Група 07-18
Хіміко-термічна обробка сталі.
8.1. Загальні відомості
Багато виробів повинні мати високу поверхневу твердість, міцний поверхневий шар і в’язку серцевину. Таке сполучення властивостей досягається поверхневим зміцненням виробів, котрі виготовлені із сталей з доброю пластичністю і задовільною міцністю. До методів поверхневого зміцнення відносять ХТО, поверхневе гартування та поверхневу пластичну деформацію.
8.1.1 Хіміко-термічна обробка - це процеси дифузійного насичення поверхневого шару виробів із зовнішнього середовища різними елементами одночасно із тепловим впливом.
ХТО - один із найбільш ефективних методів підвищення довговічності деталей машин завдяки збільшенню твердості, опору зношуванню, границі витривалості, контактної витривалості, а в деяких випадках - антикорозійних, антиерозійних властивостей та окалино- (жаро)стійкості.
Після ХТО змінюється хімічний і фазовий склад, структура, та як наслідок цього - властивості поверхневого шару. Дифузійне насичення металів і сплавів можливо лише при підвищеній температурі, коли стає помітною дифузія атомів елемента, що насичує поверхню. Для зміни хімічного складу виробів їх нагрівають в активному середовищі і при цьому одночасно відбуваються такі процеси: утворення елемента в активному (атомарному) стані; адсорбція атомів поверхнею виробів; дифузія атомів від поверхні у глибину виробу.
Основні кількісні характеристики дифузійного шару - його глибина, концентрація елемента, твердість поверхні. При ХТО глибина шару залежить від багатьох факторів: природи елемента, що насичує; його активності в робочому середовищі; тривалості та температури насичення; хімічного складу сталі. Наприклад, при насиченні елементами, котрі утворюють тверді розчини втілення, швидкість формування шару в багато разів вища, ніж при утворенні твердих
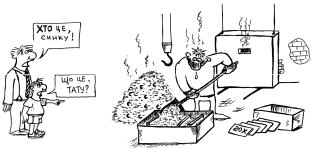
82
розчинів заміщення, тому що дифузійна рухомість атомів втілення на декілька порядків вища рухомості атомів заміщення. Підвищення температури насичення при однаковій тривалості приводить до збільшення глибини дифузійного шару за експонентою і на практиці використовується як один із методів інтенсифікації процесів ХТО.
У залежності від стану речовини - постачальника атомів насичення, розрізняють насичення із газової (парової), рідкої або твердої фази.
Окрім того, всі різновиди ХТО поділяють на дві групи: 1)
дифузійне насичення неметалами: цементація (насичення вуглецем), ціанування (вуглецем і азотом), азотування (азотом); 2) дифузійне насичення металами (дифузійна металізація) - хромом, алюмінієм, кремнієм, титаном тощо. Найбільш поширене промислове використання знайшли методи насичення неметалами.
Цементація - процес дифузійного насичення вуглецем поверхневих шарів сталевих виробів. Цементовані вироби повинні мати поверхневу твердість ³56HRC, підвищену зносостійкість поверхні та в’язку серцевину. Тому для їх виготовлення використовують маловуглецеві (0,1...0,25 %С) сталі: 10, 15, 20, 15Х, 18ХГТ, 12ХНЗА, 18Х2Н4А та інші.
Розчинність вуглецю у фериті незначна, тому цементацію сталі проводять в аустенітному стані (при температурі вище Ас3 для цементовної сталі). Інтервал температур цементації складає 870...1050° С. Підвищення температури цементації приводить до росту аустенітного зерна, погіршенню механічних і експлуатаційних властивостей шару і серцевини. Оптимальним поверхневим вмістом вуглецю у шарі вважається 0,8...1,1 %. При меншому вмісті вуглецю не досягається необхідна твердість поверхні, а при більшому - в цементованому шарі утворюється карбідна сітка, внаслідок чого він стає крихким.
83
Глибина шару частіше за все знаходиться в межах 0,6...1,3 мм; на деталях зі значними розмірами вона може досягати 4...6 мм. За рівних умов підвищення температури цементації скорочує тривалість насичення. Наприклад, тривалість процесу для досягнення глибини 1 мм в сталі 10 при 900° С становить 6 годин, а при 970 ° С – 4...5 годин.
Речовини - постачальники вуглецю при цементації називаються карбюризаторами. У залежності від виду карбюризатору розрізняють цементацію у твердому карбюризаторі і газову цементацію.
Твердий карбюризатор складається із суміші деревного вугілля та вуглекислих солей. Деталі складають в спеціальні сталеві ящики, пересипають карбюризатором, герметизують, щоб зменшити доступ повітря, і завантажують у нагріту піч. При нагріванні внаслідок взаємодії деревного вугілля і залишку кисню утворюється оксид вуглецю СО, який на поверхні металевих виробів дисоціює за реакцією 2СО→С+СО2 з утворенням атомарного вуглецю. Останній “ поглинається” металом, а СО2 після взаємодії з деревним вугіллям відновлюється до СО.
При газовій цементації використовують як карбюризатор спеціально приготовлену суміш газів (ендогаз); природний газ; рідкі вуглеводні - гас, синтин, піробензол. Деталі у спеціальних пристроях завантажуються в цементаційні печі, в котрих природний газ і органічні рідини дисоціюють з утворенням атомарного вуглецю, наприклад,
СН4→С+2Н2.
Газова цементація має низку переваг порівняно з цементацією у твердому карбюризаторі: можливі механізація і регулювання насичення; менша тривалість процесу. У зв’язку з цим газова цементація використовується в масовому та серійному виробництві.
Після цементації максимальний вміст вуглецю на поверхні виробів плавно зменшується в перерізі деталі від поверхні до початкового вмісту в серцевині. Наприклад, в цементованій деталі із сталі 10 концентрація вуглецю зменшується від 1,0 % на поверхні до 0,1 % в серцевині. Структура деталей, повільно охолоджених після цементації, близька до рівноважної і залежить від вмісту вуглецю: в заевтектоїдній частині шару - перлит із сіткою вторинних карбідів, в евтектоїдній - перлит, в доевтектоїдній - перлитоферитна із зростанням частки фериту в напрямку до серцевини. Зазначені структури мають низький рівень твердості, тому лише однієї цементації недостатньо для досягнення значної поверхневої твердості та високих експлуатаційних властивостей.
84
Вони забезпечуються завершальною термічною обробкою - гартуванням та відпусканням. У залежності від марки цементовної сталі, температури цементації, призначення деталей і т. ін., можливі такі основні технологічні схеми:
-цементація, повільне охолодження, гартування від температури
Ас1+(30...50)°С, відпускання низькотемпературне (ХТО для маловідповідальних деталей);
-цементація, повільне охолодження, подвійне гартування, відпускання низькотемпературне (для важконавантажених деталей
відповідального призначення), перше гартування (температура вище Ас3) використовують для перекристалізації та подрібнення зерен в серцевині, що виросли при високих температурі і тривалості цементації, а також розчинення цементитної сітки в заевтектоїдній зоні шару. Друге
гартування (температура Ас1+(30...50)°С) забезпечує дрібнозернисту структуру шару та збереження дрібних глобулярних карбідів в заевтектоїдній частині шару;
-цементація, охолодження в печі до температури гартування сталі
(Ас1+(30...50)°С), гартування (так зване гартування з цементаційного нагрівання), відпускання низькотемпературне.Використовується для спадководрібнозернистих сталей, що зберігають після тривалої цементації зерно в серцевині і в шарі не більше 7 балу. Ця технологія використовується після газової цементації; її головні переваги - виключення повторного нагрівання, зменшення деформації деталей, збереження енергоносіїв.
Структура цементованого шару після термічної обробки - мартенсит відпущений, аустеніт залишковий, карбіди; структура серцевини - феритоперлитна (вуглецеві сталі), маловуглецевий відпущений мартенсит із феритом (леговані сталі), що пояснюється підвищеною прогартовуваністю легованих сталей. Після ХТО твердість
поверхні цементованих сталей HRC³56, серцевини HRC20...45 (в залежності від хімічного складу сталі, розмірів деталі, структури серцевини). Швидкість цементації становить 0,1...0,2мм/год.
Методи поверхневого зміцнення, зокрема цементація, підвищують міцність, границю витривалості, опір руйнуванню виробів, зумовленого втомою металу, що виникає під дією контактних напружень. Тріщина втоми зароджується і розвивається під дією напружень розтягу. У зміцненому поверхневому шарі, що має більший питомий об’єм
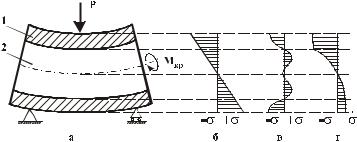
85
порівняно із серцевиною, виникають напруження стиснення (рис. 8.1, в). Внаслідок взаємодії напружень від навантаження і зміцнення (рис. 8.1, г) зменшується рівень напружень розтягу і підвищується опір втомі сталі, довговічність деталей.
Рисунок 8.1 - Схема навантаження деталі типу вал (а) та епюри напружень від
навантаження (б), поверхневого зміцнення (в), спільної дії навантаження і зміцнення(г)
Азотування - процес дифузійного насичення поверхні виробів азотом. Мета азотування - підвищити твердість, зносостійкість, границю витривалості та опір корозії.
В сплавах системи Fe-N (рис. 8.2) утворюються наступні фази: α-фаза - твердий розчин втілення азоту в α-Fe з граткою ОЦК; γ-фаза - твердий розчин втілення азоту в γ-Fe з граткою ГЦК; γ′-фаза - твердий розчин на основі нітриду Fe4N з ГЦК граткою. ε-фаза - твердий розчин на основі нітриду Fe3N з граткою ГЩП. Твердість нітридів заліза відносно невисока: γ′-фази – HV 550
(HRC 50); ε-фази – HV 450 (HRC 44) . Тому твердість вуглецевих сталей після азотування не перевищує HV600 і для азотування використовують леговані алюмінієм, ванадієм та хромом сталі. В них, окрім нітридів AlN, VN, Cr2N, для яких характерна висока твердість, є зони з підвищеним вмістом азоту і легувальних елементів, що створюють пружні викривлення гратки α-твердого розчину. Високодисперсні нітриди легувальних елементів та збагачені азотом, алюмінієм, ванадієм та хромом зони гальмують рух дислокацій і підвищують твердість азотованого шару легованих сталей (НV 1000...1200).
Азотування конструкційних сталей проводиться при температурах нижче 591° С - температури евтектоїдного перетворення в системі Fe-N. Використовують середньовуглецеві (0,3...0,45 %С) леговані сталі 38Х2МЮА, 30Х2Н2МФА, 40ХНМ та ін. Перед азотуванням деталі проходять поліпшення (гартування і високотемпературне відпускання),
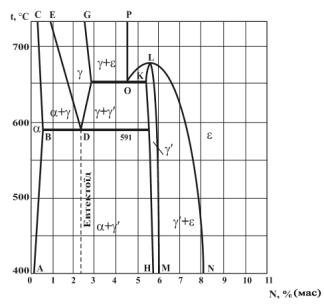
86
щоб забезпечити в’язку серцевину і підготувати структуру до азотування. Азотування при 520...560 ° С дозволяє сформувати шар 0,3...0,6 мм за 30...60 годин, тобто швидкість азотування складає 0,01 мм/год. Атомарний азот для насичення утворюється при дисоціації аміаку
2NH3→2N+3H2.
Після насичення деталі охолоджуються з піччю в атмосфері аміаку до 150...200° С, а потім на повітрі. Висока твердість азотованого шару забезпечується утворенням твердого розчину втілення азоту в α-Fe і , головним чином, нітридами легувальних елементів. Тому після азотування термічна обробка не виконується.
Рисунок 8.2 - Фрагмент діаграми стану системи Fe-N
Переваги азотування порівняно із цементацією: більша твердість поверхні, яка зберігається при нагріванні до 500° С (твердість цементованих виробів знижується при нагріванні вище 200° С); підвищені зносостійкість, границя витривалості, кавітаційна стійкість; опір корозії в повітряній атмосфері, прісній воді і її парі; незначна деформація виробів.
Недоліки азотування: повільна швидкість насичення; підвищена крихкість азотованого шару.
8.1.2 Поверхневе гартування. Поєднання високої поверхневої твердості, міцності та в’язкої серцевини, окрім ХТО, досягається
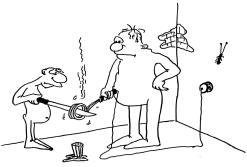
87
поверхневим гартуванням після газополуменевого, електроннопроменевого або плазмового нагрівання та нагрівання струмом високої частоти (СВЧ). При нагріванні СВЧ використовується явище нерівномірності розподілу змінного струму за перерізом виробу: при високих частотах струм практично проходить тільки в поверхневому шарі деталі, розігріваючи його до температур гартування.
Деталь, що підлягає поверхневому гартуванню, розташовують в індукторі (один чи декілька витків водоохолоджуваної мідної трубки), який повторює форму деталі. Змінний струм, що проходить через індуктор, створює змінне магнітне поле, яке зумовлює виникнення в деталі змінного струму. З підвищенням частоти змінного струму зменшується глибина нагрітого (а потім і загартованого) шару. Наприклад, при частоті струму (0,5...1) кГц загартований шар становить
(5...6) мм, при (60...250) кГц - менше 1 мм.
Завдяки великій швидкості нагрівання (100...1000 ° С/с), нетривалій витримці при температурі гартування досягається дрібнозерниста структура, мікронеоднорідність аустеніту за вмістом вуглецю, що дозволяє підвищити на 1...3 HRC твердість загартованої сталі після нагрівання СВЧ порівняно із гартуванням після об’ємного нагрівання.
Для зміцнення використовують середньовуглецеві сталі (0,3...0,5%С): 35, 45, 50, 40Х, 40ХН та ін. При меншому вмісті вуглецю не забезпечуються вимоги щодо твердості поверхні (HRC³55); при більшому - серцевина буде мати низьку в’язкість. Перед поверхневим гартуванням здійснюють нормалізацію чи поліпшення, які забезпечують необхідні властивості серцевини. Після нагрівання СВЧ деталі охолоджуються водою в гартівній ванні або за допомогою спеціального пристрою, потім проводиться відпускання при 160...200° С, іноді - самовідпускання. Після термічної обробки поверхневий шар має
88
структуру відпущеного мартенситу (HRC 55...58), серцевина - феритоперлитну або сорбітну (HRC 20...35) структуру.
Переваги поверхневого гартування порівняно із об’ємним: менший розмір зерна і підвищена твердість; незначна деформація деталі; наявність напружень стиснення в поверхневих шарах і, як наслідок, підвищена циклічна довговічність виробів.
8.2 Завдання на підготовку до лабораторної роботи
Вивчити сутність і призначення ХТО і поверхневого гартування; сталі, що використовуються для цементації, азотування та поверхневого гартування; технологію попередньої і заключної термічної обробки; переваги поверхневого зміцнення у порівнянні із об’ємною термічною обробкою.
8.3 Контрольні запитання для самоперевірки і контролю підготовленості до лабораторної роботи
Призначення ХТО та поверхневого гартування.
Переваги ХТО та поверхневого гартування у порівнянні із об’ємною термічною обробкою.
Процеси, які проходять при ХТО.
Вплив температури насичення, тривалості процесу, хімічного складу сплаву на глибину дифузійного шару.
Сутність цементації. Речовини-постачальники вуглецю. Температура цементації, оптимальна поверхнева концентрація вуглецю.
Сталі для цементації. Термічна обробка виробів після цементації. Структура і властивості шару та серцевини після цементації та наступної термічної обробки.
Принципи підвищення твердості, зносостійкості, міцності, опору втомі після різних способів поверхневого зміцнення.
Попередня термічна обробка виробів із азотовних сталей. Сутність азотування. Сталі для азотування, температура та тривалість процесу.
Структура і властивості сталей після азотування. Вплив легувальних елементів на властивості азотованого шару. Переваги та недоліки азотування порівняно із цементацією.
Поверхневе гартування. Сталі, що використовуються для поверхневого гартування; термічна обробка після гартування; структура і властивості поверхневого шару та серцевини. Вплив прискореного нагрівання на структуру та властивості сталі.
Контрольні запитання
1. Що таке термічна обробка і з якою метою її застосовують?
2. На яких фізико-хімічних процесах ґрунтується термічна обробка сталей?
3. Які недоліки можуть виникнути при неправильному нагріванні і витримки
сталей?
4. Які основні види термічної обробки застосовують? Яких властивостей
сталей при цьому досягають? Наведіть приклади.
5. Розкрийте суть процесів відпалювання, нормалізації, гартування і відпуску
сталей. Які структури при цьому утворюються?
6. Які сталі та з яким вмістом вуглецю загартовують?
7. Що таке критична швидкість охолодження сталі?
8. Які види гартування сталей Вам відомі? Охарактеризуйте їх.
9. Що являють собою загартовуваність і прогартовуваність сталей? Від чого
вони залежать?
10. Що таке термомеханічна обробка сталей (ТМО), які є способи ТМО і для
чого їх застосовують?
11. У чому суть поверхневого гартування і де його застосувують?
12. Що таке старіння сплавів і як воно впливає на їх властивості?
13. Сутність хіміко-термічної обробки сталей, призначення і застосування.
Лабораторна робота № 1
Вивчення впливу термічної обробки на властивості і структуру вуглецевої сталі.
Мета роботи: дослідити вплив температури нагрівання для гартування на мікроструктуру і твердість вуглецевої сталі; набути практичні навички визначати температуру гартування; дослідити вплив швидкості охолодження на мікроструктуру й твердість вуглецевої сталі; дослідити перетворення, які відбуваються у загартованій вуглецевій сталі після відпуску; провести аналіз структури і властивостей після відпуску.
Теоретичні відомості
Термічна обробка – це сукупність технологічних операцій теплової дії на метал для забезпечення потрібних технологічних, механічних та фізико-хімічних властивостей виробів унаслідок зміни структури. Основними параметрами режиму термічної обробки є температура і швидкість нагрівання, час витримки при заданій температурі, швидкість охолодження. Режим будь-якої термічної обробки може бути зображений графічно в координатах "температура–час". Основними видами термічної обробки сталей є відпал I роду, відпал II роду, гартування з подальшим відпуском. Гартування – зміцнювальний вид термообробки, в результаті якого у сплавах утворюється нерівноважна (метастабільна) структура. Воно широко застосовується вмашинобудуванні для підвищенняміцності, твердості та стійкості до спрацювання сталевих деталей. Для набуття метастабільних структур сталеві деталі нагрівають і витримують при температурі існування аустеніту, а потім охолоджують зі швидкістю, яка дає змогу зафіксувати мартенсит. Мартенсит – орієнтована структура, що являє собою пересичений твердий розчин вуглецю в α-залізі. Властивості після гартування залежать від температури нагрівання, тривалості витримки, швидкості охолодження деталей тощо. Процес гартування сталі внаслідок перетворення кристалічних ґраток супроводжується збільшеннямвнутрішніх напружень, якіможуть бути більшими за границю міцності сталевої загартованої деталі. Гартують, як правило, сталі з підвищеним вмістом вуглецю, а сталі, в яких він менше 0,3 %, не гартують, оскільки в них не відбувається суттєвого підвищення твердості та міцності. Міцність сталі після гартування підвищується в міру збільшення вмісту вуглецю до 0,7 %, а потім вона залишається практично сталою на рівні приблизно 670 НВ. Загартована доевтектоїдна сталь зазвичай має структуру дрібноголчатого мартенситу з незначною кількістю залишкового аустеніту, евтектоїдна сталь – структуру мартенситу із залишковим аустенітом, а заевтектоїдна – структуру мартенситу з вторинним цементитом і залишковим аустенітом. Залежно від режиму термообробки розрізняють повне та неповне гартування сталі. Для повного гартування сталь нагрівають на 30...50 °С вище від критичної точки Ас3 (Аст), а для неповного – вище від точки Ас1 , але нижче від Ас3 (Аст).
Температура гартування визначається залежно від вмісту вуглецю
за лініями діаграми стану сплавів залізо–цементит. При нагріванні до точки 1 структура сталі не змінюється. Нагрівання до точки 2
приводить до перетворення
перліту в аустеніт і незначного розчинення фериту в аустеніті. Після гартування починаючи із цієї температури
структура сталі буде складатися з мартенситу і фериту.
Ферит зменшує твердість
і міцність сталі. Підвищення
температури гартування до
точки 3 збільшує кількість
аустеніту при нагріванні
й кількість мартенситу після
охолодження. Твердість і міцність сталізростають.
Структура сталі після нагрівання до точки 4 складається тільки з аустеніту, тому після охолодження досягаються максимальні значення твердості й міцності. Надмірне перевищення температури вище від точки Ас3 пов'язане з ростом зерна, що призводить до
зниженняміцності й опору крихкому руйнуванню.
Для доевтектоїдної сталі
застосовують повне гартування.
Для заевтектоїдної сталі застосовують неповне гартування, коли в її
структурізалишається вторинний цементит, який не розчинився. Цементит – складова міцна, тому її наявність у загартованій сталі підвищує
міцність, але знижує пластичність деталі. З метою зменшення крихкості
загартованої сталі перед гартуванням слід виконати нормалізацію або
сфероїдизацію сталі, щоб усунути цементитну сітку. Нагрівати заевтектоїдну сталь вище від критичної точки Аст (повне гартування) недоцільно,
оскільки при охолодженні в сталі утвориться великоголчатий мартенсит.
Крім того, збільшується аустенітне зерно, з поверхні виробів вигоряє вуглець і підвищуються гартівні напруження.
У практиці термообробки перетворення аустеніту часто відбувається при неперервному охолодженні сталі з різною швидкістю. Оскільки
діаграми ізотермічного перетворення аустеніту побудовано в координатах "температура–час", вони дають можливість мати якісне уявлення про характер перетворень при неперервному охолодженні сталі. Для цього
накладемо криві охолодження евтектоїдної вуглецевої сталі на її С-подібну діаграму (рис. 7.2,а). Швидкість охолодження V характеризується
нахилом кривої (одиниця швидкості охолодження – °С/с). Чим повільніше
відбувається охолодження сталі, тим більш пологою стає крива її охолодження. Перетворення аустеніту при дуже малій швидкості V1 відбувається в умовах, близьких до рівноважних, за температури, наближеної
до А1. При цьому утворюються грубодисперсні феритно-цементитні
суміші. Під час неперервного охолодження аустеніт переохолоджується
до температури нижче від точки Аr1, при цьому підвищення швидкості
охолодження зумовлює зниження температури перлітного перетворення. Ця температура характеризує нерівноважні умови перетворення сталі.
Перетворення аустеніту на перліт при неперервному охолодженні
сталі розвивається в інтервалі температур. Чим більша швидкість охолодження і менший температурний інтервал розпаду аустеніту, тим вища
дисперсність утворюванихферитно-цементитних сумішей. При невеликій
швидкості охолодження V1 утворюється перліт, при більшій V2 – сорбіт,
а при ще більшій V3 – троостит.
При значно більших швидкостях охолодження сталі, наприклад V4,
аустеніт розпадається у двох температурних інтервалах: частина його зазнає спочатку перлітного, а потім бейнітного перетворення, а залишкова частина переохолоджується до температури, що відповідає точці Мп,
і перетворюється на мартенсит. Унаслідок цього утворюється мішана
структура трооститу, бейніту та мартенситу. При швидкостях охолодження сталі спостерігаються дві критичні точки: Аr
' і Мп. Як випливає
з рис. 7.2,а, утворення суто бейнітної структури при неперервному охолодженні аустеніту вуглецевої сталі неможливе.
При надто швидкому охолодженні, наприклад зі швидкістю V5, переохолоджений аустеніт повністю зберігається до лінії точок Мп і перетворюється на мартенсит. Нижче від точки Мп дифузійна рухливість атомів
вуглецю стає дуже малою. У цих умовах перетворення аустеніту відбувається бездифузійним шляхом: кристалічні ґратки Feγ завдяки кооперативному (одночасному) зміщенню однієї чи кількох суміжних площин
атомів заліза перетворюються на ґратки Feα. Оскільки дифузійні процеси загальмовані, весь вуглець, розчинений в аустеніті, залишається
в ґратках Feα. Розчинність вуглецю в аустеніті значно більша (максимум
у 100 разів), ніж у фериті, тому утворюється пересичений твердий його
розчин в α-залізі, який називається мартенситом. Мартенситне перетворення сталізавершується після досягнення температури, що відповідає точці Мк. Це перетворення відбувається в сталі при її гартуванні.
При утворенні мартенситу ґратки Feα дуже спотворюються, перетворюючись із кубічних на тетрагональні. Це дуже міцна та тверда структурна складова сталі, разом із цим і крихка. Велика твердість мартенситу
пояснюється значними внутрішніми напруженнями в його ґратках,
зумовленими надмірно розчиннимвуглецем, подрібненнямблокової структури його зерна та високою щільністю дислокацій. Властивості мартенситу залежать від вмісту вуглецю в ньому: зі збільшенням вмісту вуглецю твердість, а в деякому інтервалі й границя міцностізростають, а пластичність та ударна в'язкість збігаються.
Для розроблення технології термічної обробки крім діаграм ізотермічного розпаду аустеніту використовують термокінетичні діаграми. За
цими діаграмами можна отримувати точні дані про температурні інтервали проходження фазових перетворень при безперервному охолодженні
й структурні складові, які при цьому утворюються. Термокінетичні діаграми також будують у координатах "температура–час" на основі аналізу
серії кривих охолодження, на яких відмічають температури початку
і кінця перлітного й проміжних перетворень і відповідної області цих перетворень (рис. 7.3). Тонкі лінії на діаграмі для евтектоїдної сталі відпо-відають діаграмі ізотермічного перетворення переохолодженого аустеніту.Ці діаграми показують, що при малих швидкостях охолодження
у вуглецевій сталі проходить тільки дифузійний розпад аустеніту з утворенням феритно-цементитної структури різного ступеня дисперсності.
При високих швидкостях охолодження, вищих від критичної, дифузійний
розпад аустеніту пригнічується і проходить мартенситне перетворення.
У легованій сталі існує також область проміжного бейнітного перетворення, в якій аустеніт розпадається з утворенням бейніту. Прискорення
швидкості охолодження пригнічує перлітне перетворення і приводить до
утворення бейніту. Проміжне перетворення не проходить до кінця, тому
після охолодження разом з бейнітом завжди будуть присутні мартенсит
ізалишковий аустеніт.
Мінімальна швидкість охолодження сталі, яка забезпечує утворення суто мартенситної структури, називається критичною швидкістю
гартування (Vкр). Її можна визначити графічно, провівши дотичну до
кривої початку ізотермічного перетворення сталі біля її виступу. Числове значення критичної швидкості гартування сталі можна знайти за формулою.
Дійсна критична швидкість гартування сталі приблизно в 1,5 рази
менша, ніж визначена графічно. Це і враховується коефіцієнтом у знаменнику формули.
Значення критичної швидкості гартування залежать від стійкості
аустеніту. Чим вона вища, тобто чим правіше зсунуті криві на С-подібній
діаграмі, тим менша критична швидкість гартування сталі. Отже, її значення залежить від вмісту вуглецю в сталі.
В області температур, розташованих вище від точки Тm, вигідним
є охолоджування сталі з помірною швидкістю. Для середньовуглецевих
сталей область мінімальної стійкості лежить між 650 і 500 °С. При вищих температурах аустеніт відносно стійкий і передчасне перетворення
його на феритно-перлітну суміш не відбувається. У той же час при плавному охолодженні сталі в області високих температур вирівнюється температура по перерізу і зменшуються температурні напруження. Сталь
ще досить пластична, тому ймовірність короблення сталевих виробів та
утворення тріщин мінімальна.
Повільне охолодження сталі бажане також в області, розташованій
нижче від інтервалу температур мінімальної стійкості аустеніту, оскільки
в цій області його стійкість знову підвищується. При температурі 300 °С
і нижче швидке охолодження сталі особливо небезпечне внаслідок того,
що вона стає не такою пластичною, ніж при високих температурах.
Термічні напруження в сталі додаються до напружень, які виникають
при перетворенні аустеніту на мартенсит. Тому при швидкому охолодженні підвищується небезпека утворення тріщин і короблення сталі.
Швидкість охолодження сталевих деталей можна регулювати
застосовуючи різноманітні гартівні середовища: воду, водяні розчини
солей, кислот, лугів і полімерів, різні масла, розплавлені солі та метали,
емульсії тощо. Головною вимогою до гартівних середовищ є велика охолодна здатність в інтервалі температур 650...550 °С і зменшена охолодна здатність при 300 °С та нижче.
Відпуск сталі належить до завершальних операцій її термообробки
і здійснюється після гартування. Ним усувають надмірну крихкість
загартованої сталі та отримують структуру, стійкішу при звичайній температурі. Крім того, відпуск повністю або частково усуває внутрішні
напруження, що виникають при гартуванні. Ці напруження знімаються
тим швидше, чим вища температура. Відпуск сталі полягає в тому, що
загартовані деталі нагрівають до температури, нижчої за межу структурних перетворень (А1), витримують і потім охолоджують з довільною
швидкістю.
Відпуск вуглецевих сталей супроводжується структурними змінами
передусім у кристалах мартенситу. Першою причиною таких змін є утворення в мартенситі ділянок з неоднорідною концентрацією (сегрегацій)
вуглецю.
Утворення кластерів (плоских скупчень атомів вуглецю одноатомної товщини) проявляється при температурі до 100...150 °С у мартенситі
сталей із вмістом вуглецю більше ніж 0,7 %. Скупчення атомів вуглецю
зумовлює зміщення атомів заліза, що призводить до спотворення ґраток
мартенситу.
Наступною структурною зміною під час відпуску сталі можна вважати виділення проміжних карбідів з мартенситу. Експериментально
виявлено при температурі приблизно 100 °С метастабільну структуру
ξ-карбіду з імовірною формулою Fe2,4C. Цей карбід має гексагональні
кристалічні ґратки на відміну від ромбічних ґраток цементиту. Не виділяється ξ-карбід у сталях з концентрацією вуглецю менше 0,2 %, тому
що під час відпуску більшість атомів вуглецю зв'язані з дислокаціями.
При температурі вище 250 °С і в інтервалі температур 300...400 °С
дуже активно відбувається утворення більш стабільної структури цементиту Fe3C. Вона близька до структури цементиту відпаленої сталі.
До завершальних процесів карбідоутворення під час відпуску сталі
належать процеси, незв'язані з фазовими перетвореннями: коагуляція
і сфероїдизація цементиту. Його частинки набувають круглої форми
і збільшуються в розмірах.
Відпуск високовуглецевих сталей супроводжується розпадом залишкового аустеніту, який при гартуванні цих сталей утворюється у великій кількості. Його розпад спостерігається в інтервалі температур 200...
...300 °С. При відпуску сталі залишковий аустеніт перетворюється на
нижній бейніт.
Під час відпуску сталі відбувається також зміна стану матричної
фази, що спостерігається у всьому температурному інтервалі та характеризується зменшенням вмісту вуглецю в α-розчині при виділенні карбідної фази.
Важливими процесами, що відбуваються в α-фазі під час відпуску
сталі, також є повернення і рекристалізація.
Структура відпущеної сталі формується в період витримки при температурі відпуску, тому інтенсивність наступного охолодження не зумовлює яких-небудь змін у ній. Як правило, сталеві деталі охолоджують на
спокійному повітрі.
Залежно від температури та утвореної структури металу розрізняють низький, середній та високий відпуски сталі.
Низький відпуск здійснюється нагріванням сталі до 150...250 °С
й охолодженням її з будь-якою швидкістю. Цей вид відпуску застосовують для різноманітного різального та вимірювального інструментів
з вуглецевих і низьколегованих сталей, а також деталей після обробки
їхніх поверхонь гартуванням, цементацією тощо.
Середній відпуск здійснюється нагріванням сталі до 300...450 °С,
коли мартенсит перетворюється на троостит відпуску. Такий відпуск
використовується, наприклад, при виготовленні різних сталевих деталей,
що працюють за умов тертя (пружин, ресор штампів тощо).
Високий відпуск здійснюється нагріванням сталі до 500...650 °С,
коли мартенсит перетворюється на сорбіт відпуску. Деякі сталі після
цього відпуску охолоджують у воді або маслі. Високий відпуск застосовують для деталей з конструкційних сталей, що працюють при підвищених і динамічних навантаженнях.
Процес гартування з високим відпуском називають поліпшенням
сталі. Після такої обробки сталь набуває кращого поєднання міцності та
в'язкості порівняно з відпалюванням і нормалізацією.
У сталі, обробленій на сорбіт відпуску, зменшується твердість до
250...350 НВ, знижується міцність у 1,5...2,0 рази, а пластичність і в'язкість
збільшуються в кілька разів. Відпуск при температурі 600...650 °С усуває внутрішні напруження в сталі повністю.
Нормалізація належить до досить поширених методів термічної обробки сталей. Від повного відпалу вона відрізняється тим, що охолодження сталевих виробів після витримки в печі здійснюють прискорено
на спокійному повітрі або в його струмені.
Для нормалізації сталь нагрівають до повної перекристалізації, тобто на 30…50 °С вище від критичної точки Ас3 для доевтектоїдних сталей або Аст для заевтектоїдних. Після охолодження на спокійному повітрі
сталь набуває дрібнозернистої однорідної структури, зменшуються
внутрішні напруження у виробах.
Нормалізацію найчастіше застосовують як проміжну обробку для
поліпшення структури сталі перед гартуванням. Однак іноді вона може
бути кінцевою, тому що дає можливість отримати сприятливе поєднання
властивостей міцності й пластичності.
Порядок виконання роботи
1. Визначити за діаграмою "залізо–цементит" температуру нагрівання
під гартування t
н для сталі 40. П'ять зразків помістити в піч, розрахувати
час нагрівання і витримки τв.
2. Провести охолодження зразків: три – у воді, один – у маслі, один –
на повітрі.
3. Заміряти твердість зразків після термічної обробки.
4. Провести низький, середній і високий відпуски за одним зразком
загартованої сталі. Заміряти твердість після термічної обробки.
5. Визначити за діаграмою "залізо–цементит" температуру гартування для сталі У12. Три зразки помістити в піч, розрахувати час нагрівання і витримки.
6. Провести охолодження зразків: один – у воді, один – у маслі, один
– на повітрі.
7. Заміряти твердість зразків після термічної обробки.
8. Провести низький відпуск загартованого зразка. Заміряти
твердість після термічної обробки.
9. Усі дані занести у таблицю. Для сталі 40 побудувати графік залежності твердості від температури відпуску.
Вплив термічної обробки на мікроструктуру і твердість вуглецевої сталі
Твердість після
термічної обробки,
HRC
Твердість після
відпуску, Написати звіт по роботі, в якому коротко сформулювати мету
роботи, проаналізувати перетворення і дати характеристику мікроструктурам, які утворилися при різних видах термічної обробки, описати експериментальну частину, навести таблиці, графіки.
Прилади, матеріали та інструменти
Для проведення роботи необхідно мати муфельну піч, баки з водою і маслом для охолодження, пристрій типу Роквелла, зразки сталі 40 і У12; шліфувальну шкурку.
Контрольні запитання
1. Що таке гартування сталі?
2. Як визначити температуру нагрівання для гартування доевтектоїдної та заевтектоїдної сталей?
3. Як змінюється структура доевтектоїдної сталі при нагріванні в інтервалі Ас1...Ас3?
4. Чому після гартування з міжкритичного інтервалу температур з підвищенням температури твердість зростає?
6. Чому для доевтектоїдних сталей проводять повне, а для заевтектоїдних – неповне гартування?
7. Чим відрізняються перліт, сорбіт і троостит?
8. Які охолодні середовища застосовують під час гартування сталі?
9. Що таке критична швидкість охолодження?
10. Які властивості має сталь з мартенситною структурою?
11. Що таке відпуск сталі, для чого його застосовують і які його види існують? Як змінюється структура сталі внаслідок її відпуску?
12. Чим відрізняється нормалізація від відпалу?
Увага!Перейдіть за ссилкою, відкрийте збірник лабораторних робіт та виконайте лабораторну роботу №7.
http://eir.nuos.edu.ua/xmlui/bitstream/handle/123456789/765/Dubovij_Materialoznavstvo.pdf?sequence=1
Випробування на втомленість.Поняття про витривалість металу
Методи визначення механічних властивостей металів поділяють на такі групи:
- статичні, коли навантаження зростає повільно і плавно (випробування на розтяг, стиск, згин, крутіння, твердість);
- динамічні, коли навантаження зростає з великою швидкістю (випробування на ударний згин);
- циклічні, коли навантаження багаторазово змінюється (випробування на втому);
- технологічні — для оцінки поведінки металу при обробці тиском (випробування на згин, перегин, видавлювання).
Випробування на розтяг (ГОСТ 1497—84) проводяться на стандартних зразках круглого або прямокутного перерізу. При розтязі зразок деформується під дією навантаження, яке плавно зростає до моменту його розривання. Під час випробування зразка знімають діаграму розтягу (рис. 1.36, а), яка фіксує залежність між силою Р, що діє на зразок, і викликаною нею деформацією Δl (Δl — абсолютне видовження).
В'язкість (внутрішнє тертя) — здатність металу поглинати енергію зовнішніх сил при пластичній деформації і руйнуванні (визначають величиною дотичної сили, прикладеної до одиниці площі шару металу, який підлягає зсуву).
Пластичність — здатність твердих тіл необернено деформуватися під дією зовнішніх сил.
При випробуванні на розтяг визначають:
- σв — границю міцності, МН/м2 (кг/мм2):
- σпц — границю пропорційності, МН/м2 (кг/мм2):
- де Pпц — навантаження, що відповідає границі пропорційності;
- σпр — границю пружності, МН/м2 (кг/мм2):
- σт — границю плинності, МН/м2 (кг/мм2):δ — відносне видовження, %,де l0 — довжина зразка до розривання, м; l1 — довжина зразка після розривання, м;ψ — відносне звуження, %:де F0 — площа перерізу до розривання, м2; F1 — площа перерізу після розривання, м2.
Випробовування на твердість.
Випробовування за Брінеллем (ГОСТ 9012—83) проводяться шляхом вдавлювання в метал сталевої кульки. У результаті на поверхні металу утворюється сферичний відбиток (рис. 1.37, а). Твердість за Брінеллем визначається за формулоюде P — навантаження на метал, Н; D — діаметр кульки, м; d — діаметр відбитка, м.Чим твердіший метал, тим менша площа відбитка.Діаметр кульки і навантаження встановлюють залежно від металу, який досліджують, його твердості та товщини. При випробуванні сталі та чавуну вибирають D = 10 мм і P = 30 кН (3000 кгс), при випробуванні міді та її сплавів D = 10 мм і P = 10 кН (1000 кгс), а при випробуванні дуже м'яких металів (Аl, бабітів та ін.) D =10 мм і P = 2,5 кН (250 кгс). При випробуванні зразків товщиною менше 6 мм вибирають кульки з меншим діаметром — 5 і 2,5 мм. На практиці користуються таблицею переведення площі відбитка у число твердості.Метод Брінелля не рекомендовано застосовувати для металів твердістю понад Н 450 (4500 МПа), оскільки кулька може деформуватися, що спотворить результати випробувань.Випробування за Роквеллом (ГОСТ 9013—83). Здійснюють шляхом вдавлювання в метал алмазного конуса (α = 120°) або сталевої кульки (D = 1,588 мм або 1/16", рис. 1.37, б). Прилад Роквелла має три шкали — В, С і А. Алмазний конус застосовують для випробування твердих матеріалів (шкали С і А), а кульку — для випробування м'яких матеріалів (шкала В). Конус і кульку вдавлюють двома послідовними навантаженнями: попереднє Р0 і загальне Р:Р = Р0+ Р1,де Р1 — основне навантаження.Попереднє навантаження Р0 = 100 Н (10 кгс). Основне навантаження складає 900 Н (90 кгс) для шкали В; 1400 Н (140 кгс) для шкали С і 500 Н (50 кгс) для шкали А.- Твердість — це опір матеріалу проникненню в нього іншого, твердішого тіла. З усіх видів механічного випробування визначення твердості є найпоширенішим.
Рис. 1.37. Схема визначення твердості:
- а — за Брінеллем; б — за Рoквеллом; в — за ВіккерсомТвердість за Роквеллом вимірюють в умовних одиницях. За одиницю твердості приймають величину, що відповідає осьовому переміщенню наконечника на відстань 0,002 мм. Твердість за Роквеллом обчислюють у такий спосіб:НR = 100 – e (шкали А і С); НR = 130 – e (шкала В).Залежно від шкали твердість за Роквеллом позначають НRВ, НRС, НRА.Випробування за Віккерсом (ГОСТ 2999—83). В основу методу покладено вдалювання в поверхню (шліфовану чи навіть поліровану), що підлягає випробуванню, чотиригранної алмазної піраміди (α = 136°) (рис. 1.37, в). Метод використовують для визначення твердості деталей малої товщини і тонких поверхневих шарів, які мають високу твердість.Твердість за Віккерсом:де Р — навантаження на піраміду, Н; d — середнє арифметичне двох діагоналей відбитка, виміряних після зняття навантаження, м.Число твердості за Віккерсом визначають за спеціальними таблицями по діагоналі відбитка d. При вимірюванні твердості застосовують навантаження від 10 до 500 Н.Мікротвердість (ГОСТ 9450—84). Принцип визначення мікротвердості такий самий, що і за Віккерсом, згідно зі співвідношенням:
.
Метод застосовують для визначення мікротвердості виробів дрібних розмірів і окремих складових сплавів. Прилад для вимірювання мікротвердості — це механізм вдавлювання алмазної піраміди та металографічний мікроскоп. Зразки для вимірювань мають бути підготовані так само ретельно, як мікрошліфи.
Рис. 1.38. Випробовування на твердість
Випробовування на ударну в'язкість.
Для випробовування на удар виготовляють спеціальні зразки з надрізом, які потім руйнують на маятниковому копрі (рис. 1.39). Загальний запас енергії маятника витрачатиметься на руйнування зразка і на підйом маятника після його руйнування. Тому якщо із загального запасу енергії маятника вилучити частину, яка припадає на підйом (зліт) після руйнування зразка, дістанемо роботу руйнування зразка:
K = Р(h1 – h2)
або
K = Рl(соs β – соs α), Дж (кг·м),
де P — маса маятника, Н (кг); h1 — висота підйому центра маси маятника до удару, м; h2 — висота зльоту маятника після удару, м; l — довжина маятника, м; α, β — кути підйому маятника відповідно до руйнування зразка і після нього.
Рис. 1.39. Випробовування на ударну в'язкість:
1 — маятник; 2 — ніж маятника; 3 — опори
1 — маятник; 2 — ніж маятника; 3 — опори
Ударну в'язкість, тобто роботу, витрачену на руйнування зразка і віднесену до поперечного перерізу зразка у місці надрізу, визначають за формулою:
де F — площа поперечного перерізу в місці надрізу зразка, м2 (см2).
Для визначення KС користуються спеціальними таблицями, в яких для кожного кута β зазначена величина роботи удару K. При цьому F = 0,8 · 10-4 м2.
Для позначення ударної в'язкості додають і третю букву, що вказує на вид надрізу на зразку: U, V, Т. Запис KСU означає ударну в'язкість зразка з U-подібним надрізом, KСV — з V-подібним надрізом, а KСТ — із тріщиною (рис. 1.40).
Рис. 1.40. Види надрізів на зразках для випробування на ударну в'язкість:
а — U-подібний надріз (KCU); б — V-подібний надріз (KСV); в — надріз із тріщиною (KСТ)
а — U-подібний надріз (KCU); б — V-подібний надріз (KСV); в — надріз із тріщиною (KСТ)
Випробування на утомлюваність (ГОСТ 2860—84). Руйнування металу під дією повторних або знакозмінних напружень називають утомлюваністю металу. При руйнуванні металу внаслідок втоми на повітрі злом складається з двох зон: перша зона має гладку притерту поверхню (зона втоми), друга — зона долому, в крихких металів вона має грубокристалічну будову, а у в'язких — волокнисту.
При випробовуванні на втому визначають границю втоми (витривалості), тобто те найбільше напруження, яке може витримати метал (зразок) без руйнування задане число циклів. Найпоширенішим методом випробовування на втому є випробовування на згин при обертанні (рис. 1.41).
ис. 1.41. Схема випробовування на згин при обертанні:
1 — зразок; Р — навантаження; Мвиг — вигинаючий момент
1 — зразок; Р — навантаження; Мвиг — вигинаючий момент
Застосовують такі основні види технологічних випробувань (проб).
Проба на згин (рис. 1.42) у холодному та гарячому станах — для визначення здатності металу витримувати заданий загин; розміри зразків — довжина l = 5а +150 мм, ширина b = 2а (але не менш ніж 10 мм), де а — товщина матеріалу.
Рис. 1.42. Технологічна проба на згин:
а — зразок до випробовування; б — загин до певного кута; в — загин до паралельності сторін; г — загин до стикання сторін
а — зразок до випробовування; б — загин до певного кута; в — загин до паралельності сторін; г — загин до стикання сторін
Проба на перегин передбачає оцінку здатності металу витримувати повторний згин і застосовується для дроту та прутків діаметром 0,8—7 мм зі смугового та листового матеріалу товщиною до 55 мм. Зразки згинають перемінно праворуч та ліворуч на 90° з рівномірною — близько 60 перегинів за хвилину — швидкістю до руйнування зразка.
Проба на видавлювання (рис. 1.43) — для визначення здатності металу до холодного штампування та витягання тонкого листового матеріалу. Полягає у продавлюванні пуансоном листового матеріалу, затиснутого між матрицею та затискачем. Характеристикою пластичності металу є глибина видавлювання ямки, що відповідає появі першої тріщини.
Рис. 1.43. Випробовування на видавлювання:
1 — лист; h — міра здатності матеріалу до витягу
1 — лист; h — міра здатності матеріалу до витягу
Проба на навивання дроту діаметром d ≤ 6 мм. Випробовування полягає у навиванні 5—6 щільно прилеглих по гвинтовій лінії витків на циліндр заданого діаметра. Здійснюється тільки в холодному стані. Дріт після навивань не повинен мати пошкоджень.
Проба на іскру використовується при необхідності визначення марки сталі за відсутністю спеціального обладнання та маркування.
Матеріал для закріплення знань
Рис. 1.44. Технологічні проби:
а — згинання; б — перегинання; в — осаджування; г — навивання; д — видавлювання; е — проба сталі на іскру
а — згинання; б — перегинання; в — осаджування; г — навивання; д — видавлювання; е — проба сталі на іскру
- Назвіть основні характеристики механічних властивостей металів.
- Назвіть групи випробовувань механічних властивостей металів.
- У чому полягає суть випробовування на розтяг?
- Що таке в'язкість і пластичність твердих тіл?
- Що таке твердість?
- Чим користуються при визначенні твердості за Брінеллем?
- Як позначають твердість за Роквеллом?
- Коли доцільно застосовувати метод Віккерса?
- Які прилади використовують для вимірювання мікротвердості?
- Поясніть мету та суть випробовування на ударну в'язкість.
- Назвіть основні види технологічних проб металів.
Схема
випробування на втомленість
Основним параметром, який визначають при випробуванні на втому є границя витривалості матеріалу — найбільше напруження, яке витримує матеріал без руйнування при повторенні заздалегідь заданого числа циклів. Границю витривалості визначають за допомогою випробувань серій однакових зразків (не менше 10 шт. на один рівень навантаження) при циклічному прикладанні навантаження[2]:
- в умовах згинання, скручування, розтягнення—стиснення або комбінованого навантаження;
- при симетричних або асиметричних циклах напружень або деформацій;
- за наявності або відсутності концентрації напружень;
- за нормальної, підвищеної або пониженої температур;
- за наявності або відсутності агресивного середовища;
- у багато- або малоцикловій пружній та пружнопластичній зонах деформування.
Випробування проводять[2]:
- на зразках круглого перерізу (діаметр d робочої частини 5,0; 7,5; 10; 12; 15; 20 або 25 мм) з торовидною (R≥5d) або циліндричною (l = 5d) формою робочої частини (тип I і тип II, відповідно);
- на плоских зразках товщиною h до 10 мм з профілем робочої частини, виконаним по дугових лініях із шириною у найвужчому місці b=10h але не більшою за 30 мм при циклічному згинанні у площині розміру h та на плоских зразках товщиною h=3…20 мм із шириною у найвужчому місці b=(0,5…2)h при циклічному згинанні у площині розміру b (тип III);
- на плоских зразках товщиною h до 10 мм з прямолінійним профілем робочої частини шириною b=10h але не більшою за 30 мм та довжиною в умовах циклічного згинання у площині розміру h (тип IV);
- на циліндричних зразках круглого перерізу з діаметром D робочої частини 5,0; 7,5; 10 або 12 мм з концентратором у вигляді кільцевої V-подібної виточки на робочій частині глибиною t=0,25D в умовах циклічного згинання, кручення або розтягування—стискання (тип V);
- на зразках з призматичною формою робочої частини з розмірами перерізу H=b 10, 15 або 20 мм з концентратором у вигляді двох поперечних симетрично розташованих рівців V-подібного профілю глибиною t=0,25H в умовах циклічного розтягування—стискання або згинання у площині розміру H (тип VI);
- на плоских зразках товщиною h до 3 мм з шириною робочої частини b=10h та товщиною h=3…10 мм з шириною робочої частини b=5h з наскрізним отвором діаметром d=0,1b, виконаним на осі робочої частини в умовах розтягування—стискання або згинання у площині розміру h (тип VII);
- на циліндричних зразках круглого переріз з діаметром D робочої частини 6; 9; 12 або 17 мм з концентратором у вигляді кільцевої радіусної виточки з радіусом і глибиною r=t=0,5 мм (для D=6 мм); 0,75 мм (для D=9 мм) та 1 мм (для D=12 або 17 мм) (тип VIII);
- на плоских зразках шириною B=40 мм і товщиною h до 10 мм з двома симетрично розташованими отворами радіусом ρ 3 або 1,5 мм і боковими прорізами до них в умовах розтягування—стискання (тип IX);
- на плоских зразках шириною B=40 мм і товщиною h до 10 мм з двома симетрично розташованими боковими надрізами V-подібного профілю глибиною 10 мм кожний в умовах розтягування—стискання (тип X).
Типи робочих частин зразків для випробувань на втому за ГОСТ 25.502-79






Машини для випробувань на втому мають забезпечувати навантажування зразків за однією або декількома схемами, поданими на рисунках.


При випробуванні зразків допускається м'яке і жорстке навантажування. В межах наміченої серії випробувань усі зразки навантажують одним способом і випробують на однотипних машинах.
Випробування зразків проводять безперервно до утворення тріщини заданого розміру, повного руйнування або до досягнення базового числа циклів. Допускаються перерви в випробуваннях з урахуванням умов їх проведення та обов'язковим оцінюванням впливу перерв на результати випробувань. У процесі випробування зразків контролюють стабільність задання навантажень (деформацій).
Випробування серії однакових зразків при асиметричних циклах проводять:
- або за однакових для усіх зразків середніх напружень (деформацій) циклу;
- або за однакового для усіх зразків коефіцієнта асиметрії циклу.
Для побудови кривої розподілу довговічності та оцінювання середнього значення і середнього квадратичного відхилення логарифма довговічності на заданому рівні напружень випробують серію обсягом не менше 10 однакових зразків до повного руйнування або утворення макротріщин.
Технологічні властивості, технологічні проби.
Технологічні властивості визначають здатність металів отримувати ту чи іншу обробку. До технологічних властивостей металів належать: обробка різанням, ковкість, рідкотекучість, усадка, зварюваність.
Ковкістю (malleable) називається здатність металів, не руйнуючись, приймати потрібну форму під дією зовнішніх сил. Сталь у нагрітому стані має хорошу ковкість.
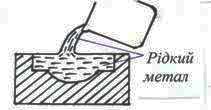
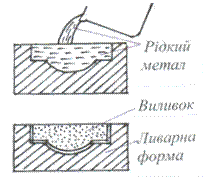
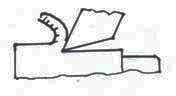
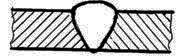
Метали і сплави мають різні властивості, а не знаючи властивостей не можна зробити висновок про їх використання. Властивості металів визначають за сертифікатами, паспортами і за результатами лабораторних випробувань, які називаються технологічними пробами.
Технологічними пробами визначають здатність металів або виробів витримувати той чи інший вид обробки. Проби можуть бути проведені безпосередньо на робочому місті найпростішими приладами та інструментами.
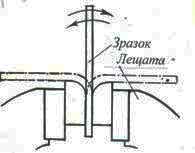
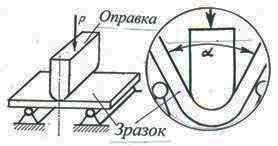
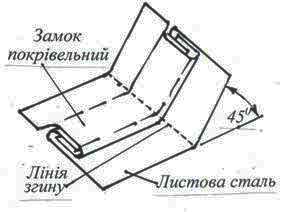
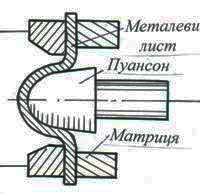
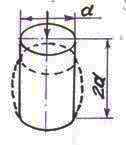
Проба на іскру дозволяє приблизно визначити хімічний склад (марку) сталі. При оброблені сталі шліфувальним кругом на заточувальному верстаті утворюються іскри. Кожна марка сталі має свій колір і форму іскри :
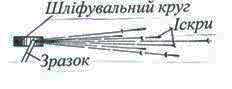
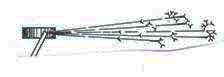
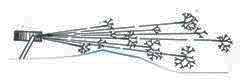
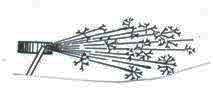
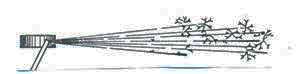
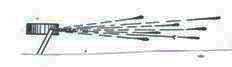
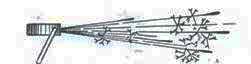
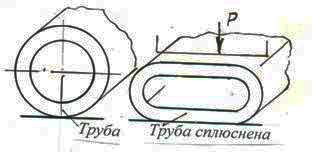
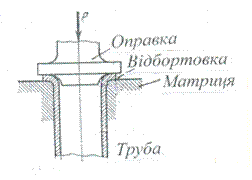
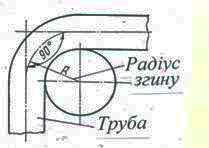
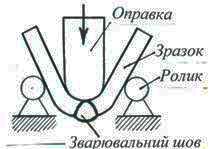
Питання для самоконтролю
1. Як називають властивість матеріалів чинити опір зовнішнім силам?2. Що таке твердість? Густина?
3. В чому полягає суть способу визначення твердості металу за Бринелем?
4. Як перевіряють твердість металів способом Роквелла?
5. Що характеризують технологічні властивості матеріалів?
6. Назвіть відомі вам види навантажень, які діють на деталі.
7. Назвіть основні технологічні властивості металів?
8. Які властивості відносять до фізичних?
9. З якою метою проводять технологічні проби металів?
10. Яким чином і навіщо випробовувати штабовий метал на перегин?
11. Як проводять пробу на подвійний покрівельний замок? Для якого матеріалу проводять цю пробу?
12. Як проводять іскрову пробу сталі і що за допомогою неї можна визначити?
13. Як і для чого застосовують пробу сталевих труб на бортування і сплющування?
14. Як випробовують сталеві труби на загин?
15. За якими ознаками бракують труби при їх технологічних пробах?
10. Яким чином і навіщо випробовувати штабовий метал на перегин?
11. Як проводять пробу на подвійний покрівельний замок? Для якого матеріалу проводять цю пробу?
12. Як проводять іскрову пробу сталі і що за допомогою неї можна визначити?
13. Як і для чого застосовують пробу сталевих труб на бортування і сплющування?
14. Як випробовують сталеві труби на загин?
15. За якими ознаками бракують труби при їх технологічних пробах?
Тестові завдання для перевірки знань ви знайдете за посиланням:
Шановні учні!Опрацюйте даний матеріал,дайте відповіді на запитання.
ВідповістиВидалити