу можна розділити на кілька видів, сліди визначають її характер, і метод усунення треба вибирати, керуючись виключно її характеристиками. Основні види – суха і волога. Суха з’являється в тому випадку, коли машина знаходиться в теплому приміщенні. При сухій корозії металеві деталі авто приймає темний колір, і їм потрібно антикорозійне покриття. Волога виникає від постійного контакту авто з вологою. Особливо цьому сприяє налипшая бруд на кузов авто, всередині якої довгий час зберігається вологість. Саме такий вигляд і несе в собі найбільшу небезпеку для металу.
По закінченні часу із-за іржі фарба починає злазити з місць ураження металу, і потрібно вжити заходів для її усунення. Просто зафарбувати пошкоджену ділянку не вийде, фарба дуже швидко злізе з автомобіля.
У зимовий час власники авто сприяють появі іржі на кузові, ставлячи її в тепле приміщення, де немає правильної вентиляції.
Це призводить до появи деяких типів корозії.
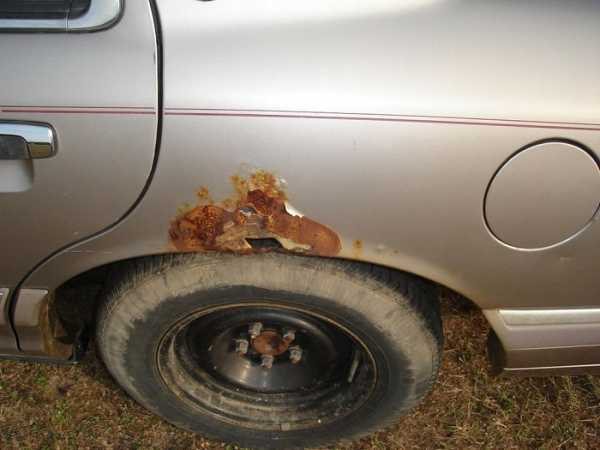
Щоб усунути з кузова авто іржу, треба правильно визначити її тип, яких існує декілька варіантів:
При виявленні будь-яких проявів іржі на кузові варто негайно почати усунення з місць її освіти, це посприяє продовженню терміну служби автомобіля на тривалий час.
Для проведення ремонту місць пошкодження знадобляться спеціалізований інструмент і чисте приміщення, куди можна поставити авто на кілька днів. З інструменту краще всього скористатися:
При наявності сухого і чистого приміщення, а також необхідних навичок, видалити пошкодження з автомобіля можна самостійно, не вдаючись до допомоги професіоналів, ніж зберегти чималі фінансові кошти.
Робота поділяється на декілька етапів:
Перед початком будь-яких зварювальних робіт треба відключити акумуляторну батарею авто, інакше може статися замикання в бортовій мережі, що призведе до виходу з ладу електронних систем управління.
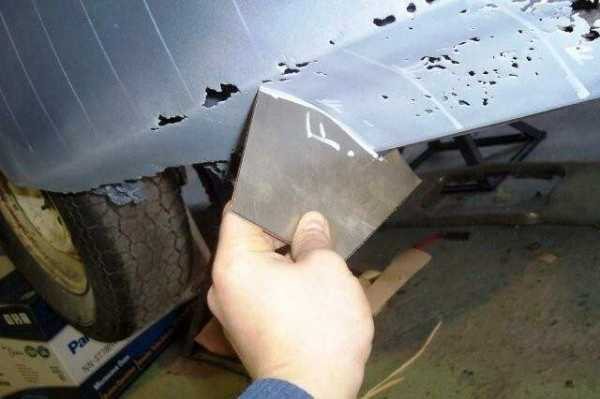
Проводити обробку перетворювачем треба в рукавичках, щоб уникнути ушкодження шкіри рук.
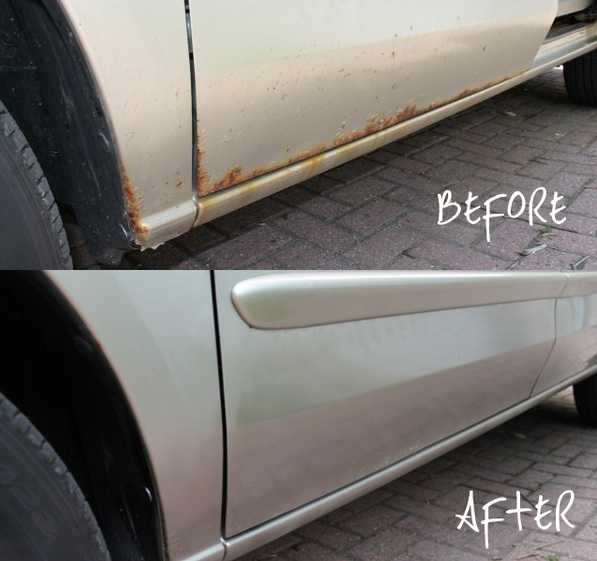
Приводити в порядок кузов машини, позбавляючи від корозійного ушкодження, – справа досить клопітка і довготривала. Набагато простіше уважно стежити за зовнішнім станом транспортного засобу і вчасно реагувати на появу на його лакофарбовому покритті сколів. Якщо здійснити належний догляд, фарба збереже прекрасний вигляд і надійно захищатиме метал кузова. Але якщо трапилася така неприємність, видалити корозійні сліди і продовжити термін служби найдорожчого елементу машини – цілком здійсненне завдання. Головне, проявити старанність при виконанні всіх етапів робіт і грамотний підхід до справи.
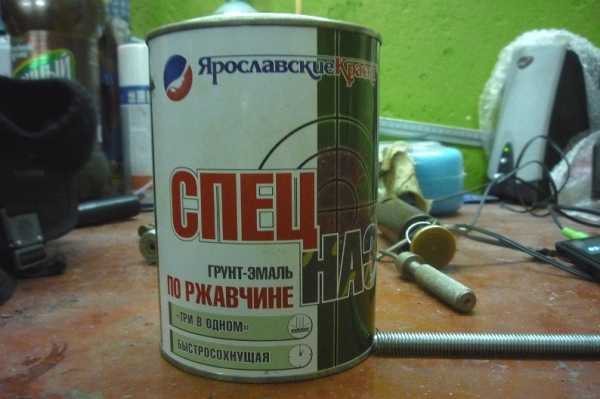
Завершальним і ключовим штрихом кузовних робіт є фарбування, яка не тільки надає обробленим елементів конструкції товарний вигляд, але і оберігає їх впливу навколишнього середовища. Незахищені деталі автомобіля під впливом повітря і вологи окислюються і втрачають міцнісні властивості. При експлуатації транспортного засобу в зимовий час його днище і крила постійно контактують з різними хімічними реагентами, що призводить до передчасного руйнування. Якісна грунтовка, не дозволяє іржі дістатися до металу, є запорукою високого ресурсу відремонтованого кузова автомобіля.
Ідеальні фарба і грунтовка повинні відповідати наступним критеріям:
Такі елементи транспорту, як днище, піддаються не тільки хімічним і температурному, але і механічного впливу. Фарба, скалываемая камінням та щебенем, вилітають з-під коліс, оголює метал, відкриваючи доступ іржі, яка починає активно роз’їдати незахищені ділянки. Але шукати супердорогий імпортний матеріал, щоб пофарбувати автомобіль, не обов’язково. Аналіз ринку показує, що вітчизняним виробникам по силам випускати продукцію, конкурентоспроможну з кращими західними аналогами. Численні позитивні відгуки споживачів можуть служити найкращими рекомендаціями для її використання.
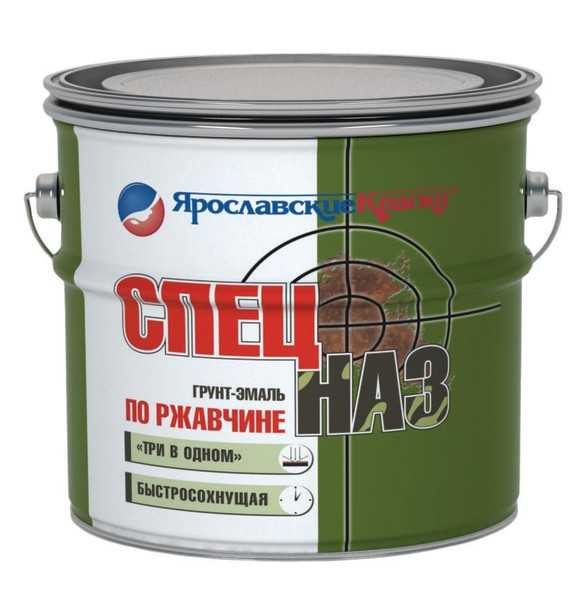
Під вищенаведені вимоги відмінно підходить універсальна фарба «Спецназ». Вона спеціально розроблена для роботи зі схильними до корозії металевими поверхнями і не вимагає попереднього очищення. Виробляється ця продукція «Ярославскими фарбами» і може використовуватися як грунтовка, так і на завершальних етапах обробки. По суті, «Спецназ» виконує три функції:
Фарба «Спецназ» рекомендується виробником для захисту як сталевих, так і чавунних поверхонь, що мають важкі залишки старого покриття. Її можна наносити прямо по іржі.
При ремонті автомобіля «Спецназ» рекомендується, в першу чергу, для таких деталей, як днище і крила, так як вони найбільш схильні до механічного і хімічного впливу навколишнього середовища. Фарба, нанесена в три шари, надійно захищає металеві поверхні від різних агресивних реагентів до температури 60 С, і численні позитивні відгуки автолюбителів підтверджують це.
Серед достоїнств грунт-емалі «Спецназ» слід виділити її здатність швидко сохнути. Ґрунтовка в два шари вимагатиме не більше години витримки: за 30 хвилин після кожного нанесення. Оптимальна температура для виконання робіт 20ºС, але допускається проводити фарбування при негативних температурах (до-10ºС). Заключний шар сохне приблизно 1 годину. Кілограма матеріалу вистачає, щоб покрити за один раз 7-10 кв. м поверхні. Універсальна фарба «Спецназ» не потребує додаткового захисту, але після того, як вона остаточно підсохне, через добу її можна при необхідності покрити лаком або емаллю типу: ЕП, ПФ, НЦ. ХВ або ХС.
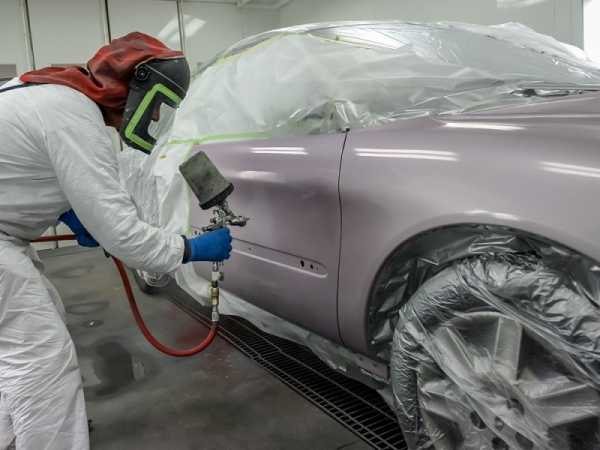
Фарба може наноситися різними способами, в залежності від наявності доступу до деталей. У роботі можна користуватися як пневморозпилювачи, так і пензлем. Дрібні елементи зручно фарбувати звичайним зануренням. Незважаючи на те, що «Спецназ» призначений для роботи по іржі, попередньою обробкою поверхонь нехтувати не варто. Слід обов’язково видаляти пухкі ділянки корозії, окалини і різні забруднення, використовуючи металеву щітку або насадку для дрилі. Після чого фарбується повинна бути знежирена уайт-спіритом або розчинником № 647. Останній можна також використовувати для розрідження фарби.
Відгуки більшості людей, що скористалися грунт-емаль «Спецназ», відзначають високу практичність продукту. Фарба, що не вимагає трудомісткою очищення малодоступних місць, полюбилася як автолюбителям, так і знайшли їй застосування в господарських цілях. Відгуки підтверджують, що матеріал прекрасно працює як грунтовка по іржі, розчиняючи її і забезпечуючи надійну адгезію з металевою поверхнею. Відзначається висока стійкість покриття днища і крил автомобіля і простота його нанесення, в поєднанні з відносно невеликою, особливо в порівнянні з імпортними аналогами, ціною фарби.
Позитивні відгуки про грунт-емалі «Спецназ» дозволяють рекомендувати її при проведенні кузовних робіт, особливо для важкодоступних ділянок конструкції автомобіля.
Ця фарба здатна надійно захистити метал від руйнівного впливу агресивних середовищ і не дати іржі можливості роз’їсти його структуру. Крім того, відгуки говорять про високої міцності покриття, що дозволяє уникнути випадкових відколів пофарбованої поверхні при експлуатації автомобіля, особливо при частих поїздках по грунтових дорогах.
До складу фарби «Спецназ» входять різні антикорозійні добавки, пігменти, синтетичні смоли, наповнювачі та розчинники. Хоча це продукт вітчизняного виробництва, але він містить компоненти, що випускаються в Німеччині, які забезпечують перетворення іржі в хімічно інертні з’єднання. Термін зберігання фарби становить півтора року з моменту виготовлення. Її перевагою є можливість зберігання при негативній температурі без втрати споживчих властивостей.
Будучи відносно новим продуктом, фарба «Спецназ» постійно модернізується. Так, зовсім недавно з’явилася її нова різновид – Рідкий цинк. Покриття з її використанням володіє підвищеною стійкістю і міцністю.
При появі на шарі фарби якого-небудь дефекту цинк окислюється, утворюючи додатковий захист основного металу від іржі. Крім високих технічних характеристик, таке покриття, за відгуками споживачів, має чудовий товарний вигляд. Фарба «Спецназ» придатна не тільки для кузовних робіт.
Вона відмінно підходить для фарбування дверей гаража, металевої огорожі та інших виробів, які мають складну конфігурацію і експлуатованих у вуличних умовах або агресивному атмосфері.
Тверді діелектрики. Класифікація, галузь застосування, характеристики.
Загальні характеристики твердих діелектриків.
Тверді діелектрики - це надзвичайно широкий клас речовин, що містить речовини з, що радикально різняться електричними, теплофізичними, механічними властивостями.
Наприклад, діелектрична проникність міняється від значення, що незначно перевищує 1, до більш ніж 50000, залежно від типу діелектриків: неполярний, полярний, сегнетоелектрик. На початку курсу приводилися визначення різних типів діелектриків. Коротенько торкнемося цих визначень стосовно до твердих діелектриків.
Неполярний діелектрик - речовина, що містить молекули з переважно ковалентним зв'язком.
Полярний діелектрик - речовина, що містить дипольні молекули або групи, або, що має іони в складі структури.
Сегнетоелектрик - речовина, що має в складі області зі спонтанною поляризацією.
Механізми поляризації в них різко різняться:
- чисто електронна поляризація в неполярних діелектриків типу поліетилена, полістиролу, при цьому діелектрична проникливість ε -невелика, не більш 3, діелектричні втрати теж малі;
- іонна поляризація в іонних кристалів типу NaСl або дипольна в полярних діелектриків типу льоду, при цьому ε може перебувати в межах від 3-4 до 100, діелектричні втрати можуть бути досить значні, особливо на частотах обертання диполів і інших резонансних частотах;
- доменна поляризація в сегнетоелектриків - при цьому ε максимальна й може досягати 10000-50000, діелектричні втрати можуть бути досить значні, особливо на резонансних частотах і в області підвищених частот.
Особливості механізмів провідності у твердих діелектриках - концентрація носіїв дуже мала, рухливість іонів у гомогенних матеріалах дуже мала, рухливість електронів у чистих матеріалах велика, у технічно чистих - мала. Механізми електропровідності різні в різних речовинах. Іонна провідність реалізується в полідисперсних діелектриків (картон, папір, гетинакс, дерево) і іонних кристалів. У першому випадку іони пересуваються по границях роздягнула, утвореним злиплими дисперсними частками.
Поява носіїв заряду сильно пов'язане з вологістю цих матеріалів і визначається, як розглядалося в гл.1 і 2 дисоціацією домішок і полярних груп основної речовини на поверхні роздягнула. У випадку іонних кристалів, у провідності беруть участь іони основної речовини, домішок, дефекти структури. Електронна провідність реалізується в титанатів барію, стронцію і т.д., електронна, діркова й іонна провідність у полімерів.
Додамо деякі терміни, специфічні для твердих діелектриків:
хімічна стійкість - здатність витримувати контакти з різними середовищами (кислота - кислотостійкість, луг - лугостійкість, озон - озоностійкість, масло - маслостійкість, вода - водостійкість);
трекінгостійкість - здатність протистояти дії дуги;
дендритостійкість - здатність протистояти утворенню дендритів.
3.4.2. Види діелектриків. Застосування твердих діелектриків в енергетиці.
Усі діелектричні матеріали можна розділити на групи, використовуючи різні принципи, наприклад, розділити на неорганічні й органічні матеріали.
Неорганічні діелектрики: скла, слюда, кераміка, неорганічні плівки (окисли, нітриди, фторидів), металлофосфати, електроізоляційний бетон. Особливості неорганічних діелектриків - негорючі, як правило, світло-, озоно- термостійкі, мають складну технологію виготовлення. Старіння на змінній напрузі практично відсутні, схильні до старіння на постійній напрузі.
Органічні діелектрики: полімери, воски, лаки, гуми, папери, лакотканини. Особливості органічних діелектриків - горючі (в основному), малостійкі до атмосферних і експлуатаційних впливів, мають (в основному) просту технологію виготовлення, як правило, більш дешеві в порівнянні з неорганічними діелектриками. Старіння на постійній напрузі практично відсутнє, на змінній напрузі старіють за рахунок часткових розрядів, дендритів і водних тріінгів.
Застосування в енергетику:
- лінійна й підстанційна ізоляція - це порцеляна, стекло й кремнійорганічна гума в підвісних ізоляторах ПЛ, порцеляна в опорних і прохідних ізоляторах, склопластики як несучі елементи, поліетилен, папір у високовольтних уведеннях, папір, полімери в силових кабелях;
- ізоляція електричних приладів - папір, гетинакс, склотекстоліт, полімери, слюдяні матеріали;
- ізоляція машин, апаратів - папір, картон, лаки, компаунди, полімери;
- конденсатори різних видів - полімерні плівки, папір, оксиди, нітриди.
Із практичної точки зору в кожному випадку вибору матеріалу електричної ізоляції слід аналізувати умови роботи й вибирати матеріал ізоляції відповідно до комплексу вимог. Для орієнтування доцільно розділити основні діелектричні матеріали на групи за умовами застосування.
1. Нагрівостійка електрична ізоляція. Це в першу чергу виробу зі слюдяних матеріалів, деякі з яких здатні працювати до температури 700 ° С. Скла й матеріали на їхній основі (склотканини, склослюдініти). Органосілікатні й металофосфатні покриття. Керамічні матеріали, зокрема нітрид бору. Композиції із кремнійорганіки з термостійким сполучним. З полімерів високу нагрівостійкість мають поліімід, фторопласт.
2. Вологостійка електрична ізоляція. Ці матеріали повинні бути гідрофобні (незмочування водою) і негігроскопічні. Яскравим представником цього класу є фторопласт. У принципі можлива гідрофобізація шляхом створення захисних покриттів.
3. Радіаційно-стійка ізоляція. Це, у першу чергу, неорганічні плівки, кераміка, склотекстоліт, слюдинітові матеріали, деякі види полімерів (полііміди, поліетилен).
4. Тропікостійка ізоляція. Матеріал повинен бути гідрофобним, щоб працювати в умовах високої вологості й температури. Крім того, він повинен бути стійким проти цвілевих грибків. Кращі матеріали: фторопласт, деякі інші полімери, гірші - папір, картон.
5. Морозостійка ізоляція. Ця вимога характерна, в основному для гум, тому що при зниженні температури всі гуми втрачають еластичність. Найбільш морозостійка кремнійорганічна гума з фенільними групами ( до -90°С).
6. Ізоляція для роботи у вакуумі (космос, вакуумні прилади). Для цих умов необхідно використовувати вакуумно-щільні матеріали. Придатні деякі, спеціально приготовлені керамічні матеріали, малопридатні полімери.
Тверді діелектрики поділяються за хімічним складом на:
- органічні;
- неорганічні.
В радіотехніці особливе значення має урахування впливу частоти електричного поля на властивості матеріалу. Тому з поділом за хімічним складом ми будемо ділити діелектрики на полярні (низькочастотні) та неполярні (високочастотні).
Розглянемо органічні діелектрики.
Першим представником органічних діелектриків є смоли.
Смоли – це аморфні високомолекулярні речовини, які можуть бути в трьох станах: склоподібному, еластичному та в’язкотекучому.
Поділяються на:
- термопластичні – в них перехід від твердого стану до пластичного може відбуватися багаторазово;
- термореактивні - в них перехід від твердого стану до пластичного відбувається лише один раз, смолу не можливо повернути до пластичного стану.
Використовуються для виготовлення пластмас.
Неполярні високочастотні полімери:
- Поліетилен – продукт полімеризації газоподібного етилену (С2Н4). Використовується як ізолюючий матеріал для провідників та кабелів, для виготовлення каркасів котушок індуктивності, як діелектрик в конденсаторах.
- Полістирол – полімер стирола (С2Н3С6Н5). Має високі діелектричні характеристики, особливо на ВЧ та НВЧ. Його недоліки – низька нагрівостійкість (80 оС), швидке старіння. Використовується для виготовлення волокна, плівок, каркасів, лампових панелей, ізоляційних деталей в ВЧ апаратурі.
- Фторопласт 4 – політетрафторетилен. Один з найкращих матеріалів для діапазону ВЧ та НВЧ. Має високу нагрівостійкість ( до 300 оС). Хімічна стійкість більша ніж у золота та платини. Не горючий. Не гігроскопічний, не змочується водою.Має малий коефіцієнт тертя. Легко оброблюється різанням. Має малу теплопровідність. При температурах вищих за 400 оС виділяє фтор (отруйний газ). Використовується там де потрібні високі діелектричні властивості при дії агресивних середовищ.
Характеристики неполярних ВЧ полімерів наведені в табл.
Таблиця.
Характеристики неполярних ВЧ полімерів.
Параметр | Одиниця виміру | Поліетилен | Полістирол | Фторопласт 4 |
Електрична міцність | МВ/м | 40...150 | 20...110 | 40...150 |
Робоча температура | оС | - 60...+110 | -40...+80 | -296...+300 |
Діелектрична проникність, ε | Відносних одиниць | 2,3...2,4 | 2,5...2,6 | 1,9...2,2 |
tgδ | Відносних одиниць | 0,0002...0,0003 | 0,0002...0,0004 | 0,0002...0,0003 |
Питомий опір, ρ | Ом∙м | 1014 | 1015 | 1017 |
Полярні НЧ полімери.
Для них характерні висока діелектрична проникність, низький tgδ. Основні характеристики приведені в табл.
Таблиця.
Характеристики НЧ полімерів.
Параметр | Одиниці виміру | Полівінілхлорид | Лавсан | Нейлон, капрон | Фторопласт 3 | Силікони |
ε | Відносних одиниць | 3,5...4,5 | 3...3,5 | 5...6 | 3,5 | 3,5 |
tgδ | Відносних одиниць | 0,2...0,5 | 0,002 | 0,06 | 0,04 | 0,01...0,03 |
ρ | Ом∙м | 1012 | 1012 | 109 | 1013 | 1014 |
Tmax | оС | |||||
Tmin | оС | -35 | -80 | -40 | -195 | -70 |
Використовуються для ізоляції монтажних проводів (полівінілхлорид), вт конденсаторах (лавсан), для виготовлення термотривких компаундів, лаків, каучуків (силікони), для виготовлення складних деталей (лампові панелі, гнізда та інш.), для конденсаторів (фторопласт3).
Електроізоляційні лаки та емалі використовуються для захисту елементів апаратури від корозії, пилу та вологи. Вони поділяються за використанням на: просочувальні, покрівельні та ключі.
За складом електроізоляційні лаки та емалі можна поділити на:
- полімерні (полістирольний та епоксидний лаки, тобто ті, в яких плівкоутворюючими елементами є полімери – полістирол, полівінілхлорид) та смоли (епоксидна, кремнійорганічна).
- нітроцелюлозні – розчини нітроцелюлози в ацетоні. Вони швидко висихають, але мають погану адгезію до металу та малу нагрівостійкість.
- масляні –до них відносяться ті, що мають висихаючи масла )лляне чи синтетичне).
Компаунди – це суміші смол, бітуму та воску. Використовуються для просочення та заливки елементів РЕА (трансформаторів, блоків, котушок і т. д.). При цьому досягається захист елементів від дії атмосфери, підвищуються електроізоляційні властивості, покращується відвід тепла, збільшується механічна міцність.
Волокнисті матеріали – складаються з частинок подовженої форми- волокон. Мають високу механічну міцність, легко оброблюються, дешеві. Для них характерна невисока електрична міцність та теплопровідність. Головний недолік – гігроскопічність. До волокнистих матеріалів відносяться:
- конденсаторний папір;
- електрокар тон;
- текстильні ізоляційні матеріали.
Використовуються в конденсаторах, конструкційних елементах, для виготовлення ізоляції проводів та шнурів.
Матеріали для друкованих плат – це слоїсті пластики, на які наклеєна тонка (18, 30 або 50 мкм) мідна фольга. Основні типи матеріалів наведені в табл.
Таблиця.
Матеріали для друкованих плат
Марка | ε, відносних одиниць | tgδ, відносних одиниць | ρ, Ом·м | Епроб, МВ/м | Область застосування |
Гетинакс фольгований ГФ-1-11 | 0,035 | 1010 | РЕА широкого призначення | ||
Склотекстоліт фольгований СФ-1 | 0,05 | 1013 | Плати зі збільшеною стабільністю | ||
Склотекстоліт для мікроелектроніки ФДМЭ-1 | 0,025 | 1010 | Багатошарові плати для обчислювальної техніки | ||
Фторопласт фольгова ний ФФ-4 | 2,1 | 0,0002 | 1017 | Плати НВЧ діапазону | |
Поліетилен фольгований ПЭФ-1 | 2,2 | 0,0005 | 1015 | Плати НВЧ діапазону |
Рідкі кристали – рідини, які знаходяться в проміжному стані між кристалом та рідиною і мають анізотропні властивості. Це органічні з’єднання, молекули яких мають подовжену або паличкову форму. Структура РК легко змінюється при зовнішніх впливах (магнітне, електричне поля, температура, тиск). Використовуються в індикаторних пристроях пасивного типу (РК - індикатори, панелі).
Неорганічні діелектрики.
До неорганічних діелектриків відносяться:
- неорганічне та напівпровідникове скло;
- склокераміка (ситали);
- кераміка;
- слюдяні матеріали.
Неорганічне скло – це аморфний матеріал, до ч складу якого входять складні системи різних окислів. За звичайних умов скло має властивості твердого матеріалу. При нагріванні – перетворюється в рідину. Одержують скло при охолодженні розплаву, що складається із оксидів SiO2, B2O3, Na2O, K2O, CaO, MgO, PbO, ZnO, Al2O3. При варці оксиди утворюють силікати, борати та алюмінати.
Збільшення в складі SiO2 підвищує тугоплавкість, покращує діелектричні властивості та зменшує коефіцієнт лінійного розширення скла (силікатне скло).
Присутність лужних оксидів Na2O, K2O збільшує ε та зменшує tgδ, але вона зменшує нагрівостійкість скла.
Використовується в основному для виготовлення колб електровакуумних ламп.
Напівпровідникове скло – скло чорного кольору, завдяки присутності оксидів заліза. Має електронну провідність n чи p типу в залежності від його складу. Якщо на звичайне скло нанести тонке н/п покриття, то таке скло буде поєднувати н/п властивості з прозорістю. Для цього використовують SnO2, In2O3, TiO2 з добавками CaO, ZnO. Такі шари товщиною в декілька мікрон забезпечують питомий поверхневий опір від 10 до 40 Ом. З н/п скла виготовляють нагріваючі стекла, посуди для нагрівання рідин, конденсаторів, фотоелементів, плівкових резисторів, для вирівнювання напруг на скляних балонах електровакуумних приладів. Воно також використовується в складі склоемалей для захисту від корозії та придання деталям потрібного кольору.
Плівки SiO2 – використовуються в мікроелектроніці для одержання між шарової ізоляції. Має ε = 9...12; tgδ = 0,01...0,03 (на 1кГц) Епробивне = 100...300тМВ/м. Використовуються плівки товщиною від 0,3 до 3 мкм.
Склокераміка (ситали) – займає проміжне положення між склом та керамікою. Ситали – це скло керамічні матеріали, отримані шляхом стимуляції кристалізації скла спеціального складу, кристалізатором яких виступає Ag чи Cu, а також TiO2, FeS. Використовуються для виготовлення ізоляторів з низькими втратами на ВЧ та високих температурах. Основні параметри ситалів приведені в табл.
Таблиця.
Основні типи ситалів
Марка | ε | tgδ (на 106 Гц) | ρ, Ом·м |
СТ 32-1 | 20·10-4 | 1010 | |
СТ 38-1 | 7,35 | 30·10-4 | 1012 |
СТ 50-1 | 8,5 | 15·10-4 | 1012 |
Кераміка – основні компоненти це окисли алюмінію, кремнію, титану, цирконію, олова, магнію. Кераміка характеризується тим, що можливе отримання матеріалів з наперед заданими характеристиками шляхом зміни складу та технології виготовлення.
Кераміка – це багатофазна система, яка складається з кристалічної та скловидної фаз. Кристалічна фаза це різні хімічні з’єднання та тверді розчини цих з’єднань. Визначає основні характеристики кераміки – ε, tgδ, ρ, механічну міцність, температурний коефіцієнт лінійного розширення. Скловидна фаза – це скло, яке зв’язує кристалічну фазу. Визначає технологічні властивості кераміки – температуру спікання, пластичність при формуванні та інше.
В залежності від призначення ділиться на три типи:
- А – ВЧ для конденсаторів;
- Б – НЧ для конденсаторів;
- В – ВЧ для установочних деталей. Основні характеристики кераміки такі:
ε = 7...200, (для установочних деталей ....для конденсаторів), tgδ = (4...50)·10-4: Епроб = 4...20 МВ/м; діапазон робочих температур - -60...+300 оС.
Слюда – це мінерал, що легко розчіплюється на тонкі листки. За хімічним складом відносяться до водяних алюмосилікатів. Є дві різновидності слюди:
- мусковіт (K2O·Al2O3·6SiO2·2H2O) – матеріал без кольору іноді з червонуватим або зеленуватим відтінком.
- флогопіт (K2O·6MgO·Al2O3·SiO2·2H2O) – більш темного кольору, від коричневого до чорного тону.
Мусковіт – один з найкращих електроізоляційних матеріалів та ВЧ діелектриків. Має високу електричну міцність Епроб = 100...200МВ/м; ε = 5...10), tgδ = 3·10-4 (на 1 МГц).
Використовується для виготовлення електроізоляційних шайб, ізоляторів для електровакуумних приладів, в конденсаторах високої якості.
характеристики і область застосування твердих діелектриків: волокнисті матеріали, пластмаси, слюдяні матеріали, електроізоляційна кераміка.Для ізоляції електричних машин і апаратів широко застосовують різні волокнисті матеріали рослинного походження (папір, картон, бавовняні і шовкові волокна, тканини і стрічки), а також деякі синтетичні текстильні матеріали, одержувані хімічною переробкою окремих речовин: штучний шовк, синтетичні волокна (капрон, нейлон), матеріали з полістиролу, поліхлорвінілу, поліамідні і триацетатні плівки. Органічні волокнисті ізоляційні матеріали відрізняються невисокою нагревостойкостью. і в природному вигляді без спеціальної обробки відносяться до класу Y. Їх недолік - висока гігроскопічність. Між їх волокнами і нитками залишаються повітряні проміжки (пори), легко поглинають вологу.
Папір і картон - листові матеріали коротко-волокнистої будови, що складаються з целюлози. Папір виготовляють з подрібненого бавовняного ганчір'я і волокон деревини, які піддають спеціальній хімічній обробці. Всі сорти паперу мають гарні ізоляційні властивості, однак в електромашинобудуванні застосовують тільки такі спеціальні сорти: кабельну (товщиною 0,08-0,17 мм), телефонний (0,05 мм), конденсаторну (7-30 мк), обклеювальну (0, 33 мм), просочувальну (0,12 мм), намотувальні (0,05-0,07 мм) і мікастрічкових (20 мк).
Зазначені сорти паперу використовують для ізоляції обмотувальних проводів і кабелів різного типу, виготовлення конденсаторів, обклеювання листів електротехнічної сталі, а також для виготовлення Мікаленти (див. Нижче) і різних шаруватих пластичних матеріалів (листового і фасонного гетинакса, бакелітових трубок та ін.).
Картон виготовляють з того ж сировини, що і папір, але він має значно більшу товщину. У електромашинобудуванні застосовують такі сорти картону: електрокартон, фібру і літероід.
Пластичні маси -це матеріали, здатні в прес-формах під дією зовнішнього тиску приймати необхідний вид. Велика частина ізоляційних пластмас (наприклад, з органічними сполучними) вимагають також підвищеної температури. До переваг їх, в першу чергу, відноситься висока економічність.
Пластмаси, використовувані в електротехніці, - це найчастіше ізоляційні матеріали, що складаються з двох основних складових: пов'язує і наповнювача. До перших відносяться смоли, бітуми, цемент і ін. До других - порошкоподібні матеріали (деревна або кам'яне борошно), волокнисті (бавовняну, азбестове або скляне волокно і ін.), А також листові вироби (папір, текстиль і т. П.) .
Наповнювач в основному покращує механічні характеристики ізоляції, але знижує електричні, до того ж підвищує гігроскопічність. Ось чому для пластмас, від яких потрібні високі електроізоляційні властивості, нерідко від наповнювачів відмовляються, хоча вони значно їх здешевлюють. В пластмаси вводяться ще пластифікатори (для підвищення гнучкості) і барвники (для отримання потрібного зовнішнього вигляду).
Електричні і механічні характеристики, а також нагреостойкость пластмас залежать від сполучного і від наповнювача. EПР в середньому становить 3,0-40 МВ / м (при 20 ° С), нагревостойкость коливається від А до Н.
Промисловістю пластмасові вироби випускаються у вигляді заготовок і готових фасонних деталей часто складної конфігурації.
Область застосування пластмас дуже велика: від корпусів побутових електроприладів до ізоляційних деталей складної конфігурації для електричних машин і апаратів.
Слюда є основою великої групи електроізоляційних виробів. Головне достоїнство слюди - висока термостійкість поряд з досить високими електроізоляційними характеристиками. Слюда є природним мінералом складного складу. В електротехніці використовують два види слюди: мусковіт КАl2 (АlSi3О10) (ОН) 2 і флогопит КMg3 (АlSi3О10 (ОН) 2. Високі електроізоляційні характеристики слюди зобов'язані її незвичайного будовою, а саме - шаруватості. Слюдяні пластинки можна розщеплювати на плоскі пластинки аж до субмікронних розмірів. Руйнують напруги при відриві одного шару від іншого шару складають приблизно 0.1 МПа, тоді як при розтягуванні вздовж шару - 200-300 МПа. З інших властивостей слюди відзначимо невисокий tgd, менш ніж 10-2; високий питомий опір, більш 1012 Ом · м; досить високу електричну міцність, більш 100 кВ / мм; термостійкість, температура плавлення понад 1200 ° С.
Слюда використовується в якості електричної ізоляції, як у вигляді щипана тонких пластинок, в. т. ч. склеєних між собою (міканіти), так і у вигляді слюдяних паперів, в. т. ч. просочених різними сполучними (слюдиніту або слюдопласт). Слюдяная папір виробляється за технологією, близькою до технології звичайного паперу. Слюду роздрібнюють, готують пульпу, на машинах з виробництва паперу розгортають аркуші паперу.
Електроізоляційна кераміка являє собою матеріал, що отримується з формувальної маси заданого хімічного складу з мінералів і оксидів металів. Будь-яка кераміка, в тому числі і електроізоляційна, - матеріал багатофазних, що складається з кристалічної, аморфної і газової фаз. Її властивості залежать від хімічного і фазового складів, макро- і мікроструктури і від технологічних прийомів виготовлення./1/ В електричної та радіоелектронної промисловості керамічна технологія широко застосовується для виготовлення діелектричних, напівпровідникових, п'єзоелектричних, магнітних, металокерамічних і інших виробів. В даний час, особливо з проникненням в побут електронної техніки, з електроізоляційної кераміки виготовляються десятки тисяч найменувань виробів масою від десятих часток грама до сотень кілограмів і розмірами від декількох міліметрів до декількох метрів. У ряді випадків вироби з кераміки, головним чином з електрофарфору, покриваються глазур'ю, що зменшує можливість забруднення, покращує електричні і механічні властивості, а також зовнішній вигляд виробу./14/ Електрофарфор є основним керамічним матеріалом, використовуваним у виробництві широкого асортименту низьковольтних і високовольтних ізоляторів та інших ізоляційних елементів з робочою напругою до 1150 кВ змінного і до 1500 кВ постійного струму.
Пластмаси. Основні характеристики пресованих
матеріалів і пластмас.
Залежність характеристик пластмас від наповнювачів і в'яжучих.
Особливості пластмас, їхні переваги і недоліки. Пластмасами називають матеріали, створені на основі природних або синтетичних високомолекулярних сполук, які здатні під впливом нагрівання і стискування перетворюватися на вироби.
Основою (зв'язувальною речовиною) пластмас є високомолекулярні сполуки — полімери. Більшість полімерів перебувають в аморфному стані і називаються смолами. У виробництві пластмас зазвичай застосовують синтетичні і рідше — природні смоли.
Головними цінними властивостями пластмас є: мала щільність — 940...1500 кг/м3 (0,94...1,50 г/см3), рідше до 2300 кг/м3; високі ді-електричні властивості і стійкість до корозії; низька теплопровідність; антифрикційні властивості одних і фрикційні властивості інших пластмас; високі декоративні властивості; значна механічна міцність у волокнистих та шаруватих пластмасах; добрі технологічні властивості, що дають змогу виготовляти вироби високопродуктивними методами (без зняття) стружки.
До недоліків пластмас належать такі: деякі пластмаси деформуються при нагріванні, а за низьких температур стають крихкими; пластмаси мають низьку теплостійкість (здебільшого не перевищує 100... 120 °С); деякі пластмаси поглинають вологу (набухають), а деякі змінюють свої властивості під впливом атмосферних, температурних і хімічних чинників (старіють); у високомолекулярних пластмас зменшується еластичність, виникає жорсткість і крихкість, знижується механічна міцність.
Залежно від реакції смол при нагріванні пластмаси, що виготовлені на їхній основі, поділяють на термопластичні і термореактивні.
Термопластичні пластмаси при багаторазовому нагріванні й охолодженні зберігають здатність пом'якшуватися (переходити в пластичний стан), плавитись і знову тверднути. Завдяки цим властивостям такі пластмаси можна багаторазово переробляти.
Термореактивні пластмаси, нагріваючись, плавляться і за певної температури тверднуть унаслідок утворення складних тривимірних молекул; повторне нагрівання не повертає їм здатності плавитись.
Крім смоли, пластмаси можуть містити 40...70% наповнювачів, пластифікатори та інші добавки.
Наповнювачами є порошкові, волокнисті і листові матеріали. Вони зміцнюють і здешевлюють пластмасу, а також надають їй певних фізико-механічних і технологічних властивостей. Прозорі полімери наповнювачів не мають.
Пластифікаторами називають низькомолекулярні речовини (гліцерин, парафінове масло та ін.).
Крім зазначених компонентів, до складу пластмас можуть входити різні добавки: стабілізатори, каталізатори, мастильні речовини, барвники тощо.
Стабілізатори затримують руйнування — старіння полімеру під дією світла, підвищеної температури та інших чинників (сажа, сполуки олова і свинцю та ін.).
Каталізатори прискорюють процес тверднення пластмас (уротропін тощо).
Мастильні речовини полегшують пресування пластмас і не дають їм змоги прилипати до стінок прес-форми (стеарин, віск та ін.)
Фарбники надають пластмасам різних кольорів (вохра, крон, сурик та ін.)
КЛАСИФІКАЦІЯ І ЗАСТОСУВАННЯ ПЛАСТМАС.
Нині застосовують кілька тисяч пластмас, які відрізняються одна від одної складом і властивостями.
Пластмаси, що використовуються як конструкційні матеріали, класифікують за видом наповнювачів. За цією ознакою розрізняють пластмаси без наповнювачів, з наповнювачами (порошкові, волокнисті і шаруваті), а також газонаповнені полімерні матеріали.
Пластмаси без наповнювачів — це здебільшого термопластичні полімери. Випускають їх у вигляді порошків та гранул і використовують для виготовлення різних деталей та напівфабрикатів. Іноді до складу цих пластмас вводять незначну кількість наповнювачів, щоб надати їм спеціальних фізичних або механічних властивостей.
Поліетилен має високі антикорозійні і діелектричні властивості, добру стійкість до лугів, розчинів солей та сильних кислот. Теплостійкість його становить 110... 120 °С, морозостійкість до мінус 70 41 Поліетилен застосовують для виготовлення труб, кранів, кабелів, деталей арматури, листів, плівок, пляшок, балонів, плащів та ін.
Поліпропілен має вищу міцність і теплостійкість (до 140 °С), ніж поліетилен, проте його морозостійкість нижча (-5...-15 °С). Він е добрим діелектриком. Поліпропілен водостійкий і хімічно стійкий. З нього виготовляють плівки, труби для гарячої води, корпуси насосів, деталі холодильників і автомобілів.
Вініпласти (поліхлорвініл) мають теплостійкість до 60...70 °С, високу механічну міцність, але низьку ударну в'язкість. Цей матеріал має властивість повзучості, набухає у воді. Його застосовують для виготовлення труб, ізоляції електрокабелів, шлангів, плівки, лінолеуму. Для хімічної промисловості з нього виготовляють фільтри, змійовики, крильчатки насосів.
Полістирол — пластик, який має високу водостійкість і діелектричні властивості. Він стійкий до дії мінеральних кислот, лугів, спиртів, але руйнується від азотної кислоти. До його недоліків належать горючість, невисока теплостійкість (до 95 °С), крихкість, здатність до розтріскування в експлуатації. З полістиролу виготовляють деталі технічного і побутового призначення, деталі приладів, холодильників, радіоапаратів, плівки, труби.
Органічне скло (плексиглас) — замінник звичайного силікатного скла. Воно легше за силікатне і до того ж еластичне, має високі діелектричні властивості, масло-, бензо - і водостійке, а також стійке до розведених лугів, кислот, солей, проте розчинне у вуглеводнях, набухає в спиртах і має недостатню термостійкість (до 80 °С), легко пошкоджується від механічної дії. Органічне скло використовують для скління вікон автомобілів і вагонів, в оптичній і годинниковій промисловості, у світлотехніці, для виготовлення прозорих трубок, посуду, підфарників, деталей приладів і апаратів та ін.
Капрон — стійкий матеріал до розведених мінеральних кислот, лугів, досить міцний на розрив, твердий та еластичний. Плавиться за температури 225 °С, проте за температур, вищих від 100 °С і нижчих ніж 0 °С, його механічна міцність знижується. Капрон застосовують для виготовлення деталей вузлів тертя. Інколи ним замінюють кольорові метали і сплави при виготовленні вкладишів підшипників, втулок, манжет, зубчастих передач та інших деталей. Капрон використовують також для виготовлення плівок, волокон, корду, тканин, сіток, канатів тощо.
Пластмаси з наповнювачами частіше виготовляють на основі фенолоформальдегідних смол, які залежно від хімічного складу можуть бути термопластичними і термореактивними.
Термопластичні смоли при нагріванні до 100... 120 °С плавляться, а при охолодженні — тверднуть. Вони розчиняються в спирті, ацетоні та інших органічних розчинниках.
Термореактивні смоли при нагріванні переходять у рідкий стан, маючи розчинні властивості в органічних розчинниках (ацетоні. спирті та ін.), а при переході у твердий стан стають неплавкими та нерозчинними. Зміна властивостей смоли пов'язана з переходом лінійної структури макромолекул у сітчасту.
Для виготовлення технічних виробів використовують складні композиційні пластичні маси, до складу яких крім фенолформальдегідної смоли входять різні наповнювачі, що поліпшують їхні фізико-механічні властивості і знижують вартість.
До порошкових наповнювачів належать деревне борошно, мелений азбест, кварцове борошно, тальк, мелений шлак, графіт; до волокнистих — подрібнена бавовняна целюлоза, азбестові і скляні волокна.
Застосовують багато пластмас з порошковими і волокнистими наповнювачами. Деякі з них наведено нижче.
Амінопласти одержують на основі карбаміду, меламіну і деяких інших сполук з формальдегідом. їх змішують із сульфітною целюлозою (наповнювач), мастильними речовинами, барвниками і отримують прес-порошки, пофарбовані в різні кольори. Методом гарячого пресування виготовляють різноманітні вироби. їх використовують при виготовленні кольорових телефонних апаратів, рукояток меблевої фурнітури, корпусів і абажурів ламп, світильників, ручок приладів.
Волокніт — волокниста пластмаса на фенолформальдегідній смолі з наповнювачем із бавовняної целюлози. Він удароміцний і застосовується для виготовлення маховиків, рукояток верстатів, інструменту, кришок, пробок, шківів, кулачків, шестерень, роликів конвеєрів та ін.
Скловолокнистий матеріал одержують із зв'язуючих (синтетичної смоли) і скляних волокон (наповнювачів). Застосовують для виготовлення хімічно стійких труб та резервуарів, баків, залізничних цистерн, електрощитів, деталей електро - і радіотехнічної апаратури, кузовів автомобілів тощо.
Скловолокнистий анізотропний матеріал (СВАМ) має міцність, яка досягає міцності маловуглецевої сталі і становить 480...560 МПа. і
Азбоволокніт складається з азбестового волокна, меленого кварцу і добавок, зв'язаних силіційорганічною смолою. Він має високу теплостійкість і застосовується для теплозахисного покриття. Ці матеріали характеризуються високими фрикційними властивостями і використовуються в гальмових пристроях (гальмові колодки, диски, накладки, деталі пристроїв запалювання, вмикачі та ін.).
Склотекстоліт одержують із склотканини з різним переплетенням, просоченої поліефірною, епоксидного та іншими смолами. Склотекстоліт випускають у вигляді плит і листів завтовшки до 30 мм. Це цінний конструкційний матеріал, який застосовують для виготовлення кузовів легкових і вантажних автомобілів, деталей машин. В електротехніці його використовують як електроізоляційний матеріал.
Текстоліт — це пластик у вигляді листів і товстих плит (до 70 мм), стрижнів діаметром 8...60 мм, труб і фасонних виробів. Із нього виготовляють важливі деталі машин: шестерні, вкладиші підшипників, панелі, прокладки, амортизаційні, антифрикційні та електроізоляційні деталі.
Гетинакс складається з листів спеціального паперу, просочених резольними смолами і спресованих за температури 150... 160 °С Гетинакс може працювати за температури —60...—70 °С. Його випускають у вигляді листів і плит завтовшки до 5 мм, стрижнів і трубок діаметром до 25 мм. Використовують його також для виготовлення електропанелей, деталей трансформаторів, радіо - і телефонів, для облицювання кабін.
Азботекстоліт одержують із азбестової тканини або азбокарто-ну, просоченої резольною фенолформальдегідною смолою. Азботекстоліт випускають у вигляді листів і плит завтовшки до 60 мм. З нього виготовляють деталі гальмових пристроїв, фрикційні диски, деталі механізмів зчеплення, прокладки, які працюють за температур до 250 °С, та ін.
Газонаповнені полімерні матеріали — пластмаси зі щільністю 30...300 кг/м3. Мала щільність пояснюється великою кількістю пор, заповнених газом (повітрям, азотом, вуглекислим газом). Ці матеріали поділяють на дві групи: матеріали з ізольованими порами — пінопласти і матеріали із сполученими порами — поропласти.
Як вихідні речовини для виготовлення легких пластмас застосовують полівінілхлорид, ефіри, целюлози, фенопласти, амінопласти, поліефіри та ін. До складу композиції, яка містить один з цих термопластичних полімерів, як газоутворювачі вводять вуглекислий амоній, бікарбонат натрію тощо.
Поро - і пінопласти використовують для звукоізоляції і як теплоізоляційний матеріал.
Способи виготовлення виробів Із пластмас. Найчастіше застосовують такі способи виготовлення виробів із пластмас: пресування, лиття під тиском, екструзію, каландрування, обробку різанням та ін.
Для пресування виробів із пластмаси використовують гідравлічні або механічні преси потужністю 25...200 τ і спеціально виготовлені прес-форми.
Прес-форма повинна мати порожнину у матриці 3, яка заповнюється прес-матеріалом. Прес-форми бувають відкриті (рис. а) і закриті (рис. б).

Пресуванням одержують вироби з порошків або таблеток термореактивних полімерів: фенопластів, амінопластів та ін.
О — у відкритій прес-формі; б — у закритій прес-формі
Пресувальний матеріал під дією пуансона 1 (під тиском) надходить у нагріту прес-форму. У прес-формі закритого типу надлишок прес-матеріалу при пересуванні витискується виштовхувачем 4 і спрямовується вгору по канавках на пуансоні.
Прес-форми виготовляють з інструментальних вуглецевих або легованих сталей.
Лиття під тиском (рис. ) забезпечує високу продуктивність (15...20 тис. виробів за зміну).
Залежно від типу термопластичної маси і форми виробів значення тиску змінюється (40...80 МПа).
Лиття під тиском — найпродуктивніший спосіб виготовлення виробів із термопластов. Гранули полімеру з бункера 1 (рис. 2.49, а) надходять у циліндр 2 дозатора. Поршень З подає певну порцію пластмаси в приймальну камеру циліндра. Тут гранули нагріваються (160...200 °С) гарячою парою, що підводиться трубкою 7. Розплавлена пластмаса витискується крізь отвір 4 у порожнину 6 рознімної прес-форми 5, яка охолоджується по каналах водою.
Цим способом виготовляють вироби високого ступеня точності. Процес формування виробу з матеріалу відбувається дуже швидко: один цикл у звичайних ливарних машин триває 20...30 с, а в швидкісних — 3...5 с. Усі операції механізовано і керуються спеціальним реле часу.
Екструзія (видавлювання) — спосіб переробки нагрітих до пластичного стану термопластів безперервним видавлюванням крізь отвір у мундштуку. Цей спосіб застосовують для виготовлення фасонних стрижнів, труб, шлангів та ін.

Каландрування застосовують для виготовлення плівок і тонких листів завтовшки до... 1,0 мм. Плівку виготовляють з твердого полівінілхлориду, який нагрівають і обтискують вальцями, внаслідок чого він перетворюється на пластичну масу. Цю масу пропускають (під високим тиском) через нагріті валки, і вона набуває вигляду плівки. Далі ця (ще пластична) плівка проходить через холодильні валки і твердне. її розрізують по ширині і змотують у рулон.
Обробку пластмас різанням застосовують для виготовлення деталей із пластмас, які поставляють у вигляді напівфабрикатів (профілів, труб, плит та ін.). Пластмаси зазнають усіх видів обробки різанням.
Паливо, що застосовується для автомобілів.
1.1. Загальна характеристика палива. Класифікація
Паливом називають горючу речовину, яку спеціально
спалюють для одержання тепла і подальшого його використання
для інших потреб у сільськогосподарському виробництві. Воно
повинно мати певні властивості, тобто відповідати таким
основним вимогам: порівняно легко займатися; при згорянні
виділяти якомога більше теплоти; бути поширеним у природі,
доступним при видобуванні та дешевим при виробництві; не
змінювати свої властивості при транспортуванні та зберіганні;
бути нетоксичним і при згорянні не виділяти шкідливих та
отруйних речовин.
Цим вимогам найбільш повно відповідають речовини
органічного походження: нафта, природний газ, тверді горючі
копалини тощо.
Палива класифікують за такими основними ознаками:
агрегатним станом, походженням і способом одержання,
тепловою цінністю, цільовим призначенням або застосуванням.
За агрегатним станом всі види палива поділяють на тверді,
рідкі і газоподібні.
За походженням палива ділять на нафтові і альтернативні.
До альтернативних палив належать спирти, водень і майже всі
види штучних вуглеводних палив.
За способом одержання палива бувають природні, які
використовують у тому вигляді, в якому вони існують у
природі, і штучні, якщо після видобутку їх переробляють.
За тепловою цінністю, тобто тепловою згоряння, палива
класифікують на висококалорійні, середньо - і низькокалорійні.
За цільовим призначенням паливо розрізняють: паливо
для двигунів з примусовим запалюванням, реактивні і дизельні
палива. Для двигунів з примусовим запалюванням відносять
бензин і газоподібне паливо. Дизельне паливо виготовляють для
швидкохідних двигунів (автомобільних, тракторних тощо), для
середньо - і тихохідних двигунів (судових і стаціонарних).
У сільському господарстві застосовують всі види палив:
рідке – яке забезпечує роботу сільськогосподарської техніки,
стаціонарних двигунів та інших теплових установок сільськогосподарського виробництва (дизель-електростанцій з двигунами внутрішнього згоряння, котельні установки тощо); газоподібне – у газобалонних автомобілях і газогенераторних установках, для технологічних і побутових потреб; тверде – для різних
виробничих і побутових потреб.
Поняття «паливо» є категорія не тільки технічна, а й
економічна та екологічна, оскільки у кожному конкретному
випадку його використання має бути ефективним. До того ж,
при спалюванні палива необхідно створювати умови для
якомога меншого забруднення навколишнього середовища.
1.2. Склад палива
Будь-яке паливо складається з двох основних частин:
горючої і негорючої (баласту). Горюча частина містить різні
органічні сполуки, до яких входять такі хімічні елементи:
вуглець (С), водень (Н), сірка (S), кисень (О), азот (N), а також ті
неорганічні сполуки, які під час горіння палива, розкладаючись,
утворюють легкі речовини.
Склад твердого і рідкого палива визначається у процентах
за масою, газоподібного – у процентах за об’ємом.
Вуглець – основа горюча складова, із збільшенням частки
якої зростає теплова цінність палива. Вміст вуглецю у різних видах палива коливається у межах від 50% (дрова) до 98%
(антрацит).
Водень за теплотою згоряння майже у 4 рази цінніший ніж
вуглець. Враховуючи, що вміст водню в паливі складає до 25% -
це друга за значимістю складова частини палива.
Кисень, що входить в склад палива, не горить і тому
фактично є внутрішнім баластом горючої частини. Вміст кисню
становить від 0,5% до 43%. Чим більше в горючій частині
кисню, тим менш цінне паливо.
Азот, як і кисень, не горить, є внутрішнім баластом
горючої частини. У твердому і рідкому паливі вміст азоту
невеликий (0,5...1,5%) і тому вплив його на теплову цінність
палива незначний. Однак, у деякому газоподібному паливі
(наприклад, генераторному газі) вміст азоту становить біля 50%,
що різко знижує його теплову цінність.
Сірка є горючим елементом і, входячи до складу палива у
вільному стані або у вигляді органічних і сульфідних сполук,
бере участь у горінні. Але не зважаючи на це, сірка є дуже
небажаною складовою палива тому, що під час горіння сірки
утворюються сполуки SO2, SO3, які викликають газову корозію,
а з’єднуючись з вологою, яка завжди є у паливі,
перетворюються у сірчисту та сірчану кислоти, які викликають
рідину корозію металів. Вміст сірки у твердому паливі
коливається від 0,01 до 8%, а у нафтах – від 0,1 до 4%. При
переробці палива намагаються вміст сірки за можливістю
довести до мінімуму.
Негорюча частина у твердому і рідкому паливі
складається з мінеральних домішок (при згорянні утворюють
золу А) і вологи W. Ця частина, зменшуючи об’єм горючої
частини і відбираючи частину теплоти на своє нагрівання,
знижує теплову цінність палива. Крім того зола прискорює
абразивне спрацювання деталей циліндро-поршневої групи
двигунів, а волога збільшує корозію та ускладнює експлуатацію
установок взимку.
Вміст мінеральних домішок у рідкому паливі вимірюється
десятими частинами процента, а у твердому – десятками
процентів. Мінеральні домішки і вологу розділяють на зовнішні
та внутрішні.
Перші – потрапляють у паливо з навколишнього
середовища при його добуванні, транспортуванні, зберіганні,
другі – входять до його хімічного складу.
Залежно від фізичного стану палива, при якому визначають його елементарний склад, розглядають маси: робочу (р),
аналітичну (повітряно-суху, лабораторну) (а), суху (с), горючу
(г) і органічну (о).
Паливо, яке надходить до споживачів у природному стані
та містить, крім горючої частини, золу і вологу, називають
робочим. Елементарний склад палива виражають рівнянням
СР + НР + ОР + NР + SР + АР + WР = 100% (1.1)
У тих випадках, коли паливо піддають лабораторному
дослідженню, з нього готують аналітичну пробу, яку приводять
для повітряно-сухого стану. При цьому паливо містить тільки
внутрішню вологу.
Суха маса не має вологи, оскільки вона одержана
штучним сушінням при температурі 105 о
С. Горюча маса – це паливо, що не має вологи і золи. А якщо
з палива видалити ще і сірку, то отримують органічну масу.
Зальний склад палива для різного його стану схематично
показаний на рис. 1.1.
Елементарний склад палива розраховують
на горючу і суху маси, а всі теплові розрахунки ведуть на
робочу (дійсну) масу, склад якої залежить від кількості золи і
вологи.
Горюча частина газоподібного палива включає: водень
(Н), оксид вуглецю (СО), метан (СН4), та інші вуглеводні (СnНm)
з числом атомів вуглецю до чотирьох. Негорюча частина – пари
води і негорючі гази (СО2, N2, O2).
З моменту появи автомобільних двигунів внутрішнього згоряння та до сих пір для них використовуються продукти нафтопереробки: бензин чи дизельне паливо. І те, і те – суміш вуглеводнів з присадками. Різниця тільки в окремих характеристиках та температурному режимі. Від 35 до 2000 градусів для бензину чи від 180 до 3600 – для дизеля.
Бензин
Бензин – легкокиплячі рідкі вуглеводні, які виділяються при переробці твердого палива, перегонці нафти, осушування природного газу. Основний критерій – детонаційна стійкість, яка характеризується октановим числом. Чим воно вище – тим вища стійкість бензину до детонації. Найгірші показники у парафінових вуглеводнів, а найкращі – у ароматичних. Для поліпшення властивостей вводяться спеціальні присадки.
Другий важливий критерій – ступінь стиснення. Чим вона вища – тим вища потужність двигуна, але і більша витрата палива. Важливо, щоб ступінь стиснення і октанове число корелювали між собою.
Фракційний склад бензину безпосередньо впливає на пуск двигуна, прогрів, економічність, довговічність і відсутність парових пробок. Виходячи з цього, бензини класифікують на зимові та літні: адаптовані під конкретні температурні умови.
Дизельне паливо
Дизельні палива – це продукт на основі фракцій дистилятів при прямій перегонці нафти. Основні компоненти – цетан і метилнафталін. Це легко займиста рідина і погано займиста добавка. Займистість – головна характеристика, яка виражається в цетановому числі. Це аналог октанового числа для бензину.
Здатність дизеля до прокачки визначає його здатність циркулювати по системі. Вона залежить від граничної температури фільтрування, температури помутніння та застигання. Також потрібно враховувати наявність води чи механічних домішок.
Альтернативні види
У всьому світі зростає інтерес до альтернативних видів автомобільного палива: більш економічних, екологічних і ефективних. Вони виробляються з невичерпних запасів і створюють менше викидів в атмосферу.
Ось деякі з них:
- Природний газ. Доступний практично повсюди, виділяє менше токсичних речовин, ніж бензин або дизель, повністю згорає при використанні.
- Електрика. Електрокари на акумуляторах удосконалюються з кожним роком. Для зарядки вони підключаються до джерела живлення. Електрохімічна реакція в двигуні не забруднює навколишнє середовище.
- Пропан. Зріджений нафтовий газ – побічний продукт нафтопромисловості. Його вже використовують в побуті і для опалювальних систем.
- Водень. Він використовується в системах з природним газом і електричних паливних елементах.
- Метанол. Деревний метиловий спирт поки не придатний для використання в автомобілях, але з часом може стати перспективним альтернативним джерелом.
- Етанол. Етиловий спирт змішується з бензином для підвищення октанового числа палива та мінімізації токсичних викидів.
- Біодизель. Виготовлений на основі рослинних або тваринних жирів, включаючи відходи харчової промисловості. Піддається біохімічномурозкладу.
Більш детально ви зможете отримати іформацію з даної теми перейшовши за посиланням http://library.kr.ua/elib/chabannyi/Chabannyi_Pal_mast_Mater_kn1.pdf та вивчити матеріал посібника з даної теми
http://www.tsatu.edu.ua/tstt/wp-content/uploads/sites/6/lekcija-9-zmashchuvalni-materialy-z-dyscypliny-trybotehnika-133-hm.pdf
http://library.kr.ua/elib/chabannyi/Chabannyi_Pal_mast_Mater_kn2.pdf
До основних фізичним властивостям відносяться щільність, електро- і теплопровідність, намагніченість, температура плавлення, температурні коефіцієнти лінійного і об'ємного розширення та ін.
До механічним властивостям матеріалу відносяться міцність, пластичність, твердість, повзучість, ударна в'язкість, втома, зносостійкість.
Міцність - здатність твердого тіла пручатися деформації або руйнуванню під дією статичних або динамічних навантажень.
Твердість - здатність матеріалу чинити опір впровадженню в нього іншого, який не одержує залишкової деформації, тіла.
Пластичність - здатність матеріалу отримувати залишкове (залишається після видалення навантаження) зміна форми і розмірів без руйнування. Характеристикою пластичності є відносне подовження і звуження випробуваного зразка.
Ударна в'язкість - це міцність при динамічних навантаженнях, Дж / м2:
де А - робота, витрачена на руйнування зразка; F - площа зразка в місці надрізу.
Повзучість - властивість матеріалу повільно деформуватися під дією постійно розтягує навантаження, яка створює напругу нижче межі пружності даного матеріалу.
Втома матеріалу - властивість поступового накопичення пошкоджень в матеріалі під дією циклічних навантажень, що призводять до утворення тріщин і руйнування. Властивість матеріалів опиратися втоми називається витривалість опором втоми). Опір втоми характеризується межею витривалості.
Межа витривалості це найбільше напруження, яке матеріал може витримати без ознак руйнування після заданого числа нагружений знакозмінним вигином або іншим видом деформації при закріпленні випробуваного зразка одним кінцем.
Одним з показників опору втоми є живучість під якою розуміють довговічність деталі від моменту зародження перших макроскопічної тріщини втоми розміром 0,5-1,0 мм до остаточного руйнування.
Технологічні властивості характеризуються здатністю матеріалу здобувати задану форму під дією різних факторів (температури, тиску та ін.), Піддаватися механічній обробці, з'єднуватися різними методами (зварюванням, склеюванням) і т.д. Звідси випливає, що вони мають важливе значення при виборі способу виготовлення деталей, так як повинні забезпечити можливо меншу трудомісткість конструкцій.
До технологічних властивостей матеріалів відносяться ливарні властивості (жидкотекучесть, усадка, схильність до ліквації), деформованість, зварюваність і оброблюваність ріжучим інструментом.
Вологотекучість здатність розплавленого матеріалу заповнювати ливарну форму.
Усадка - зменшення лінійних розмірів (обсягу) залитого в форму матеріалу в процесі охолодження виливки.
Ліквація - сегрегація, неоднорідність хімічного складу сплаву, що виникає при його кристалізації.
Плинність - здатність порошку заповнювати прес-форму.
Спікливість - міцність зчеплення частинок в результаті термічної обробки пресованих заготовок.
Прессуемость здатність порошку ущільнюватися під дією зовнішнього навантаження і забезпечувати високу міцність зчеплення частинок після пресування.
Зварюваність - здатність матеріалу давати міцне нероз'ємне з'єднання при нагріванні зварювальних кромок до температури плавлення або сказу і додатки певного тиску (ударів або стиснення).
Деформируемость (ковкість) - здатність матеріалу приймати необхідну форму під дією зовнішнього навантаження без руйнування і при найменшому опорі.
Прожарювана - здатність металу сприймати загартування на деяку глибину від поверхні.
Оброблюваність - здатність матеріалу піддаватися обробці різанням. Критеріями оброблюваності є режими різання і якість поверхневого шару.
До експлуатаційних відносяться властивості матеріалу, що безпосередньо впливають на показники, що характеризують цільове призначення виробу.
Корозійна стійкість - опір матеріалу дії агресивних середовищ (кислотних, лужних і т.п.).
Хладостойкость - здатність матеріалу зберігати необхідні пластичні властивості при низьких робочих температурах.
Жароміцність - здатність матеріалу зберігати необхідні механічні властивості при високих робочих температурах.
Жаростійкість - здатність матеріалу чинити опір окисленню в газовому середовищі при високих температурах.
Антифрикційність здатність матеріалу прірабативала по труться до іншого матеріалу.
Зношуваність - властивість матеріалу змінювати розміри, форму, руйнувати поверхневий шар або змінювати стан його поверхні внаслідок залишкової деформації від постійно діючих навантажень при терті сполучених поверхонь.
Зносостійкість - здатність матеріалу чинити опір зношуванню, що оцінюється величиною зворотною швидкості зношування.
http://bia.ucoz.ua/index/materialoznavstvo_radioelektronnikh_zasobiv/0-91
Перейдіть за посиланням, опрацюйте матеріал з даної теми
http://www.ea.donntu.org:8080/bitstream/123456789/27907/1/%D0%91%D0%9C_%D0%9A%D0%BE%D0%BD%D1%81%D0%BF%D0%B5%D0%BA%D1%82.pdf
Мастильні матеріали, що застосовуються в механізмах автомобілів. їхні основні характеристики.
Перейдіть за посиланням, опрацюйте матеріал з даної темиhttp://www.tsatu.edu.ua/tstt/wp-content/uploads/sites/6/lekcija-9-zmashchuvalni-materialy-z-dyscypliny-trybotehnika-133-hm.pdf
Заходи безпеки під час роботи, зберігання і транспортування паливно-мастильних матеріалів
Перейдіть за посиланням, опрацюйте матеріал з даної темиhttp://library.kr.ua/elib/chabannyi/Chabannyi_Pal_mast_Mater_kn2.pdf
Тема: "Класифікація матеріалів."
Класифікація за механічними властивостями матеріалів.
Матеріали володіють певним набором властивостей. Розрізняють фізичні, хімічні, механічні, технологічні та експлуатаційні властивості матеріалів, які зумовлюють їх застосування в тій чи іншій галузі промисловості.До основних фізичним властивостям відносяться щільність, електро- і теплопровідність, намагніченість, температура плавлення, температурні коефіцієнти лінійного і об'ємного розширення та ін.
До механічним властивостям матеріалу відносяться міцність, пластичність, твердість, повзучість, ударна в'язкість, втома, зносостійкість.
Міцність - здатність твердого тіла пручатися деформації або руйнуванню під дією статичних або динамічних навантажень.
Твердість - здатність матеріалу чинити опір впровадженню в нього іншого, який не одержує залишкової деформації, тіла.
Пластичність - здатність матеріалу отримувати залишкове (залишається після видалення навантаження) зміна форми і розмірів без руйнування. Характеристикою пластичності є відносне подовження і звуження випробуваного зразка.
Ударна в'язкість - це міцність при динамічних навантаженнях, Дж / м2:
де А - робота, витрачена на руйнування зразка; F - площа зразка в місці надрізу.
Повзучість - властивість матеріалу повільно деформуватися під дією постійно розтягує навантаження, яка створює напругу нижче межі пружності даного матеріалу.
Втома матеріалу - властивість поступового накопичення пошкоджень в матеріалі під дією циклічних навантажень, що призводять до утворення тріщин і руйнування. Властивість матеріалів опиратися втоми називається витривалість опором втоми). Опір втоми характеризується межею витривалості.
Межа витривалості це найбільше напруження, яке матеріал може витримати без ознак руйнування після заданого числа нагружений знакозмінним вигином або іншим видом деформації при закріпленні випробуваного зразка одним кінцем.
Одним з показників опору втоми є живучість під якою розуміють довговічність деталі від моменту зародження перших макроскопічної тріщини втоми розміром 0,5-1,0 мм до остаточного руйнування.
Технологічні властивості характеризуються здатністю матеріалу здобувати задану форму під дією різних факторів (температури, тиску та ін.), Піддаватися механічній обробці, з'єднуватися різними методами (зварюванням, склеюванням) і т.д. Звідси випливає, що вони мають важливе значення при виборі способу виготовлення деталей, так як повинні забезпечити можливо меншу трудомісткість конструкцій.
До технологічних властивостей матеріалів відносяться ливарні властивості (жидкотекучесть, усадка, схильність до ліквації), деформованість, зварюваність і оброблюваність ріжучим інструментом.
Вологотекучість здатність розплавленого матеріалу заповнювати ливарну форму.
Усадка - зменшення лінійних розмірів (обсягу) залитого в форму матеріалу в процесі охолодження виливки.
Ліквація - сегрегація, неоднорідність хімічного складу сплаву, що виникає при його кристалізації.
Плинність - здатність порошку заповнювати прес-форму.
Спікливість - міцність зчеплення частинок в результаті термічної обробки пресованих заготовок.
Прессуемость здатність порошку ущільнюватися під дією зовнішнього навантаження і забезпечувати високу міцність зчеплення частинок після пресування.
Зварюваність - здатність матеріалу давати міцне нероз'ємне з'єднання при нагріванні зварювальних кромок до температури плавлення або сказу і додатки певного тиску (ударів або стиснення).
Деформируемость (ковкість) - здатність матеріалу приймати необхідну форму під дією зовнішнього навантаження без руйнування і при найменшому опорі.
Прожарювана - здатність металу сприймати загартування на деяку глибину від поверхні.
Оброблюваність - здатність матеріалу піддаватися обробці різанням. Критеріями оброблюваності є режими різання і якість поверхневого шару.
До експлуатаційних відносяться властивості матеріалу, що безпосередньо впливають на показники, що характеризують цільове призначення виробу.
Корозійна стійкість - опір матеріалу дії агресивних середовищ (кислотних, лужних і т.п.).
Хладостойкость - здатність матеріалу зберігати необхідні пластичні властивості при низьких робочих температурах.
Жароміцність - здатність матеріалу зберігати необхідні механічні властивості при високих робочих температурах.
Жаростійкість - здатність матеріалу чинити опір окисленню в газовому середовищі при високих температурах.
Антифрикційність здатність матеріалу прірабативала по труться до іншого матеріалу.
Зношуваність - властивість матеріалу змінювати розміри, форму, руйнувати поверхневий шар або змінювати стан його поверхні внаслідок залишкової деформації від постійно діючих навантажень при терті сполучених поверхонь.
Зносостійкість - здатність матеріалу чинити опір зношуванню, що оцінюється величиною зворотною швидкості зношування.
Класифікація матеріалів за електропровідністю.
Перейдіть за посиланням, опрацюйте матеріал з даної темиhttp://bia.ucoz.ua/index/materialoznavstvo_radioelektronnikh_zasobiv/0-91
Класифікація за фізико-хімічними властивостями матеріалів
Фізичні властивості матеріалу характеризують його відношення до фізичних процесів навколишнього середовища і визначаються параметрами стану матеріалу. До параметрів стану матеріалу відносять такі технічні характеристики:
істинна щільність (г/см3, кг/м3) – маса одиниця об'єму абсолютно щільного матеріалу. Якщо маса матеріалу m, а його обсяг Vа – його обсяг у щільному стані, то
= m/Vа;
середня щільність о (г/см3, кг/м3) – маса одиниці об'єму матеріалу в природному стані ( з порами і дефектами):
о = m/V.
Середня щільність матеріалу завжди менше істиною щільності. Наприклад: середня щільність легкого бетону – 500-1800 кг/м3, а його істинна щільність – 2600 кг/м3;
відносна щільність d виражає щільність матеріалу стосовно щільності води і є безрозмірною величиною;
насипна щільність н (г/см3 ,кг/м3) – маса одиниці об'єму пухко насипаних зернистих чи волокнистих матеріалів (цемент, пісок, щебінь і т.д). Якщо маса матеріалу m , а Vн – його обсяг у пухко насипному стані, то
н = m/Vн;
пористість П – є ступінь заповнення матеріалу порами.
Пористість виражають у % чи частках одиниці.
При експериментально-розрахунковому методі визначення пористості використовують значення істинної й середньої пористості:
П=(1 – ρо/ρ )100%.
Значення пористості будівельних матеріалів коливається від 0 до 98%. Наприклад, пористість важкого бетону – 10%; цегли звичайної – 32%; природних кам'яних матеріалів магматичного походження – 1,4%; міпори (спінених полімерів) – 98% (табл. 1.1).
Таблиця 1.1 - Значення істинної й середньої щільності, пористості для деяких будівельних матеріалів
Матеріал
|
Щільність, кг/м3
|
Пористість ,%
| ||
середня
|
істинна
| |||
Граніт
|
2600…2700
|
2700…2800
|
0…2
| |
Важкий бетон
|
2200…2500
|
2600…2700
|
2…25
| |
Цегла
|
1400…1800
|
2500…2600
|
25…35
| |
Деревина
|
400…800
|
1500…1550
|
45…70
| |
Пінопласт
|
15…100
|
950…1200
|
90…98
|
Гігроскопічність – здатність матеріалів поглинати вологу з повітря. Залежить від хімічного складу матеріалу і характеру його пористості.
Вологість матеріалу визначається вмістом вологи, віднесеної до маси матеріалу в сухому стані, залежить як від властивостей самого матеріалу, так і від навколишнього середовища. Вологість впливає на теплопровідність, стійкість до гниття і т.д.
Водопоглинення – здатність матеріалу всмоктувати й утримувати воду.
Розрізняють водопоглинення за масою і об’емом :
Wm = [(m1 – m)/m] · 100%;
Wv = [(m1 – m)/v] · 100%,
де m1 - маса зразка, насиченого водою;
m - маса сухого зразка.
Водопроникність – це властивість матеріалу пропускати воду під тиском. Водопроникність характеризується коефіцієнтом фільтрації Кф (м/г):
Кф = Vв · a/(S(р1-р)t),
де Vв – кількість води (м3), що проходить через стінку площею S = 1 м2, товщиною а = 1 м, за час t = 1 год. при різниці гідростатичного тиску на межах стінки р1-р=1 м вод ст.
Коефіцієнт розм'якшення – Кр – відношення міцності матеріалу, насиченого водою Rв, до міцності сухого матеріалу Rс:
Кр = Rв/Rс.
Коефіцієнт розм'якшення характеризує водостійкість матеріалу, він змінюється від 0 (розмокла глина) до 1 (метали). Якщо коефіцієнт розм'якшення менше 0,8, то матеріали не застосовують у будівельних конструкціях, що знаходяться у воді.
Морозостійкість – властивість насиченого водою матеріалу витримувати поперемінно заморожування і відтавання. Морозостійкість матеріалу кількісно оцінюється циклами і відповідно маркою за морозостійкістю. За марку матеріалу по морозостійкості приймають найбільше число циклів поперемінно заморожування і відтавання, що витримують зразки матеріалу без зниження міцності на стиск більше 15%; втрати маси більше 5%.
Теплопровідність – властивість матеріалу передавати тепло від однієї поверхні до іншої. Характеристикою теплопровідності є коефіцієнт теплопровідності λ (Вт/м оС) На практиці зручно судити про теплопровідність за щільністю матеріалу.
Зазначена залежність виражається формулою В.П. Некрасова:
λ =1,16
,

де d – відносна щільність матеріалу.
Теплоємність – здатність матеріалу акумулювати тепло при нагріванні і виділяти тепло при остиганні;
Вогнестійкість – властивість матеріалу витримувати тривалий вплив високої температури (від 1580 оС), не розм'якшуючись і не деформуючись.
Вогнестійкість – властивість матеріалу пручатися дії вогню при пожежі протягом певного часу, залежить від здатності матеріалу спалахувати і горіти.
http://www.ea.donntu.org:8080/bitstream/123456789/27907/1/%D0%91%D0%9C_%D0%9A%D0%BE%D0%BD%D1%81%D0%BF%D0%B5%D0%BA%D1%82.pdf
Немає коментарів:
Дописати коментар